Littelfuse T4400 Series User Manual
Page 2
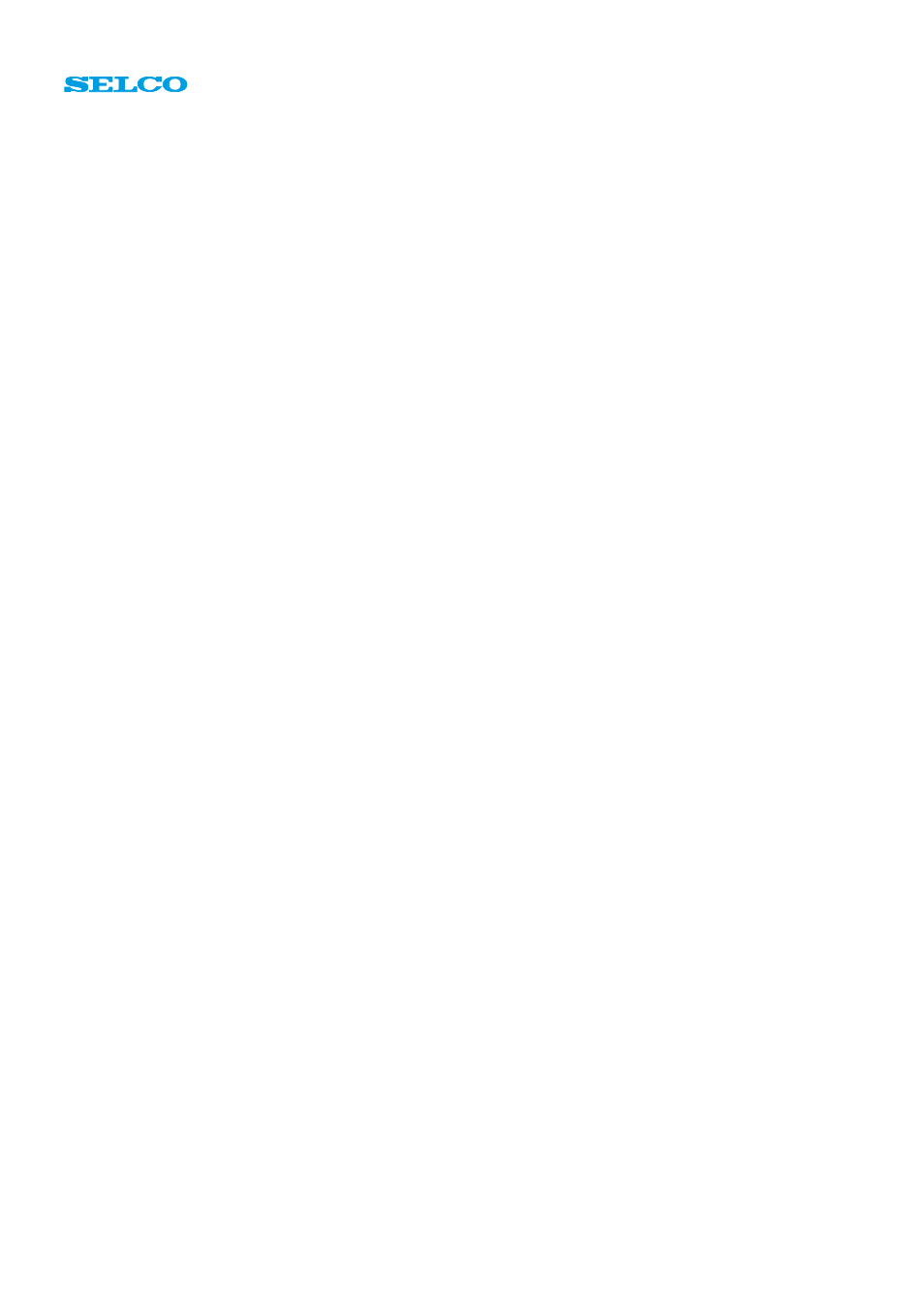
Supply voltage / current
The supply voltage from L1 and L2 is
connected to terminals 1 and 3 or 2 and
3, depending on the system voltage.
The measuring current from L3 is
connected to terminals 5 and 6 with 5
referring to the generator (see the
application diagram on page 3). The
current measurement must be taken
from the same phase on all generators.
The current is measured in the phase
that is not supplying the unit. It is
important to ensure that the phase
sequence is correct.
This relation between the connections of
voltage and current must be correct in
order to achieve a correct load measure-
ment. It can be checked on terminal 11
(TEST OUT), where an input of nominal
current (1A or 5A) and power factor 1.0
gives +6V for correct connection.
Ramp function
The T4400 includes a ramp function.
