Operating instructions – RIDGID 535 User Manual
Page 2
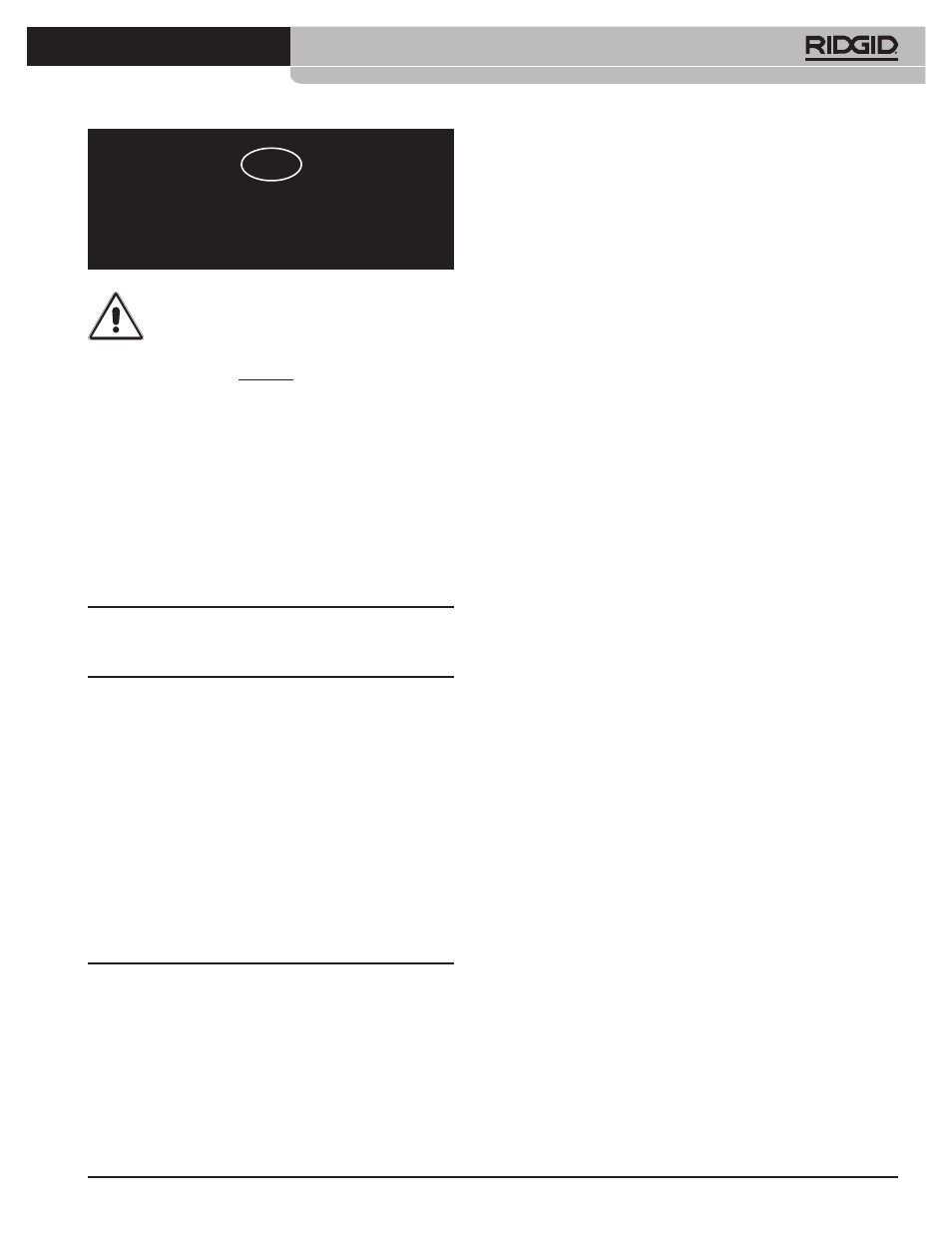
Ridge Tool Company
Tools For The Professional
TM
300 Compact, 1233, 300, 535
WARNING! Read these instructions
and the accompanying safety booklet
carefully before using this equipment. If
you are uncertain about any aspect of using this
tool, contact your RIDGID distributor for more
information.
Failure to understand and follow all instructions
may result in electric shock, fire, and/or serious
personal injury.
SAVE THESE INSTRUCTIONS!
