4 profibus output signal – VEGA VEGAFLEX 54P (Profibus PA) User Manual
Page 6
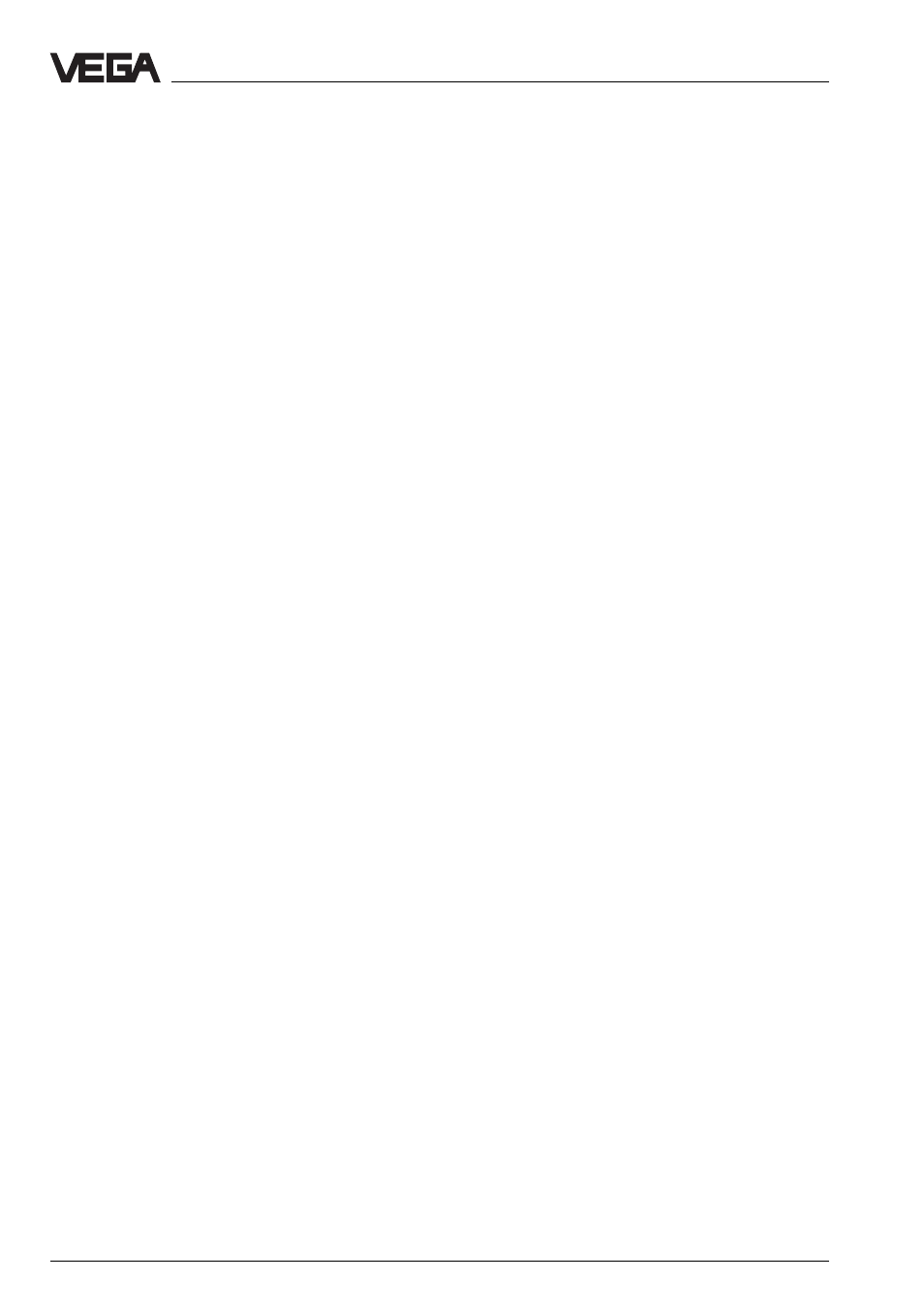
6
VEGAFLEX 54P (Profibus PA)
Product description
1.4 Profibus output signal
As a process automation bus, Profibus PA
enables power supply over the bus. Up to 32
sensors can be operated on a shielded two-
wire cable that carries both power supply
and measuring signal. In Ex areas, up to ten
sensors can be connected from the PA level
to one two-wire cable (EEx ia).
Bus structure
A Profibus system with DP and PA segments
consists of up to 126 Master and Slave par-
ticipants. Data are always exchanged from
point to point, with the data traffic being ex-
clusively controlled and checked by master
devices. Communication is carried out ac-
cording to the Token-Passing procedure.
This means that the master holding the Token
can contact the slaves, give instructions,
enquire data and cause the slaves to receive
and transmit data. After the work is done or
after a predetermined time interval, the Token
is passed on by the master to the next mas-
ter.
Master-Class 1
is the actual automation system, i.e. the proc-
ess control computer or the PLC that en-
quires and processes all measured values.
Master-Class 2
One or several Master-Class 2 devices can
operate in a Profibus network. As a rule,
Master-Class 2 devices are engineering,
adjustment or visualisation stations. The
VEGA adjustment software VVO (VEGA
Visual Operating) operates as Master-Class
2 participant on the DP bus and can work on
an engineering PC, on an adjustment PC or
on the process control computer and can
access any VEGA sensor on the PA level.
Profibus adjustment scheme
In the Profibus environment, there are differ-
ent adjustment concepts and adjustment
tools which often differ considerably from
manufacturer to manufacturer. From the us-
er’s point of view, a manufacturer-independ-
ent adjustment program which could be
operated directly on the Profibus DP, as well
as at any system node (e.g. the engineering
station or the process control), would be
ideal.
In the past, only the program "SIMATIC
PDM“, based on the HART
®
adjustment
scheme, could fulfil this wish (though with the
limitations common to HART
®
). As with
HART
®
, the availability of an instrument-spe-
cific database for a comprehensive adjust-
ment with PDM (Process Device Managing)
is a requirement. Otherwise, only the basic
instrument functions, such as adjustment, are
available. In the PDM environment, this instru-
ment-specific database is called EDD (Elec-
tronic Device Description), in perfect analogy
to the HART
®
environment which also re-
quires, except for the VEGA HART
®
instru-
ments, a DD (Device Description) for each
sensor.