With this function activated, the unit
will smoothly take over the load up to
load balance.
In order to activate this function,
terminals 7 (UNLOAD) and 32 should
initially be bridged and so should
terminals 31 (C/B) and 32 (for example
with an aux. contact of the circuit
breaker). Now the ramp function can be
activated by opening the connection
between terminals 7 (UNLOAD) and 32.
Common reference
Terminal 12 (COM.) is the common
reference for terminals 8 to 13.
Unload facility
The unload facility will smoothly
unload the generator. This facility
works like an inverted ramp function. If
activated, the load on the generator will
be reduced and maintained at a low
level.
In order to activate, terminals 31 (C/B)
and 32 should initially be bridged. The
unload function is then activated by
connecting terminal 7 (UNLOAD) to 32.
Unload trip
When the load passes below 5% load, a
trip signal is provided as a normally
open (NO) contact on terminal 20-21
and a normally closed (NC) contact on
21-22. This trip signal can be used to
trip the circuit breaker.
Reverse power trip
The reverse power trip operates at 10%
with a delay of 10 sec., but it can be
reduced to 5% by bridging terminals 17
and 18 and to 5 sec. delay by bridging
18 and 19. A resistor of 510kW between
17 and 18 gives 7.5%, a resistor of 2.7MW
between 18 and 19 gives 7.5 sec. delay.
The trip signal is provided as a normally
open (NO) contact on term. 23-24 and a
normally closed (NC) contact on 24-25.
Frequency control
The electronic speed controller will
control the frequency of the generator.
However, the frequency control of some
speed controllers will drift with time. In
order to compensate for this, the T4400
includes frequency control.
The system frequency can be set to
60Hz with terminals 29 and 30 bridged
or 50Hz with these terminals open.
Further adjustment of the frequency is
possible using the potentiometer DIFF.
FREQ. on the front panel.
Connecting terminal 8 (FREQ. OUT) to
12 will disable the frequency control.
This is used when running parallel with
the grid, where the frequency is fixed by
the grid.
Input from synchronizer
Between terminals 9 (FREQ. IN) and 12
the SELCO T4000 Auto Synchronizer or
most other synchronizer makes can be
connected. The synchronizer will then
give the synchronizing output through
the T4400. This signal is not affected by
the output adjustments on the T4400.
External power measurement
Between terminals 10 (WATT IN) and 12
a negative voltage (0 to -1V DC from a
watt converter) can be connected to
substitute the internal load measuring
circuit. In this case no input on terminals
5 and 6 is needed. Most standard measu-
ring signals can be adapted with external
resistors.
0-10V : series resistor 510kW
0-5mA : parallel resistor 200W
Communication between load sharers
For communication between the load
sharers all terminals 12 (COM.) are
interconnected, as well as all terminals
13 (+).
Output to the speed controller
Output to the electronic speed controller
is taken from terminals 15 (REF.) and 16
(+) with terminal 15 as reference. If an
inverse signal is needed, use terminals
15 (REF.) and 14 (-) rather than changing
wires to 15 and 16. The output signal is
an integrated signal. This means, the
output signal will change as long as
there is a load deviation. When load
balance is obtained the output signal will
stay at its current level.
Adjustments
LOAD DEV.
can be used for fine adjust-
ments of the load balance. LOAD DEV.
should also be used to obtain balance
with generators of different size and with
different types of current transducers
(CTs). For generators of same size and
with same type of CT, the setting 0
should be used on all load sharers.
DIFF. FREQ.
is used for adjustment of
system frequency as described on page
2 in the section about frequency control.
If the system frequency should be
exactly 50 Hz or 60 Hz, the setting 0
should be used.
STABILITY
is used for adjusting the
regulation time. A high setting of
STABILITY will give a slow but
accurate regulation. A low setting will
give a fast regulation. However, a too
low setting may cause instability.
VARIABLE OUT
is intended for
adjusting the size of the output signal to
the speed controller. The output
increases with higher setting on the
potentiometer. Too much output can
result in instability. If this is the case,
turn the potentiometer anti clockwise
until stability is restored.
Interfacing
A detailed note on interfacing the T4000
and the T4400 to a wide number of
different electronic speed controllers is
available from SELCO. This note can
also be downloaded from our web-site
www.selco.com.
Trouble Shooting
If load balance is not obtainable
If load balance is not obtainable and the
power goes to maximum or reverse
power, one of the signals is inverted
due to wrong polarity or interchanged
wires. If this is the case, the following
should be checked:
1. The polarity of the power measuring
signals on terminal 11 (TEST OUT)
must be positive with the generator
on load. If the polarity is negative,
change the voltage connections 1 and
3 or 2 and 3 or the current connections
5 and 6.