Electronics FC User Manual
Page 5
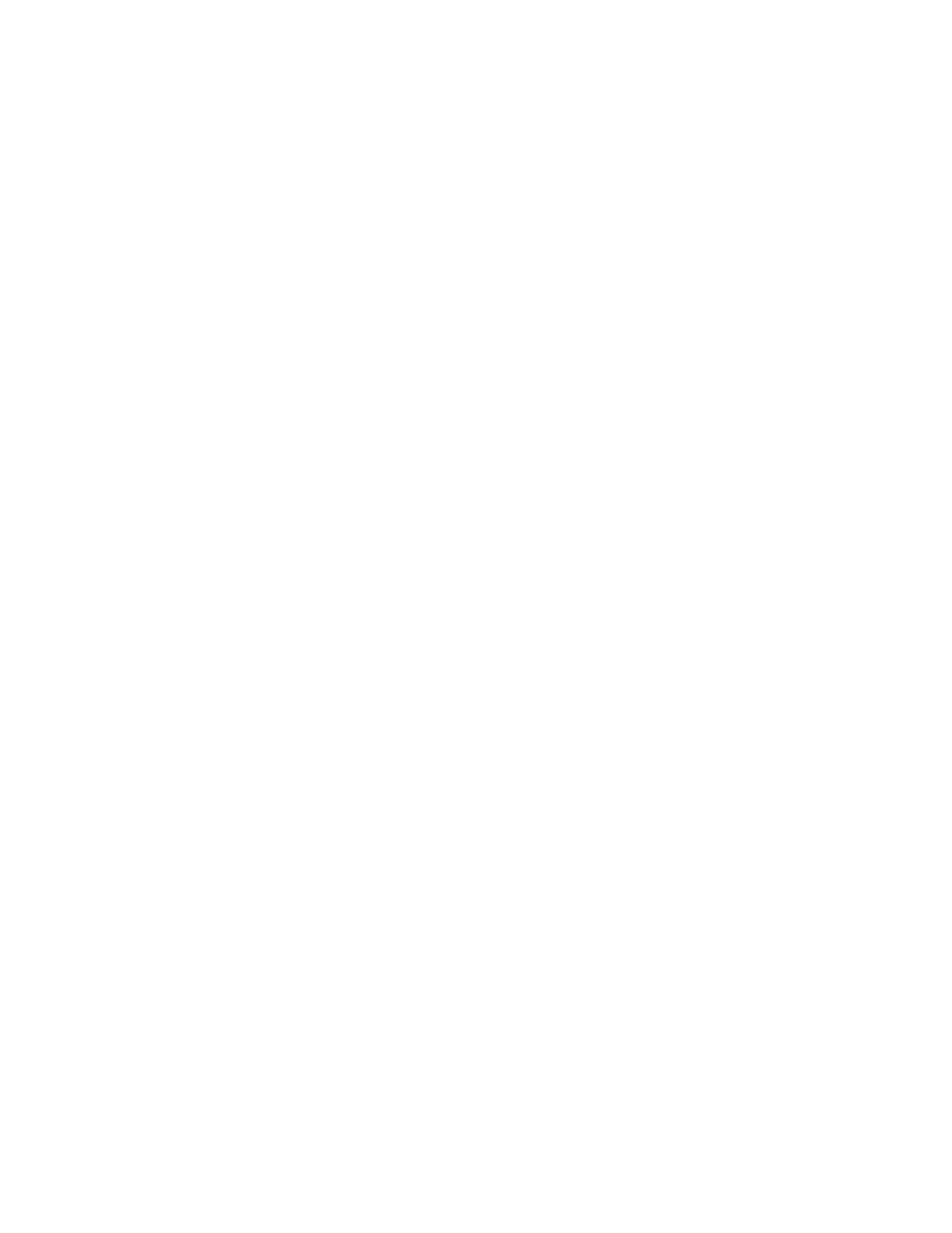
5
d. ALARM BAND - The flow set point is also the ± alarm mid-point. The alarm bandwidth, usu-
ally set at ± 5%, will track the flow set point. For example: with 1 pound/minute alarm band-
width and a set point of 12 pounds/minute the alarms would be active below 11 and above 13
pounds/minute. Changing the set point to 15 would change the alarms to 14 and 16 pounds/
minute automatically. The alarm bandwidth of ±1 stays fixed until the alarm bandwidth is
changed (see figure 2-7).
e. ALARM TIMER - When the control is "enabled" and in automatic servo mode, the "High" (1-
5) or "Low" (1-6) alarm light will come on if flow rate goes above or below the alarm limits. An
adjustable timer, labeled "ALARM DELAY” (2-6) which is adjustable from 0 - 10 seconds, will
start each time the "High" or (Low) lights come on. If the fault lasts longer than the timer set-
ting the “High” (or "Low”) lights will get brighter and the “High” (or “Low”) alarm relay contacts
will transfer and latch. The alarm will stay on after the “Enable” signal is removed until the
alarm is reset.
f. ALARM RESET - Activating the alarm-reset circuit (90-115VAC applied to Terminal #14) will
cancel the alarm relay and the alarm "High" or (“Low”) LED will go off. Continuous applica-
tion of the reset signal will disable or inhibit the alarm output signal. The alarms are automati-
cally reset upon receipt of each new "Enable" command.
g.
REMOTE SETPOINT - There are two conditions required for use of the remote setpoint. The
set point “Local/Remote” switch (2-12) must be down in the remote mode. A yellow LED (1-
8) on the front panel indicates operation in the remote mode. Apply a 0 - 10 Vdc analog re-
mote set point command signal to the remote input, Terminal #10. A 0Vdc signal will corre-
spond to a 0% flow rate command and 10 Vdc signal will correspond to a 100% flow rate. To
verify the set point command, push and hold the display switch (1-10) to the right. The re-
mote command may come from a remote pot or any 0 - 10Vdc signal source. An internal ref-
erence 10Vdc voltage for a (customer supplied) remote potentiometer (10k OHM) is available
at Terminal #4.
h. MODE SWITCH - The mode switch, (1-11) is used to turn the control "on" or "off" or to accept
a remote “Enable” while in the "Ready" mode.
i. RECORDER OUTPUT- An analog voltage recorder output signal Terminal #20 with a 0 -
10Vdc range is available to operate a strip-chart recorder or analog input card in data log-
gers. The minimum load on this output is 10K Ohms. Shielded cable (20AWG or larger
gage) should be used and the shield should be connected to rear chassis of the FC control.
This analog output signal is heavily filtered with a capacitor to provide noise immunity. Addi-
tional noise filtering may be necessary at the input terminals of your analog input card to pre-
vent erroneous readings.
j. MAGNAVALVE - During operation of the MagnaValve a red LED labeled Valve (1-3) will be
on, showing that power is sent to the MagnaValve. The MagnaValve also has an LED on the
valve driver junction box to show this function. This LED will pulse with the duty cycle (on
time to off time ratio). A low duty cycle will provide a low flow rate and the Valve LED will be
relatively dim. A long, or continuously on, duty cycle will provide for a high flow rate. At
100% duty cycle the Valve LED is constantly on and the permanent magnet field is com-
pletely canceled and no magnetic field exists in the MagnaValve and shot will fall freely
through the valve. The MagnaValve has no moving parts.
6. STABILITY ADJUSTMENTS - (SERVO STABILITY)
The servo adjustments have been factory set to typical settings and the customer may fine-tune to
optimize the speed of response if desired. Since there are many factors that determine system sta-
bility, these adjustments should be made slowly.