Vi. trouble shooting guide – Spencer Single-Stage Scroll Blowers User Manual
Page 10
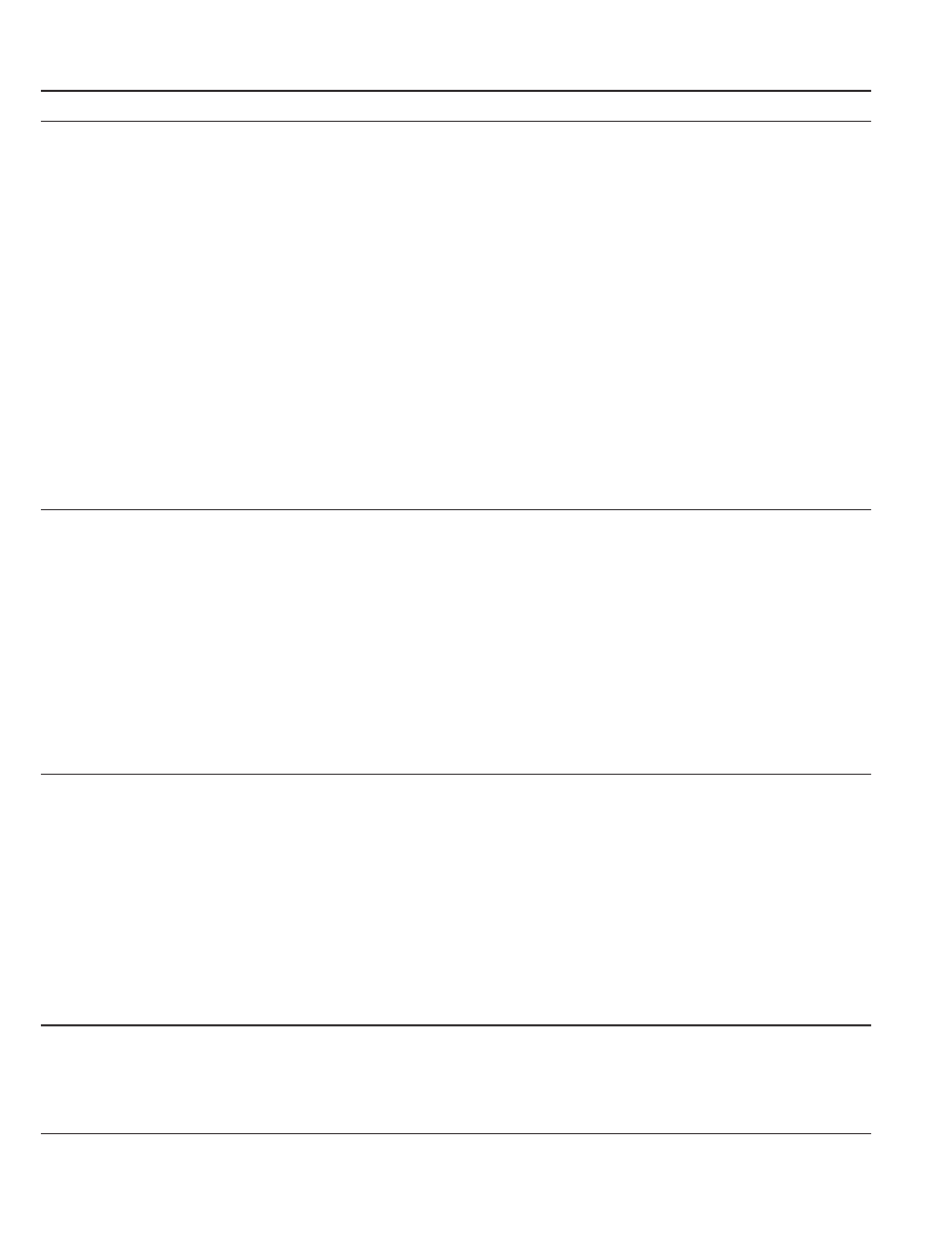
VI. Trouble Shooting Guide
Trouble
Probable Cause
Corrective Action
Insufficient air
Low pressure or vacuum as determined by measurement with a manometer:
through system
– Incorrect rotation.
Change motor leads to correct rotation.
– Machine sized for requirements given, but air lines too small
Increase line sizes or install machine providing higher
causing excessive frictional loss.
output pressure.
– Valves in line, causing excessive losses.
Install larger valves or install machine providing higher
output pressure.
