Electronics AC-24 User Manual
Page 8
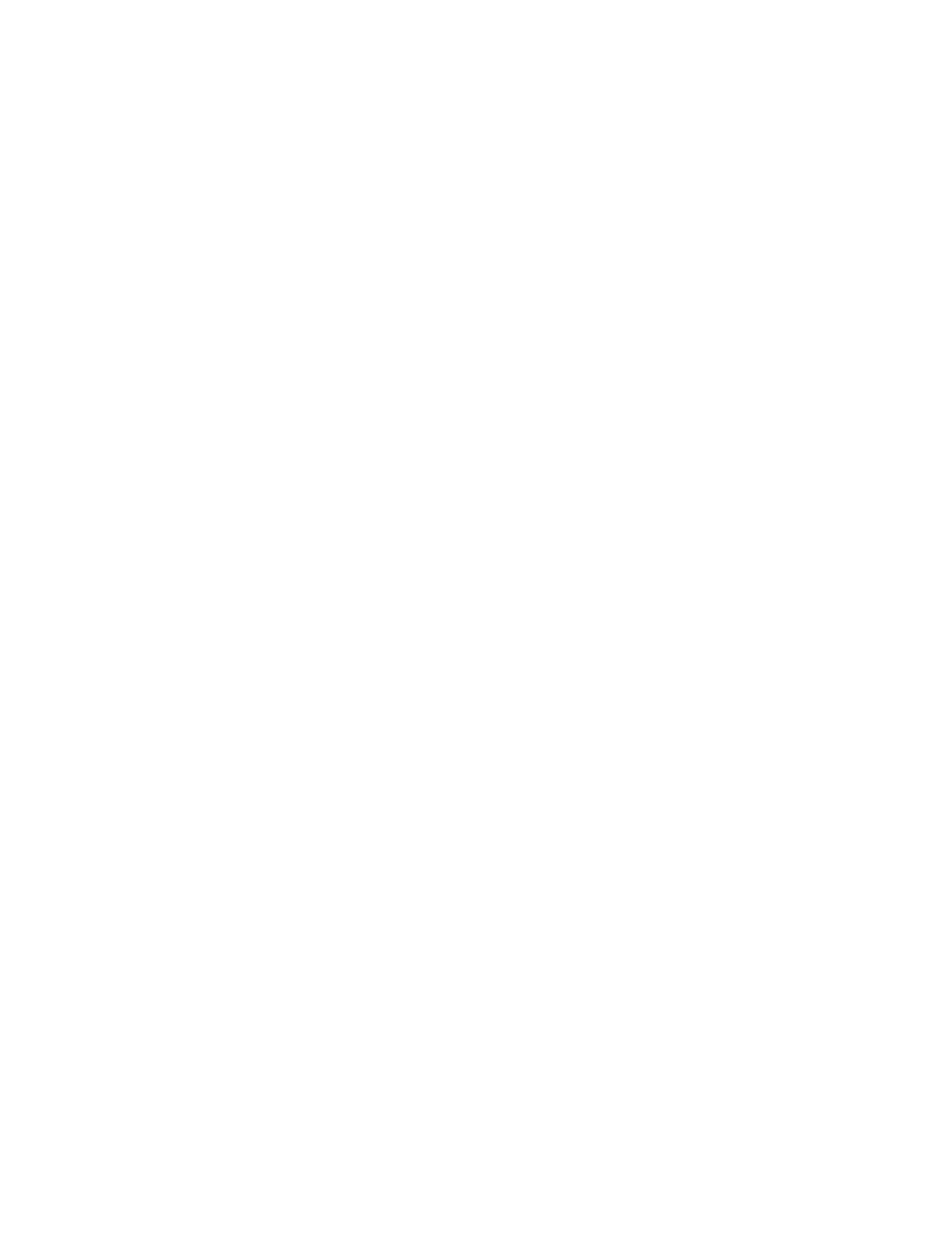
8
8. Adjust the setpoint command to 100%. The red LED bar graph will be fully on (all 10
elements on) and the MagnaValve will be in its maximum flow condition. Slowly open
the slide gate and observe the wheel ammeter for stability.
9. If the motor current is unstable, the problem is due to the wheel condition, not the AC
controller or MagnaValve.
10. If the machine uses a variable speed drive, check it for stability or bypass it with a con-
ventional motor starter.
11. The instability may be caused by flooding/choking the wheel or trying to flow more shot
than the capability of the wheel. Try operation at lower setpoint values.
12. Check for obstructions, restrictions or unnecessary bends in the flow path.
13. Worn blades or damaged control cages will not pass as much shot as new blades,
therefore as blades wear the maximum motor amperage is reduced.
14. Shot condition is very important. Unclean shot due to oil, water or dust, can cause er-
ratic flow performance. Dust can be generated by shot deterioration, or by abrasion of
parts being peened, erosion of the cabinet or tooling fixtures. Dust will tend to cake and
clog the flow. Under severe conditions, the MagnaValve may become completely
blocked.
B. Setpoint does not control motor amps
The following LEDs must be on:
1. “On” (1-7)
2. “Valve Output” bar graph (2-13)
3. “Servo On” (2-18)
4. “Local” (1-10) for control panel operation or “Remote” (1-9) for external setpoint signal.
5. MagnaValves operate using a magnetic field and have no moving parts. High air suc-
tion in some wheel designs may pull shot through the valve. This symptom is charac-
terized by having shot flowing when valve is red valve bargraph (2-13) is off. Providing
an aspiration air inlet below the MagnaValve may be necessary. Contact factory for as-
sistance.
6. MagnaValve be defective. Check the power and enable LEDs at the MagnaValve.
C. No alarm relay contact output.
1. Enable must be on (1 - 7).
2. Servo must be on (2-18).
3. High (1-2) or low (1-3) Alarm LED must be on (and in the bright mode) for alarm relay
contact to transfer. Check alarm bandwidth; it may be too large. Check setting of Alarm
Delay; it may be too long.
4. The Alarm Reset signal (24Vdc) should be absent from terminal #12.
D. Cannot achieve any flow, or motor amps is very low.
1. Enable On light must be on (1-7).
2. Setpoint command must be present (check setpoint by pushing Setpoint button (1-8).
Red LED bar graph “Valve Output” should have 2 or more elements lighted.
3. Check Red LED at MagnaValve. If it is not on, check for a wiring problem.
4. If the Red LED at the MagnaValve is on then check for an obstruction above the Mag-
naValve or low level of shot in the supply hopper. Check for contamination in or above
MagnaValve, especially check for water, oil, or dust mixture in the shot, or other ob-
structions.
5. The MagnaValve may be defective. To check, remove MagnaValve from machine
(keep wires attached). Enable the output and get red LED valve on at 100% duty cycle.
When the Valve LED is on, the magnetic field inside the MagnaValve should be per-
fectly canceled. No shot should stick inside the MagnaValve. If any shot sticks to the
valve, the MagnaValve is defective.