5 start up procedure, 1 installation with in-line cleaning systems – Viking SLAL User Manual
Page 7
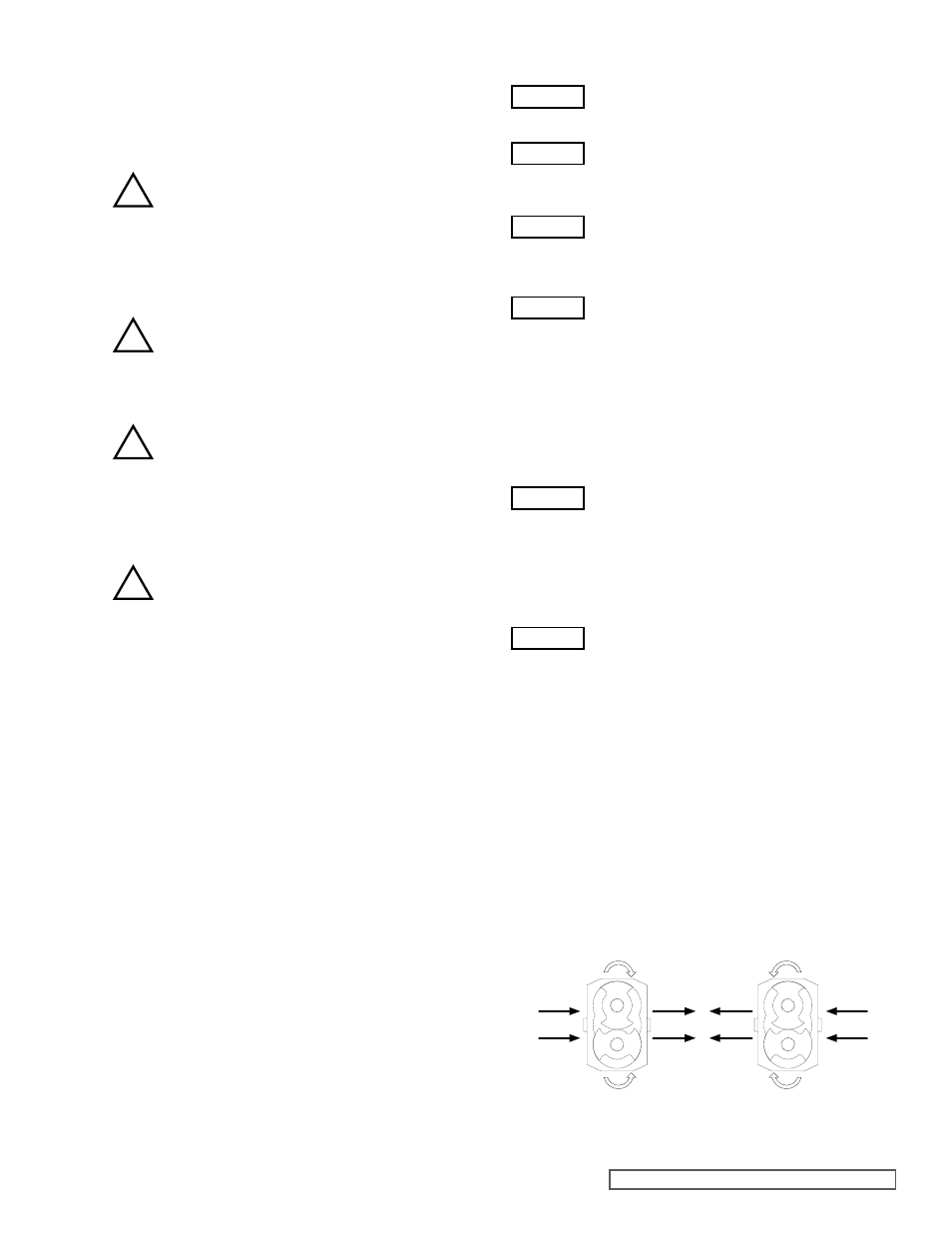
fIGURE 9
ROTaTION
dIsCHaRGE
sUCTION
sUCTION
ROTaTION
SECTION TSM 288
ISSUE
A
PAGE 7 OF 36
3.5 sTaRT UP PROCEdURE
• Check that all piping and associated equipment
are clean and free from debris and that all pipe
connections are secure and leak free.
