York YR User Manual
Page 39
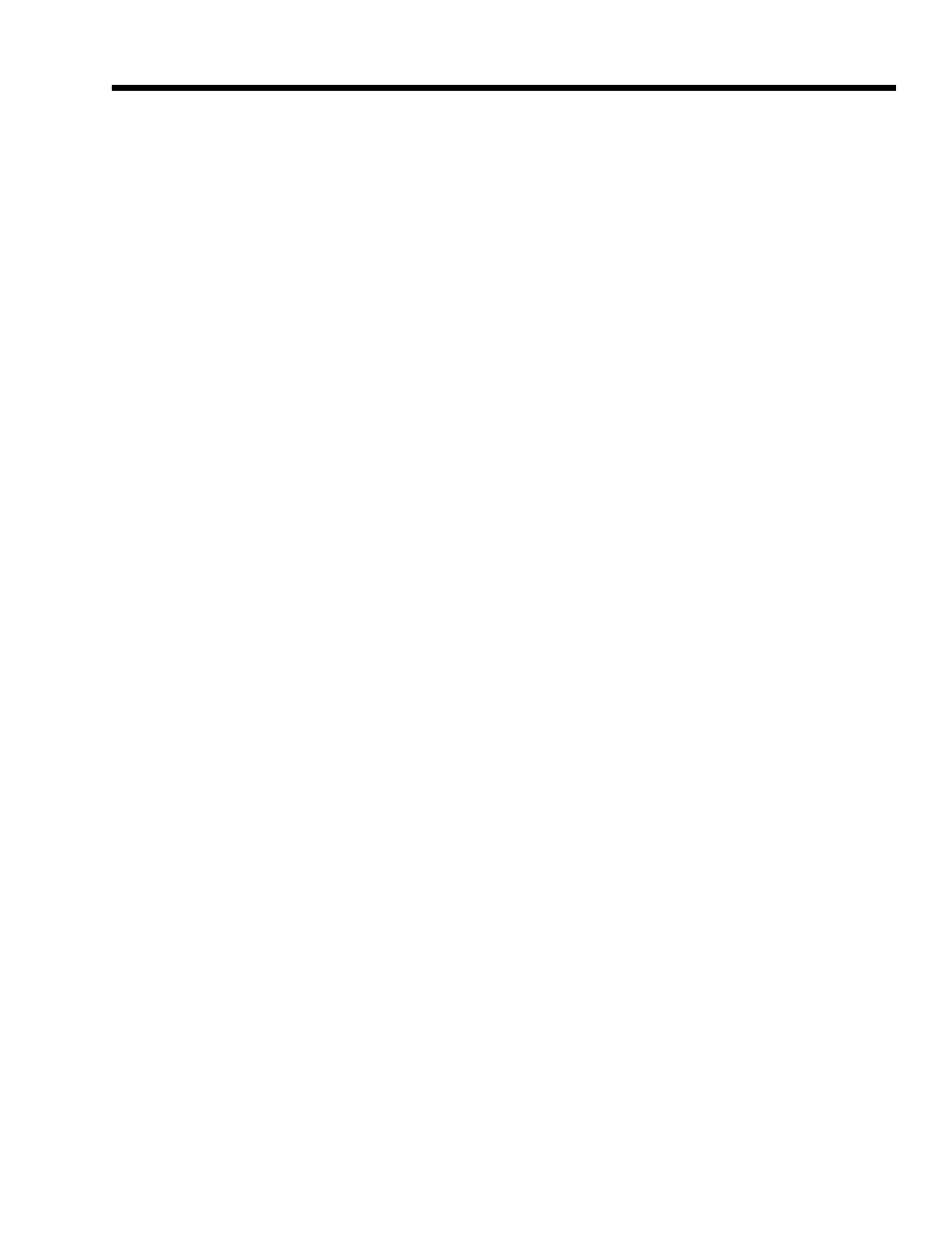
39
YORK INTERNATIONAL
FORM 160.81-EG1
n. Oil - high pressure
o. Control panel - power failure
p. Watchdog - software reboot
5.1. Safety shutdowns with a Solid State Starter
(LCSSS) shall include:
a. Shutdown - requesting fault data...
b. High instantaneous current
c. High phase (X) heatsink temperature - running
d. 105% motor current overload
e. Motor or starter - current imbalance
f. Phase (X) shorted SCR
g. Open SCR
h. Phase rotation
6. Cycling shutdowns enunciated through the display
and the status bar, and consisting of system sta-
tus, system details, day, time, cause of shutdown,
and type of restart required.
Cycling shutdowns shall include:
a. Multiunit cycling - contacts open
b. System cycling - contacts open
c. Control panel - power failure
d. Leaving chilled liquid - low temperature
e. Leaving chilled liquid - flow switch open
f. Condenser - flow switch open
g. Motor controller - contacts open
h. Motor controller - loss of current
i. Power fault
j. Control panel - schedule
6.1 Cycling shutdowns with a Solid State Starter
(LCSSS) shall include:
a. Initialization failed
b. Serial communications
c. Requesting fault data
d. Stop contacts open
e. Power fault
f. Low phase (X) temperature sensor
g. Run signal
h. Invalid current scale selection
i. Phase locked loop
j. Low supply line voltage
k. High supply line voltage
l. Logic board processor
m.Logic board power supply
n. Phase loss
7. Security access to prevent unauthorized change
of setpoints, to allow local or remote control of
the chiller, and to allow manual operation of the
variable orifice and slide valve position. Access
shall be through ID and password recognition,
which is defined by three different levels of user
competence: view, operator, and service.
8. Trending data with the ability to customize points
of once every second to once every hour. The panel
shall trend up to 6 different parameters from a list
of over 140, without the need of an external moni-
toring system.
9. The operating program stored in non-volatile
memory (EPROM) to eliminate reprogramming the
chiller due to AC power failure or battery discharge.
Programmed setpoints shall be retained in lithium
battery-backed RTC memory for a minimum of 11
years with power removed from the system.
10. A fused connection through a transformer in the
compressor motor starter to provide individual
over-current protected power for all controls.
11. A numbered terminal strip for all required field in-
terlock wiring.
12. An RS-232 port to output all system operating data,
shutdown/cycling message, and a record of the last
10 cycling or safety shutdowns to a field-supplied
printer. Data logs to a printer at a set program-
mable interval. This data can be preprogrammed
to print from 1 minute to 1 day.
13. The capability to interface with a building automa-
tion system to provide:
a. Remote chiller start and stop
b. Remote leaving chiller liquid temperature adjust
c. Remote current limit setpoint adjust
d. Remote ready to start contacts
e. Safety shutdown contacts
f. Cycling shutdown contacts
g. Run contacts
COMPRESSOR MOTOR STARTER
(OPTION, 200 - 600V)
The chiller manufacturer shall furnish a reduced-volt-
age Solid State Starter for the compressor motor. Starter
shall be factory-mounted and wired on the chiller. The
starter shall provide, through the use of silicon controlled
rectifiers, a smooth acceleration of the motor without
current transitions or transients. The starter enclosure
shall be NEMA 1, with a hinged access door with lock
and key. Electrical lugs for incoming power wiring shall
be provided.