Fault management and reporting – Rainbow Electronics MAX34441 User Manual
Page 21
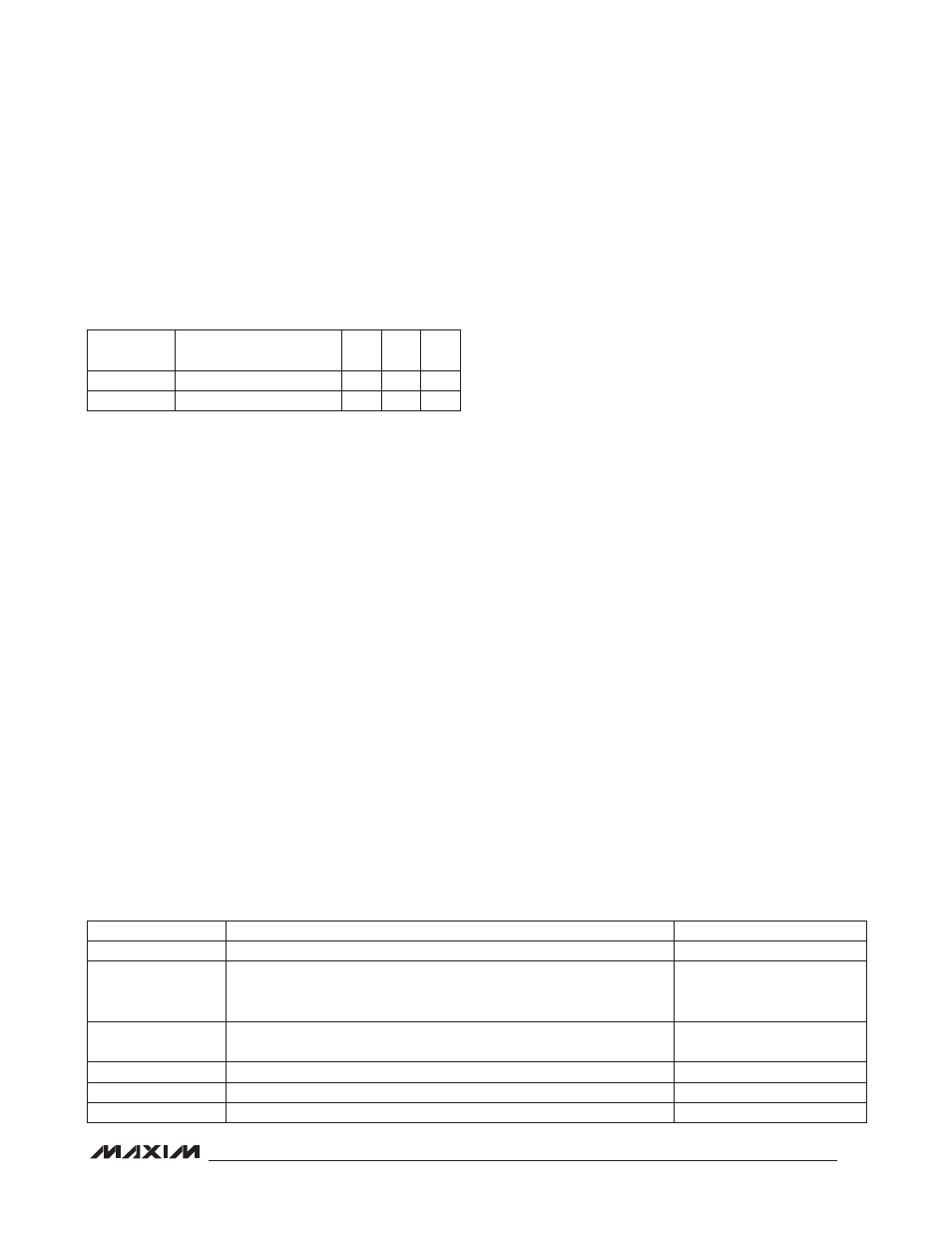
PMBus 5-Channel Power-Supply Manager
and Intelligent Fan Controller
MAX34441
21
The following example demonstrates how the host can
send and retrieve values from the device. Table 4 shows
the coefficients used in the following parameters.
