Applications information, Table 5. low-voltage troubleshooting guide – Rainbow Electronics MAX1637 User Manual
Page 17
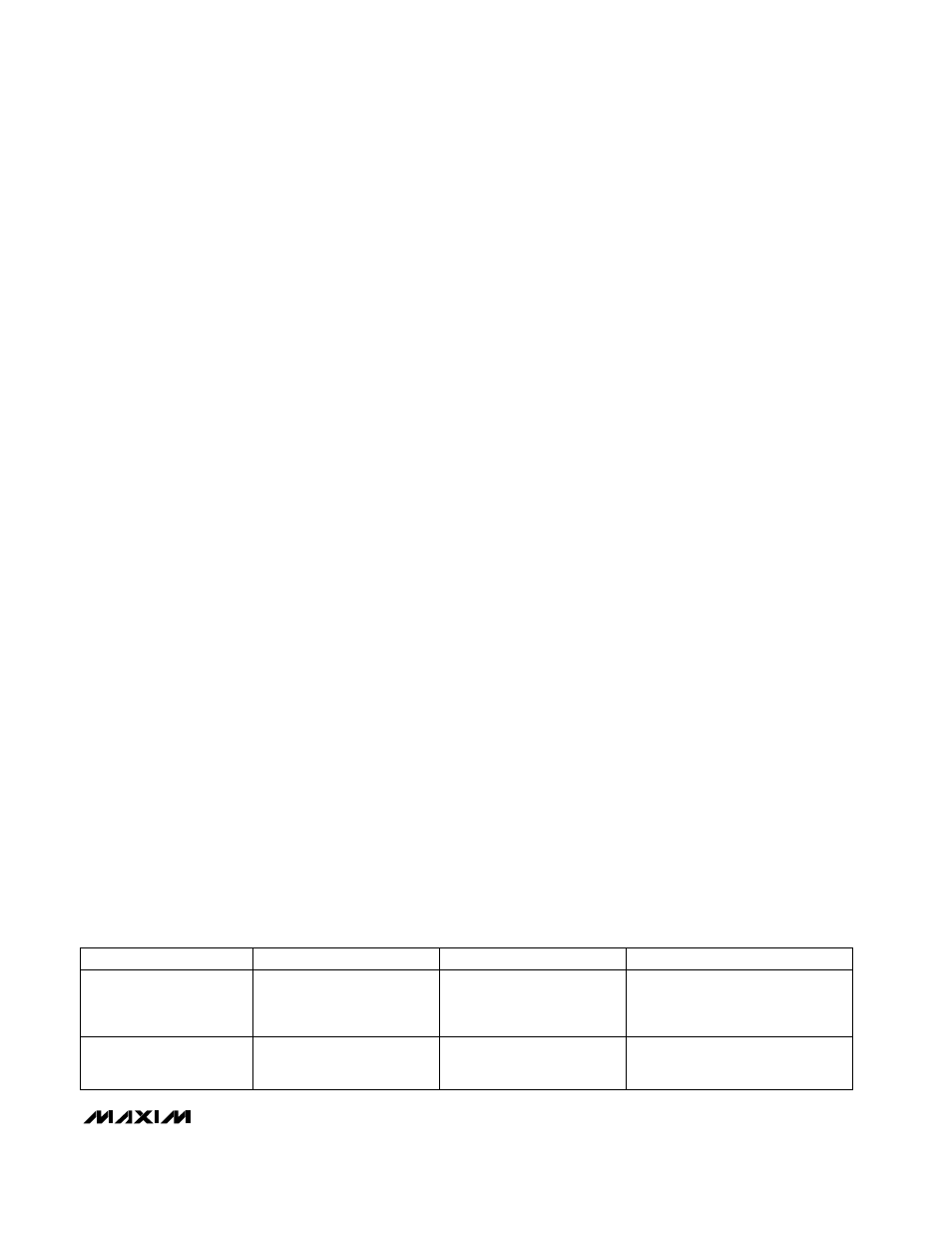
Rectifier Clamp Diode
The rectifier is a clamp across the low-side MOSFET
that catches the negative inductor swing during the
60ns dead time between turning one MOSFET off and
turning each low-side MOSFET on. The latest genera-
tions of MOSFETs incorporate a high-speed silicon
body diode, which serves as an adequate clamp diode
if efficiency is not of primary importance. A Schottky
diode can be placed in parallel with the body diode to
reduce the forward voltage drop, typically improving
efficiency 1% to 2%. Use a diode with a DC current rat-
ing equal to one-third of the load current; for example,
use an MBR0530 (500mA-rated) type for loads up to
1.5A, a 1N5819 type for loads up to 3A, or a 1N5822
type for loads up to 10A. The rectifier’s rated reverse-
breakdown voltage must be at least equal to the maxi-
mum input voltage, preferably with a 20% margin.