SPECIFICATIONS
Threading Capacity
300
Compact
1233
300/300A
535
535 400V
Pipe
Bolt
1/8”-2”
3/8”-2”
1/8”-3”
3/8”-2”
1/8”-2”
1/4”-2” (M52)
1/8”-2”
1/4”-2” (M52)
Cut-off Capacity
Pipe
Bolt
Reaming
Noise level
Weight
Motor
1/8”-2”
3/8”-1”
1/4”-2”
79.5 dBA
52 kg
1.7 kW
1/8”-3”
3/8”-1”
1/4”-3”
80 dBA
56 kg
1.7 kW
1/8”-2”
1/4”-1”
1/4”-2”
80 dBA
48/90 kg
1.5 kW
1/8”-2”
1/4”-1”
1/4”-2”
80 dBA
110 kg
1.5 kW
Available in either 230 V or 110 V - 50/60 Hz (535: 400 V)
Required fuses 10 A (230 V), 20 A (115 V)
* 535 400V only
Weight: 170 kg
Motor: 400 V, 3Ø, 50 Hz, 1.35/1.7 kW, 35/70 min
-1
Standard Equipment
300
Compact
1233
300/300A
535
535 400V
811A diehead
812A diehead
815A diehead
1/2”-3/4”, 1”-2” BSPT
dies
928 receding diehead
2 1/2”-3” BSPT HS dies
Mineral thread cutting oil
-
-
x
x
-
-
5L.
-
-
x
x
x
x
5L.
x
-
-
x
-
-
5L.
x*
-
x*
x
-
-
5L.
*Optional
Accessories
300 Compact, 1233:
100 leg stand with tray
200 wheel and cabinet stand
250 folding stand
419 nipple chuck 2 1/2” or 3” (8.2/19 cm min/max. nipple length)
819 nipple chuck 1/2”-2”
300, 300A, 535: See RIDGID Catalogue
Transport and Handling
Note: Two people are required to lift machines. Lift the machine using the hand
holds provided. The machine may be bench mounted or attached to one of the
RIDGID stands as illustrated (see page 2). Alternatively, four equal lengths of
pipe can be fitted into the sockets provided (300 Compact, 1233 only).
Machine Set-Up
Read safety information leaflet before using the machine. If you are uncertain
about any aspect of using this equipment contact your RIDGID Distributor. This
machine is designed for threading pipe and bolt and, with optional RIDGID
accessories, threading and grooving of pipe. We strongly recommend that it
NOT be modified and/or used for any application other than for which it was
intended including making-up or breaking apart of fittings, applying hemp or
powering other equipment. Place machine away from doors or passageways
and ensure that the total work area can be viewed from the operating position.
Use barriers to keep people away from the rotating pipe. Do not use machine in
wet or humid conditions. Check that machine voltage is the same as the power
supply. Ensure footswitch operates correctly and switch is in “O” position before
connecting to power supply. Use the correct plug with an earth connection and
ensure that the socket is in an accessible position located between 0.6 and
1.9 m from the ground. The footswitch allows full control of the machine which
will only operate when the pedal is depressed. For your safety ensure that
the footswitch operates freely and position it so that all controls can be easily
reached. Use a pipe support if the pipe extends more than 1 m from the rear
chuck. Add pipe supports for longer lengths (see Fig. 1).
Operation
RIDGID threading machines have been designed for ease of use (see Fig. 2).
For explanation of switch positions see Fig. 13.
IMPORTANT: Release foot from footswitch and allow machine chuck to come
to rest before touching chuck handwheel, pipe or dies. Ensure switch is in “0”
position before making any adjustments.
• Chuck (A): Close chuck by turning handwheel in a counter clockwise
direction. Check pipe is centered and tighten jaws with a repeated spin of
the handwheel. The RIDGID model 535A is equipped with an automatic
chuck. Place the pipe in the chuck, switch to Forward direction and press
on the footswitch. The pipe will be gripped and centered. If the pipe is
not centered switch to reverse to release the pipe and again switch to
Forward.
Keep hands away from chuck jaws when machine is connected to a
power supply. Closing jaws can crush fingers.
• Cutter (B): Set the cutter wheel at the point to be cut and feed the wheel
into the pipe by rotating the handle clockwise (Fig. 3) whilst rotating the
pipe.
• Reamer (C): Ream the pipe by applying pressure to handwheel (Fig. 4).
• Diehead (D): Install correct dies. Set diehead (see Fig. 5). With pipe
rotating, feed carriage to bring dies into contact with the pipe. Continue to
apply pressure to the handwheel until the dies are engaged.
The diehead will open automatically at the end of the thread.
GB
300 Compact, 1233, 300, 535
Operating Instructions