Appendix d (continued) – Bell & Gossett 70M Multiple Pump & Control Pressure Booster Systems User Manual
Page 25
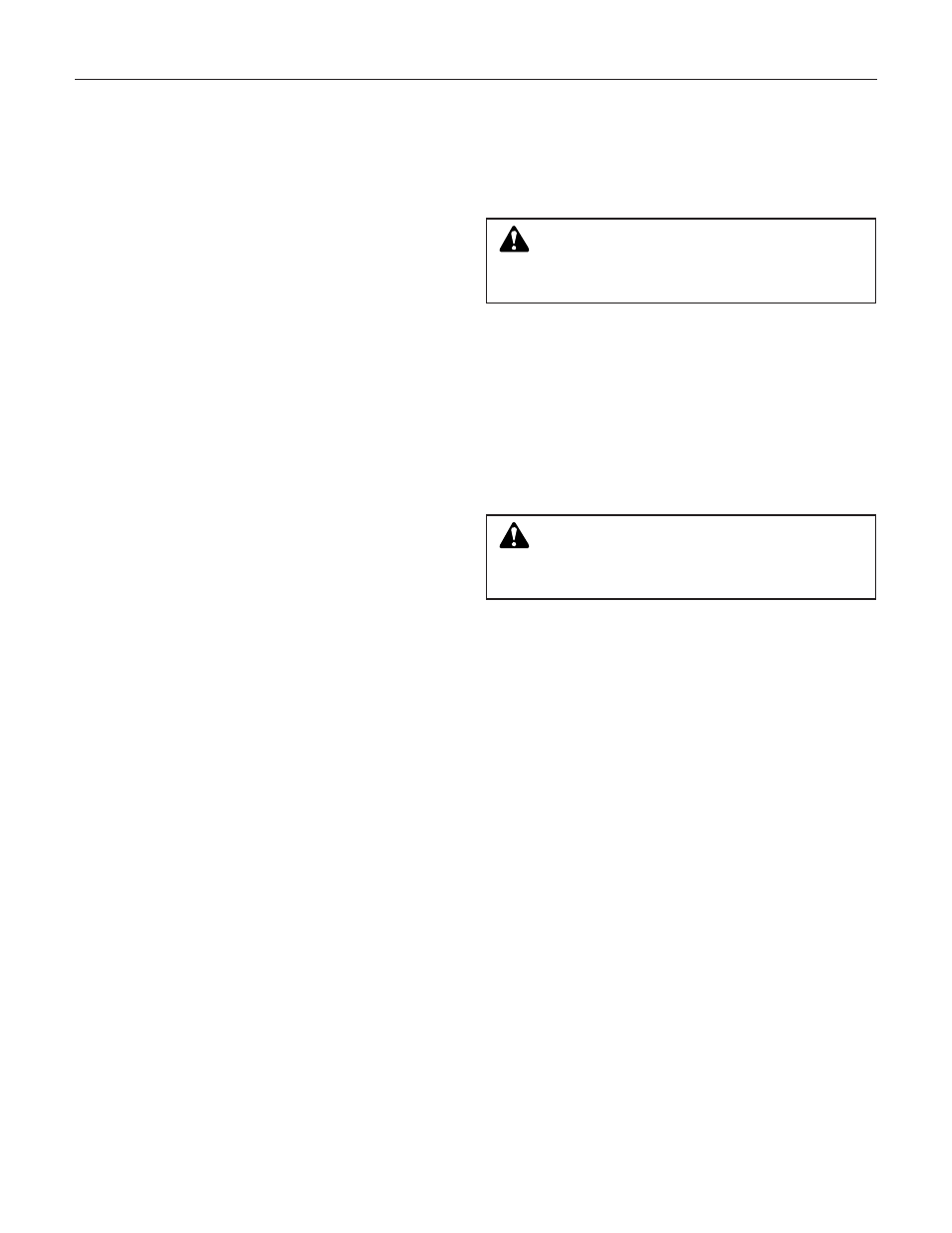
25
APPENDIX D (continued)
5.0
PRV Does Not Close (Check) on Pump Shut Down
5.1
Primary Causes
a) Insufficient pressure on top of diaphragm.
b) Leak through main valve seat or diaphragm
assembly.
5.2
Remedies (see Figure 1 for item numbers)
a) Stop cock (Item 7) closed preventing pressure
from reaching valve cover.
b) Leaking check valve (Item 2).
c) To determine whether leak is in main valve seat or
diaphragm assembly:
1. Disconnect line between flow control valve
(Item 4) and valve cover.
2. Plug flow control side.
3. Install pressure gauge in valve cover.
4. Remove vent plug in pump volute to drain inlet
side of PRV.
5. Apply pressure to top side of diaphragm by
opening shutoff valve on outlet side of PRV.
6. Read gauge pressure.
7. Close stop cock (Item 7).
If gauge pressure fails, there is a leak in the dia-
phragm assembly. This test, however, does not indi-
cate whether the seat is also leaking.
6.0
PRV Slams Shut on Pump Shut Down
6.1
Primary Causes
a) Too rapid buildup of pressure on top of diaphragm.
b) Main valve assembly binding.
c) Check valve (Item 2) sticking open momentarily.
6.2
Remedies (see Figure 1 for item numbers)
a) Throttle stop cock (Item 7).
NOTE: Closing this stop cock will completely pre-
vent PRV from functioning as a check valve.
b) Vent air from PRV (see 1.2b).
7.0
PRV Setting
7.1
Preparation in the Field
If one or more pumps must be kept running at all
times, install gauge (Item 6) or a Schraeder fitting in
each CRD. CRD has a
3
/
8
" NPT tapping.
7.2
Low Flow Setting
Since the design flow rate through each PRV is diffi-
cult to obtain, the valves should be set a very low
flow rate. Barely crack open the shutoff valve on the
outlet side of the PRV and set the CRD so the pres-
sure gauge reads 3-4 psi above the desired system
pressure.
7.3
Balancing the Settings
a) Between two or more equal pumps:
1. Check the motor amps of each pump quickly
(to reduce the possibility of load changes dur-
ing reading) with both or all equal size pumps
running simultaneously – controller in “hand” if
necessary to stabilize pump operation.
2. Select the lower reading of two equal pumps
and balance the amperage of the other pump
to that reading by lowering the CRD setting (turn
CCW) very slightly, but not more than
1
/
8
turn.
3. Select the middle reading of three equal pumps
and balance the other two pumps to that read-
ing as in Step 2 above.
4. Secure the CRD adjustment stem with the locknut.
b) Between the fixed (usually smaller) lead pump and
other pump(s):
1. Check the motor amps through pump #1 with-
out any other pumps running.
2. While observing the ampere reading of the lead
pump #1, start pump #2 in the “hand” position.
If pump #1 does not show a decrease in amp-
erage of at least one amp for a motor under 5
HP or two amps for large motors, increase CRD
#2 setting (turn CW) very slightly, usually not
more than
1
/
8
turn, to lower the amperage of
pump #1. This adjustment will assure that
pump #1 will trip out when the water demand
decreases. On three pump units, calibrate
pumps #1 and #3 as #1 and #2 above.
3. Secure the CRD adjustment stem with the locknut.
DANGER: Troubleshooting live control panels ex-
poses personnel to hazardous voltages. Electrical
troubleshooting must only be done by a qualified electri-
cian. Failure to follow these instructions could result in
serious personal injury, death, and/or property damage.
DANGER: Troubleshooting live control panels ex-
poses personnel to hazardous voltages. Electrical
troubleshooting must only be done by a qualified electri-
cian. Failure to follow these instructions could result in
serious personal injury, death, and/or property damage.