Boost-Supply Diode D2
A signal diode such as a 1N4148 works well in most
applications. Do not use large power diodes, such as
1N5817 or 1N4001.
Low-Voltage Operation
Low input voltages and low input-output differential volt-
ages each require extra care in their design. Low
V
IN
-V
OUT
differentials can cause the output voltage to
sag when the load current changes abruptly. The sag’s
amplitude is a function of inductor value and maximum
duty factor (D
MAX
, an
Electrical Characteristics
parame-
ter, 93% guaranteed over temperature at f = 200kHz) as
follows:
V
SAG
= [(I
STEP
)
2
x L] / [2C
F
x (V
IN(MIN)
x D
MAX
-
V
OUT
)]
Table 5 is a low-voltage troubleshooting guide. The
cure for low-voltage sag is to increase the output
capacitor’s value. For example, at V
IN
= 5.5V, V
OUT
=
5V, L = 10µH,
ƒ
= 200kHz, and I
STEP
= 3A, a total
capacitance of 660µF keeps the sag below 200mV.
Note that only the capacitance requirement increases;
the ESR requirements do not change. Therefore, the
added capacitance can be supplied by a low-cost bulk
capacitor in parallel with the normal low-ESR capacitor.
__________Applications Information
Heavy-Load Efficiency Considerations
The major efficiency-loss mechanisms under loads are
as follows, in the usual order of importance:
•
P(I
2
R) = I
2
R losses
•
P(tran) = transition losses
•
P(gate) = gate-charge losses
•
P(diode) = diode-conduction losses
•
P(cap) = capacitor ESR losses
•
P(IC) = losses due to the IC’s operating supply current
Inductor core losses are fairly low at heavy loads
because the inductor’s AC current component is small.
Therefore, these losses are not considered in this
analysis. Ferrite cores are preferred, especially at
300kHz, but powdered cores, such as Kool-Mu, can
also work well.
Efficiency = P
OUT
/ P
IN
x 100%
= P
OUT
/ (P
OUT
+ P
TOTAL
) x 100%
P
TOTAL
= P(I
2
R) + P(tran) + P(gate) + P(diode) +
P(cap) + P(IC)
P = (I
2
R) = I
LOAD
2
x (R
DC
+ R
DS(ON)
+R
SENSE
)
where R
DC
is the DC resistance of the coil, R
DS(ON)
is
the MOSFET on-resistance, and R
SENSE
is the current-
sense resistor value. The R
DS(ON)
term assumes iden-
tical MOSFETs for the high-side and low-side switches
because they time-share the inductor current. If the
MOSFETs are not identical, their losses can be estimat-
ed by averaging the losses according to duty factor.
PD(tran) = transition loss = V
IN
x I
LOAD
x
ƒ
x
[(V
IN
C
RSS
/ I
GATE
) + 20ns]
where C
RSS
is the reverse transfer capacitance of the
high-side MOSFET (a data sheet parameter), I
GATE
is
the DH gate-driver peak output current (1.5A typ), and
the rise/fall time of the DH driver is typically 20ns.
MAX1637
Miniature, Low-Voltage,
Precision Step-Down Controller
______________________________________________________________________________________
17
Table 5. Low-Voltage Troubleshooting Guide
Low V
IN
-V
OUT
differential,
under 1V
Low V
IN
-V
OUT
differential,
under 1.5V
Dropout voltage is
too high
Sag or droop in V
OUT
under step-load change
SYMPTOM
Maximum duty-cycle limits
exceeded
Limited inductor-current
slew rate per cycle
ROOT CAUSE
CONDITION
Reduce operation to 200kHz.
Reduce MOSFET on-resistance
and coil DC resistance.
Increase bulk output capacitance
per formula (see
Low-Voltage
Operation
section). Reduce
inductor value.
SOLUTION