5 fault codes – R&M Materials Handling VARIABLE SPEED CONTROLS ControlMaster Elite Manual User Manual
Page 22
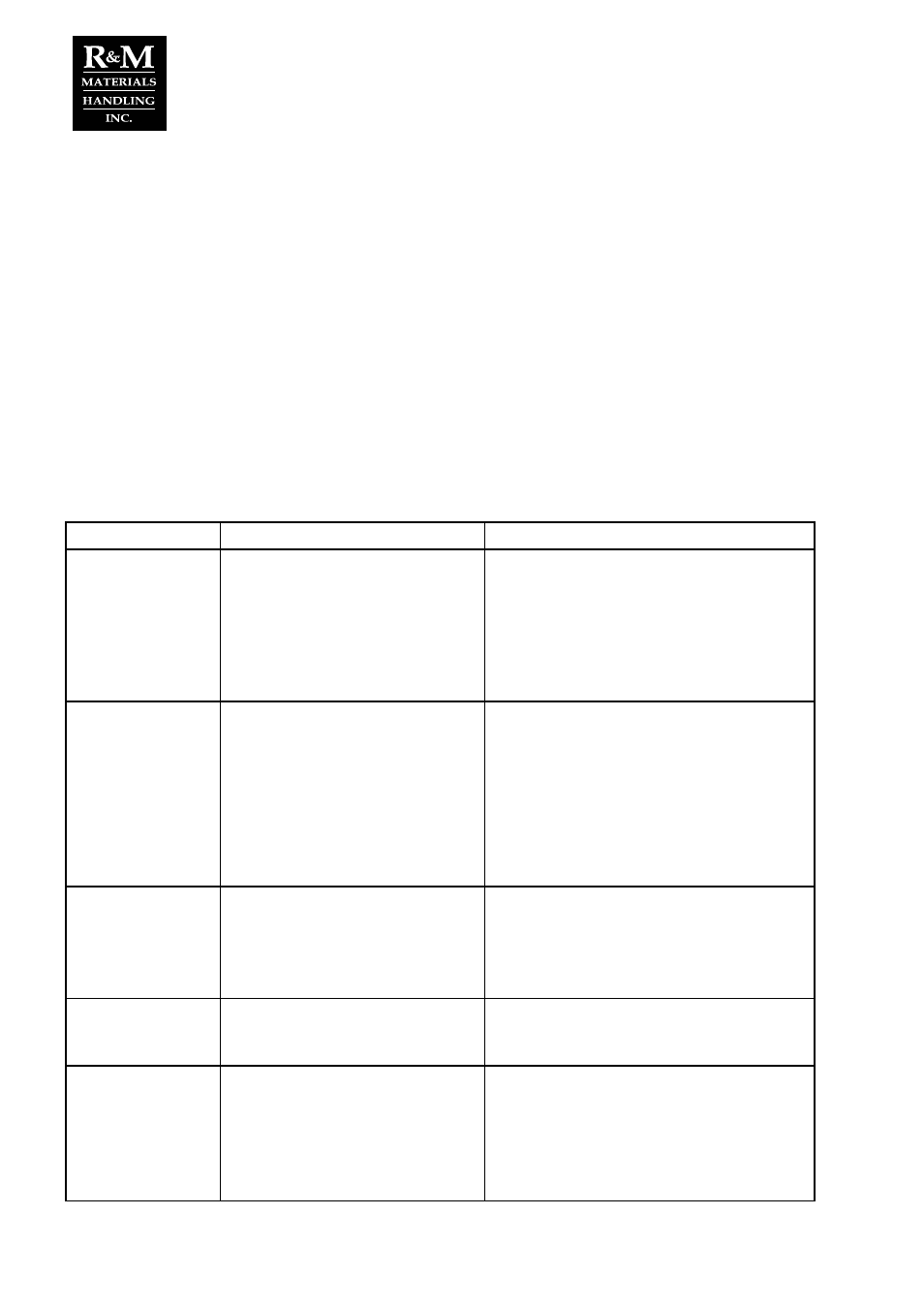
R&M Materials Handling, Inc.
4501 Gateway Boulevard
Springfield, Ohio 45502
!
: (937) 328-5100
FAX: (937) 325-5319
22/31
R&M Materials Handling, Inc. reserves the right to alter or amend the above information without notice.
5 FAULT
CODES
If any of the following failures are found, the inverter displays the fault code and closes the mechanical
brake causing the movement to stop. If several faults occur one after another, the latest one is
displayed, the others are stored to fault history page.
When inverter fault supervision trips, the FAULT indicator turns on and the blinking fault code “F xx“ (xx
= fault number) appears on the display.
D2H/D2C includes an automatic fault reset operation; the fault code stays on the display until the fault is
removed and the controller released back to 0-position. Some of the fault codes require to switch the
power off before run is possible.
The faults are stored to the fault history, from there they can be seen if necessary. The fault history can
store last 30 fault codes. Following exceptions exist when storing faults to the fault history
1. not stored faults: F6, F70
2. repeated faults are stored only once: F50, F51, F55, F60, F66, F71, F72
Fault code
Possible cause
Checking
F 1
Overcurrent
Inverter has measured too high current
(over 4*In) in the motor output:
− sudden heavy load increase
− short circuit in the motor or cable
− not suitable motor
− wrong motor parameters
Reset: switch power off and restart after the lamps
of keypad are off.
Check:
− motor cable connection
− motor and motor cable insulation
− brake operation
− motor loading
− motor type and power rating
− parameters
F 2
Overvoltage
DC-bus voltage has exceeded 135%
maximum level, 911Vdc
− supply voltage raised >1.35 x Un
(high overvoltage spikes at mains or
not sinusoidal voltage wave form)
− deceleration time is too short
Reset has an additional 5 s time delay.
Check:
− adjust the deceleration time longer
− measure main supply voltage level and wave
form while not driving
− motor insulation
− motor cable insulation (phase-ground, phase-
phase)
− braking resistor cable
− braking resistor type and resistance
− braking chopper operation
F 3
Earth fault
Current measurement has sensed
unbalance in motor phase currents.
Supervision level is 5% of inverter
nominal current
− not symmetric load
− insulation failure in the motor or the
cables
Reset has an additional 5 s time delay.
Check:
− motor insulation
− motor cable insulation (phase-ground, phase-
phase)
F 5
Charging switch
Charging switch is open when START
command becomes active
− interference fault
− component failure
Check:
− control unit and power unit connections
− charging resistors
If the fault comes again, change the control unit.
F 6
Emergency Stop
Either the ES or RDY-signal has been
tripped during run or
SSU speed supervision unit has detect
− OS overspeed supervision
− ZS stall supervision
− SD speed difference supervision
Fault is not stored into fault history.
Check:
− ES and RDY external connections
− brake operation
− pulse sensor/encoder function and cabling
− measure pulse sensor/encoder pulses with
graphical multimeter or scope
− SSU settings and SSU relay operation