Electronics AC-24 User Manual
Page 5
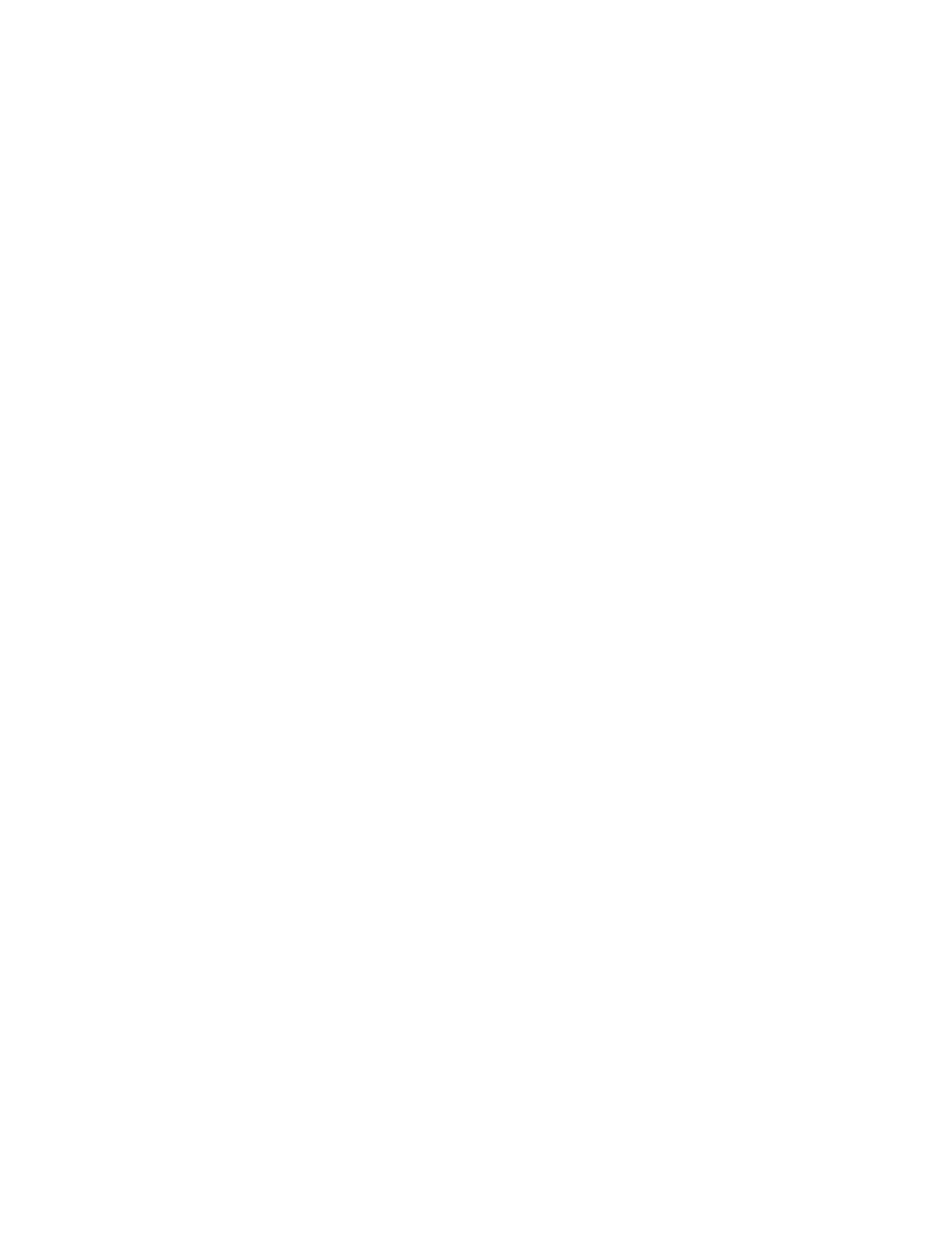
5
ting. For example: for an alarm band of 5 Amps and a setpoint of 30 Amps will have
alarms set at 25 and 35 amps. Moving the setpoint to 45 Amps will cause the alarms to
move to 40 and 50 Amps.
E. ALARM DELAY:
An adjustable time delay of 1-10 seconds is set by the alarm delay button (2-17) and the ▼
or ▲ buttons. The delay timer will start each time the “high” or “low” light comes on. If the
fault lasts longer than the timer setting, the high (or low) light will get brighter and the high
(or low) alarm relay contact will transfer and latch. The alarm will stay on after the “Enable”
signal is removed until the alarm is reset by application of the 24Vdc alarm reset signal or
the next reception of the enable signal.
F. ALARM RESET:
1. Application of the 24Vdc alarm reset signal at terminal 12 will cancel the alarm relay
and the alarm “high” or “low” LED’s will go off. Continuous application of the reset sig-
nal will disable or inhibit the alarm output signal.
2. The alarms are automatically reset upon receipt of each new “Enable” command and
therefore using the manual alarm reset function may not be necessary.
G. REMOTE MODE
1. A remote setpoint command may be used in place of the front panel setting. The set-
point LED (1-5) must be on. This is controlled by setpoint button (2-27)
2. Apply a 0 - 10 Vdc analog remote setpoint command signal to the remote input terminal
2. A 0 Volt dc signal will correspond to a 0% motor amps command; and 10 Vdc signal
will correspond to a 100% display range. To verify the setpoint command, push and
hold the setpoint switch. The remote command may come from a remote pot or any 0 -
10 Vdc signal source. An internal reference 10 Vdc excitation voltage for a remote po-
tentiometer (10K OHM) is available at terminal 2.
H. RECORDER OUTPUT
1. A recorder output analog voltage signal proportional to motor Amps is available at ter-
minal 18. It has a range of 0 - 10 Vdc and is provided to operate a strip-chart recorder
or analog input card in data loggers. The minimum load on this output is 10K Ohms.
Shielded cable should be used and the shield should be connected to the AC control-
ler’s chassis ground. Additional electrical noise filtering may be necessary at the input
terminals of your analog input card to prevent erroneous readings.
I. MAGNAVALVE OUTPUT SIGNAL
1. The MagnaValve uses permanent magnets and electromagnet solenoids to control the
flow of steel shot or grit, therefore it has no moving parts. During operation of the Mag-
naValve a red LED bar graph display (2-13) shows the relative magnitude of the servo
command signal sent to the MagnaValve.
2. The MagnaValve also has a LED to show this function. This LED will pulse at approxi-
mately an 8-15 Hertz rate with the duty cycle (on-time to off-time ratio) proportional to
shot flow rate and motor amps. A low-duty cycle will provide low shot flow rate and low
motor amps and the Valve LED will be relatively dim. A long, or continuously on, duty
cycle will provide for a high shot-flow rate and high motor amps. At 100% duty cycle the
Valve LED is constantly on, the permanent magnet field is completely canceled, and no
magnetic field exists in the MagnaValve therefore allowing shot to fall freely through the
valve.