• For pumps installed with flushed product seals
check that all auxiliary services are in place
and connected and provide sufficient flow and
pressure for flushing purposes
• Ensure lubrication is provided for both pump
and drive. SL Series pumps are shipped pre-
filled with grease, refer to section 6.4 grease
capacities and grades.
• If an external relief valve is incorporated in the
system check that it is set correctly. For start
up purposes it is considered good practice
to set the relief valve lower than the system
design pressure. On completion of start up the
relief valve should be set for the application.
The required setting should never exceed the
lower of either the pumps maximum pressure
rating or the system design pressure. For
setting integral relief valves, refer to sections
3.8.1 and 3.8.2.
• Ensure both suction and discharge valves
are fully open, and pipe work is free from
all obstructions. SL Series pumps are of
the positive displacement type and should
therefore never be operated against a closed
valve as this would result in pressure overload,
resulting in damage to the pump and possibly
the system.
• Ensure rotation of the drive shaft is correct for
the direction of flow required see Figure 9.
• Ensure product is available in the tank before
starting pump. This is very important for pumps
installed with un-flushed product seals, as
these sealing arrangements must never be
allowed to run dry.
• Before beginning operation it is considered
good practice to momentarily start/stop the
pump to check the direction of rotation and
ensure that the pump is free of obstructions.
Once this has been carried out, begin
operation keeping a visual check on suction
and discharge pressure gauges and monitor
pump temperature and power absorbed where
possible.
Where motor mounted options are to be installed follow the
manufactures recommended guidelines. However, when
installing a pump complete with base and drive, the following
guidelines must be observed:
• The preferred drive arrangement for any rotary
lobe pump is in-line direct coupled.
• Flexible couplings must always be incorporated
and correctly aligned within the limits
recommended by the coupling manufacturer.
To check coupling alignment rotate the shaft
by at least one full revolution and ensure that
the shaft rotates smoothly.
Couplings of a non-flexible design must never
be used.
• Couplings must always be enclosed in a suitable
guard to prevent contact with rotating parts that
could result in personal injury. Guards should
be of suitable material, and of sufficiently rigid
design to prevent contact with rotating parts
under normal operating conditions.
• When installing pump sets in flammable
or explosive environments, or for handling
flammable or explosive materials, special
consideration must be given not only to the
safety aspects of the drive unit enclosure
but also to the materials used for both the
coupling and the guard to eliminate the risk of
explosion.
• Baseplates must be secured to a flat level
surface such that distortion and misalignment
are avoided.
Once baseplates are fastened
in position the drive alignment must be re-
checked.
• When using electric motor drives, ensure
that the electrical supply is compatible with
the drive and controls and that the method of
wiring is correct for the type of starting required
by the motor i.e. Direct On Line, or other similar
method. Ensure all components are correctly
grounded.
3.4.1 INsTallaTION WITH IN-lINE
ClEaNING sYsTEMs
The SL Series range has been designed to be effectively
cleaned by procedures recommended for in-line cleaning of
process plant. To assist in maximizing the effectiveness of
cleaning within the pump head it is recommended that during
the cleaning cycle a flow rate equivalent to a velocity of 1.5
metres per second (3.3 feet per second); in a pipe of equal
diameter to the rotor case connections is achieved. With a
differential pressure of 2 to 3 bar (30 to 45 psi) being developed
across the pump head
For applications where maximum drainage of the pump head is
required, and / or where in-line cleaning is employed, the pump
ideally should be mounted with the rotor case connections in
the vertical orientation. A procedure must be determined to
ensure that the pump is effectively cleaned. It is recommended
that this cycle would typically include a combination of some
or all of the following: Acidic or Caustic based Detergents,
‘Sanitizers’, Disinfectants and Water rinses. These must
be appropriate to both the products being handled and the
materials of construction of the pump.
WaRNING
WaRNING
WaRNING
WaRNING
WaRNING
WaRNING
!
!
!
!