7 description of the control methods – R&M Materials Handling VARIABLE SPEED CONTROLS ControlMaster Elite Manual User Manual
Page 10
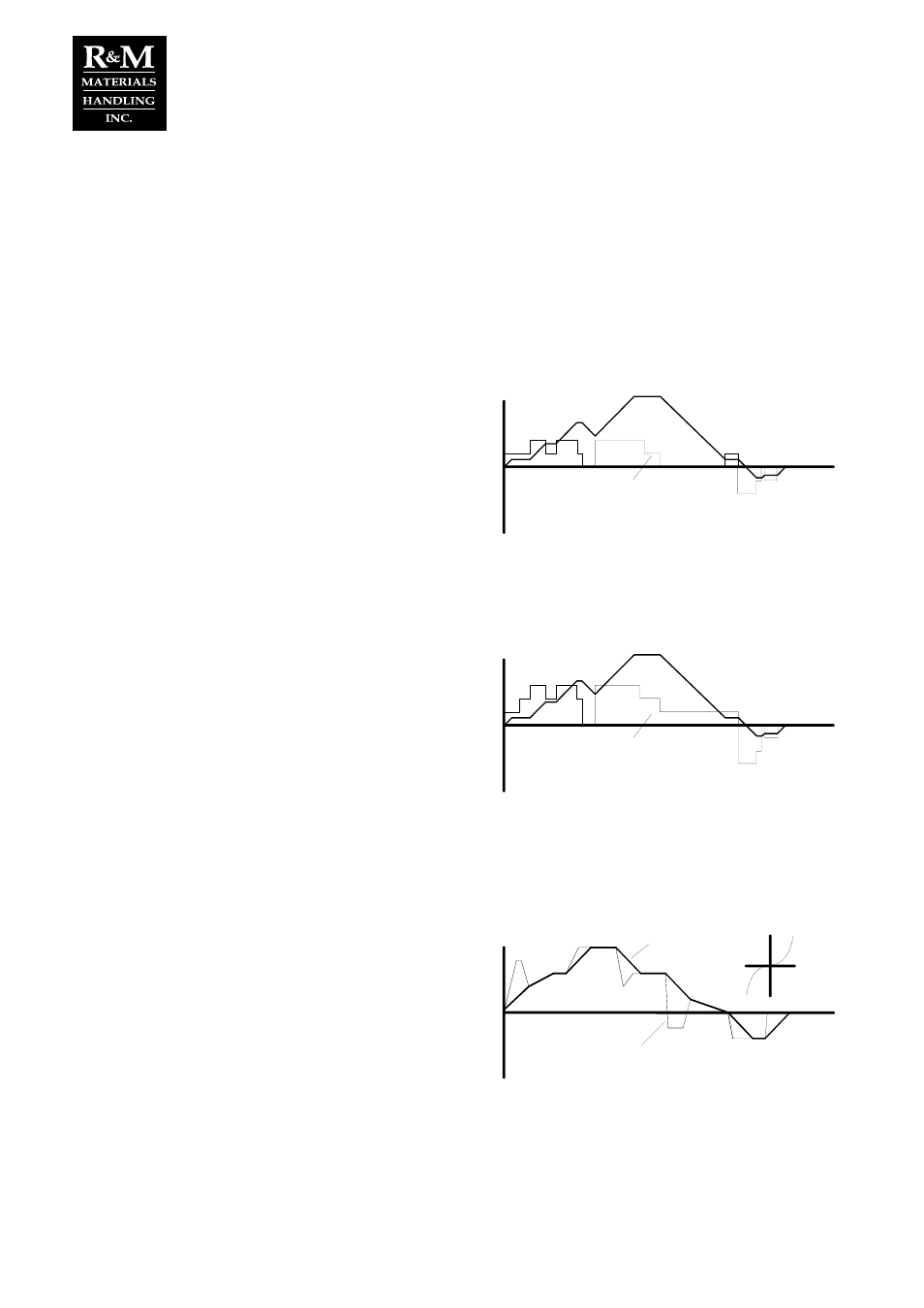
R&M Materials Handling, Inc.
4501 Gateway Boulevard
Springfield, Ohio 45502
!
: (937) 328-5100
FAX: (937) 325-5319
10/31
R&M Materials Handling, Inc. reserves the right to alter or amend the above information without notice.
Synchronization
If required, two or more D2H or D2C can be driven in precise
synchronization. A separate synchronization controller is needed for this.
The same speed reference (in EP- or PO-mode) is connected to every
D2H or D2C and the correction signal for synchronization is connected
to all D2H or D2C to input AIN2+. The speed reference signal of each
D2H or D2C can also be modified separately by a PLC. Synchronization
is activated by parameter selection.
1.7 Description of the control methods
EP-control requires two 2-step pushbuttons, one for
each direction. The operation is as follows:
− the rest position means standstill (0-position)
− during run the rest position means deceleration
− step one (switch S1 or S2) means hold speed
− when starting, step one means acceleration up to
the minimum speed
− step two (switch AP) means acceleration (up to
the maximum speed if desired)
− at the maximum speed step two means hold
speed, because the maximum speed cannot be
exceeded
Pushbutton position
rest = deceleration
step 1 = hold speed
step 2 = acceleration
speed
pushbutton
position
up / fwd
down / rev
time
EP-mode
EP3-control requires a 3-step controller. The
operation is as follows:
− the rest position means standstill (0-position)
− step one (switch S1 or S2) is the minimum speed
command
− step two (EP hold command) means hold speed
− step three (switch AP) means acceleration (up to
the maximum speed if desired)
− when releasing the controller, step one means
deceleration down to the minimum speed
speed
Pushbutton position
rest = stop
step 1 = minimum speed
step 2 = hold speed
step 3 = acceleration
pushbutton
position
up / fwd
down / rev
time
EP3-mode
PO-control requires a controller with potentiometer.
The operation is as follows:
− when the controller is at the rest position the
potentiometer is at the middle position causing
zero speed
− run commands are controlled separately by
closing the direction switches (S1 and S2)
− when the operator turns the controller to any
direction, the speed increases
− the same turning angle of the controller causes a
smaller change in speed, the closer the speed is
to the minimum speed
AU-control requires an analog reference from radio
or PLC. The operation is as follows:
− the speed linearly follows the input signal. 0V
means zero speed and the higher the voltage, the
up / fwd
down / rev
speed
speed
controller
position
time
potentiometer reference (controller position)
or auxiliary reference
PO- and AU-modes