– Inlet or outlet partially blocked, i.e., clogged inlet filter,
Check blast gate; remove and repair if necessary.
blast gate shaft slipped in handle and shutter does not open fully.
– High inlet temperature, i.e., higher than designed inlet
Direct inlet line to cooler area; replace machine with
temperature.
one designed for correct temperature.
– Lower inlet pressure, i.e., lower than designed inlet pressure.
Remove inlet restrictions or install machine providing
higher output pressure.
– Machine not running at designed speed.
Refer to motor manufacturer’s instructions; check
motor speed; check voltage connections.
– Lower than design gas density or specific gravity.
Check gas analysis; increase density or install machine
designed for correct requirements.
– Machine air passages clogged with material.
Disassemble, clean and inspect all parts.
– Fans worn out due to explosion, abrasion, or vibration.
Replace fan(s).
– Pressure or vacuum gauge inaccurate – would not apply to
Calibrate gauge; always use a “U” tube manometer for
performance of machine, but to gauge reading only.
checking pressure and/or vacuum.
Machine design capacity too small for the system:
– System requirements incorrectly calculated by customer.
Install larger volume or lower vacuum machine to
handle correct system requirements.
– Too many leaks and/or openings.
Locate and repair all leaks.
Measuring gas or air flow incorrectly:
– Flowmeters incorrectly calibrated.
Calibrate flowmeters; be certain proper orifice is used
for meter (check with flowmeter manufacturer).
– No means of measurement available so customer is
Obtain and install flowmeter.
guessing at airflow.
Machine noisy
Internal machine malfunction:
– Fan hitting after customer reassembly and/or fan slipping on
Reassemble according to instructions, tighten fan. Bleed air at
shaft due to heat or excessive inlet pressure.
low flow to reduce heat. Change inlet conditions if necessary.
– Fan coming apart due to age or wear from dirty air or gas.
Replace fan.
– Machine out of balance running rough.
Rebalance and/or clean machine (refer to
“Machine Vibrating”).
– Foreign material in machine.
Disassemble machine, inspect and clean. Reassemble and, if
necessary, install filter to prevent further clogging.
Motor malfunctions:
– Excessive electrical hum or whine.
Check motor manufacturer’s instructions. Check voltage supply
and connections.
– Wrong voltage – low voltage motor not up to speed. High
Check for proper voltage at motor and correct.
voltage will burn out motor and also cause noticeably
more noise.
– Bearing failure.
Check manufacturer’s instructions and replace if necessary.
– Motor rebuilt improperly – thrust taken on wrong end in
Rebuild motor properly and correct end play.
standard overhung machine.
– Worn bearings or loose part.
Tighten, repair or replace (check with motor manufacturer).
– Low frequency.
Separate power supply; correct frequency.
Machine vibrating
Imbalance:
– Material build-up on Impeller.
Clean Impeller; install or improve filter to prevent further build up.
– Shaft bent.
Replace shaft.
– Faulty replacement motor installed and /or machine
Disassemble machine, balance motor, reassemble
reassembled incorrectly.
according to instruction in this book and assembly print.
– Motor bearings worn.
Replace worn bearings.
Mechanical:
– Inlet and/or outlet piping connected to machine without
Install flexible connection at inlet and outlet.
flexible connector causing torque or strain on casing.
– Machine bolted down causing change in alignment.
Remove bolts; use dowel pins or set in guide channels.
– Piping not properly supported.
Properly anchor piping beyond flexible connector.
– Improper voltage on motor causing assembly to operate
Check voltage and wiring connections; correct voltage.
at different speed.
– Solids or liquids in, or passing through machine.
Disassemble, inspect and clean machine, install or improve filter
to prevent further contamination.
– Machine not mounted on solid foundation, i.e., on
Re-inforce foundation.
unstable catwalk, etc.
Motor Hot (Can be
Incorrect motor selection:
checked with surface
– Ambient temperature too high for insulation class.
Cool motor or replace with motor having proper insulation.
thermometer. Refer
– Incorrect voltage.
Change to correct voltage.
to factory for decision
– Incorrect cycle.
Change to correct cycle.
as to whether or not
– Electrical short-circuit insulation failure.
Repair or replace motor.
it is too hot.)
– Motor overloaded – blower too small for system.
Install larger motor and/or blower.
Unbalanced voltage supply:
Check with power company for correction.
10
The Spencer Turbine Company ◆ 600 Day Hill Road, Windsor, CT 06095 ◆ TEL 800-232-4321 ◆ 860-688-8361 ◆ www.spencerturbine.com