If a host wants to set the device to change the power-
supply output voltage to 3.465V (or 3465mV), the cor-
responding VOUT_MARGIN_HIGH value is:
Y = (1 x 3465 + 0) x 10
0
= 3465 (decimal) = 0D89h (hex)
Conversely, if the host received a value of 0D89h on a
READ_VOUT command, this is equivalent to:
X = (1/1) x (0D89h x 10
-(-0)
- 0) = 3465mV = 3.465V
Power supplies and power converters generally have
no way of knowing how their outputs are connected to
ground. Within the power supply, all output voltages are
most commonly treated as positive. Accordingly, all out-
put voltages and output voltage-related parameters of
PMBus devices are commanded and reported as posi-
tive values. It is up to the system to know that a particular
output is negative if that is of interest to the system. All
output-voltage-related commands use 2 data bytes.
Fault Management and Reporting
For reporting faults/warnings to the host on a real-time
basis, the device asserts the open-drain ALERT pin (if
enabled in MFR_MODE) and sets the appropriate bit in
the various status registers. On recognition of the ALERT
assertion, the host or system manager is expected to poll
the I
2
C bus to determine the device asserting ALERT.
The host sends the SMBus ARA (0001 100). The device
ACKs the SMBus ARA, transmits its slave address, and
deasserts ALERT. The system controller then communi-
cates with PMBus commands to retrieve the fault/warn-
ing status information from the device.
See the individual command sections for more details.
Faults and warnings that are latched in the status regis-
ters are cleared when any one of the following conditions
occurs:
• A CLEAR_FAULTS command is received.
• The RST pin is toggled.
• Bias power to the device is removed and then reapplied.
One or more latched-off power supplies is only restarted
when one of the following occurs:
• The output is commanded through the CONTROL
pin, the OPERATION command, to turn off and then
turn back on.
• The RST pin is toggled.
• Bias power to the device is removed and then reapplied.
A power supply is not allowed to turn on if any faults the
supply responds to are detected. Only after the faults
clear is the power supply allowed to turn on. When global
supplies are being sequenced on, a fault on any of the
supplies keeps all supplies from being turned on.
A system-wide power-up (OPERATION command is
received to turn the supplies on when PAGE is 255 or the
CONTROL pin is toggled to turn on the supplies) allows
all enabled power supplies to power-up. If any faults are
detected once the supplies start to turn on, the response
of MFR_FAULT_RESPONSE is performed.
The device responds to fault conditions accord-
ing to the manufacturer fault response command
(MFR_FAULT_RESPONSE). This command byte
determines how the device should respond to each
Table 4. Coefficients for DIRECT Format
Value
Table 5. Device Parametric Monitoring States
COMMAND
CODE
COMMAND NAME
m
b
R
25h
VOUT_MARGIN_HIGH
1
0
0
8Bh
READ_VOUT
1
0
0
PARAMETER
REQUIRED CONDITIONS FOR ACTIVE MONITORING
ACTION DURING A FAULT
Overvoltage
Power Supply Enabled (TON_MAX_FAULT_LIMIT ≠ 0000h)
Continue Monitoring
Undervoltage
•
Power Supply Enabled (TON_MAX_FAULT_LIMIT ≠ 0000h)
•
PSEN Output is Active
•
Channel’s VOUT > POWER_GOOD_ON
Stop Monitoring While the
Power Supply is Off
Overcurrent
•
Power Supply Enabled (TON_MAX_FAULT_LIMIT ≠ 0000h)
•
Current Monitoring Enabled (IOUT_OC_FAULT_LIMIT ≠ 0000h)
Continue Monitoring
Power-Up Time
Power Supply Enabled (TON_MAX_FAULT_LIMIT ≠ 0000h)
Monitor Only During Power-On
Overtemperature
Temp Sensor Enabled (ENABLE in MFR_TEMP_SENSOR_CONFIG = 1)
Continue Monitoring
Fan Speed
Fan Enabled (Bit 7 in FAN_CONFIG_1_2 = 1)
Continue Monitoring