Festo Кабели и принадлежности User Manual
Page 103
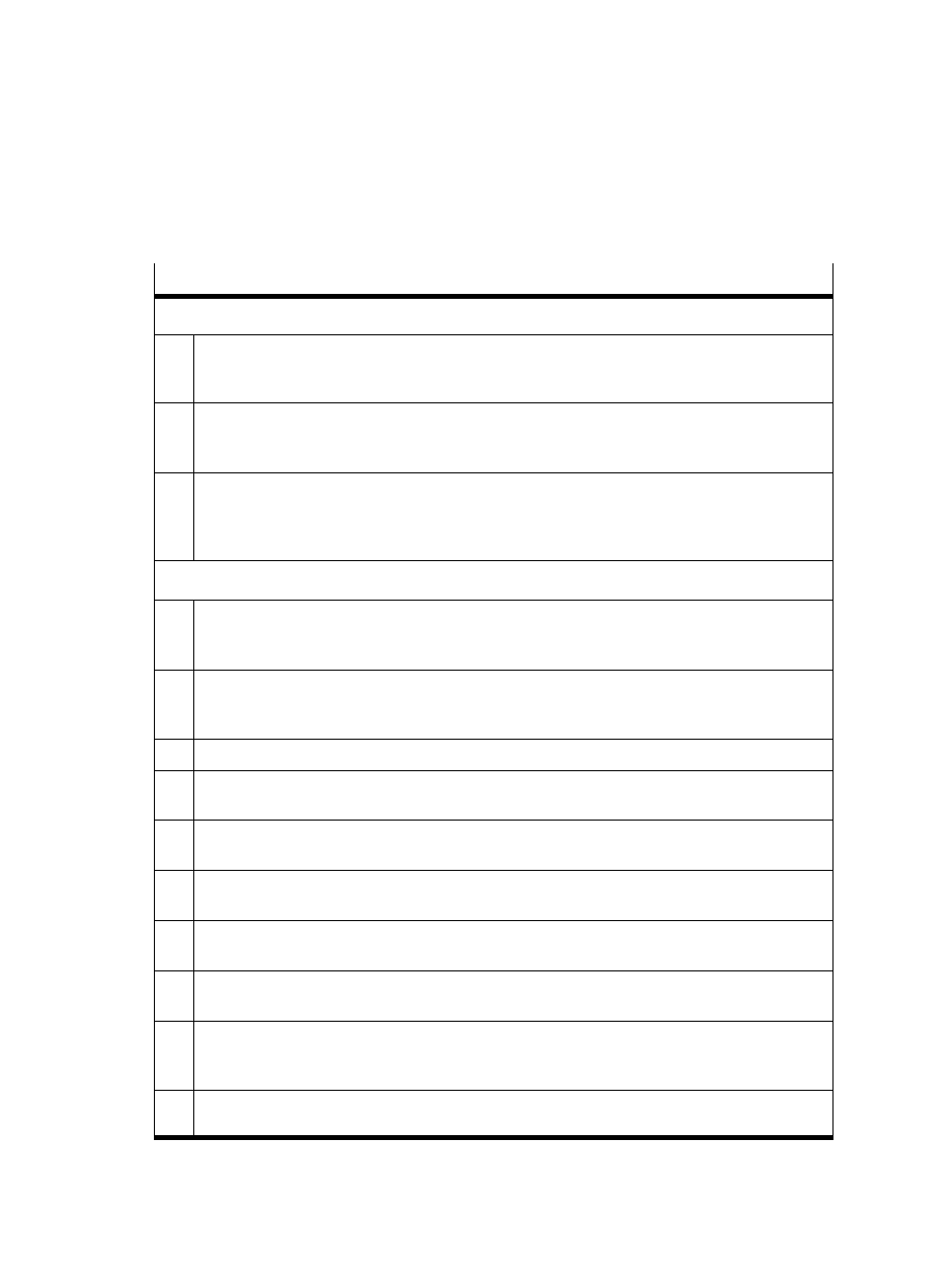
3. Installation
3−25
Festo P.BE−SPC200−EN en 0901d
Dimensional reference system for drive type DSMI−...
Reference points
(1)
Measuring system zero point ć always on the behind the stop on the left−hand side of the drive
in the anti−clockwise direction; corresponds to a measured value of 0". In the DSMI it cannot
be reached due to the limitation of the rotary wing, see also [L].
(2)
Axis zero point ć this is always to the left in the anti−clockwise direction, and corresponds to
the extreme position of the stop lever. All other axis−specific reference values refer to this
point.
(3)
Project zero point ć reference point for all angle values in programs and the position registers;
defined by the user. An actual position which is displayed also refers to this point. With this
reference value, the user has the option of using software to compare the location of the angle
values to a fixed point on the machine.
Definition of paths
(A)
Mounting offset ć specifies the angle offset between the measuring system zero point and the
axis zero point. It is a signed value; the arrow direction indicated corresponds to a positive
angle of rotation. WinPISA automatically provides this value in the application data.
(B)
Project zero point offset ć specifies the angle offset between the axis zero point and the
project zero point. It is a signed value; the arrow direction indicated corresponds to a positive
angle of rotation.
(C)
Value of the current angle position (
j actual position) relative to the project zero point.
(D)
Value of the lower software end position; defines the smallest angle of rotation that can be
moved to.
(E)
Value of the upper software end position; defines the largest angle of rotation that can be
moved to.
(F)
Working stroke ć specifies the angle range of the rotary drive; it is determined by the software
end positions and specified by the user. The following applies: (F) = (E) ć (D)
(G)
Maximum permissible angle range during positioning; determined by the max. swivel angle of
the drive (for DSMI: 272°) and the stroke reserve. The following applies: (G) = (H) ć 2 * [K]
(H)
Angle of rotation of the drive, corresponds to the order specifications, and is also indicated on
the type plate.
[K]
Stroke reserve; for the DSMI it is 5°. It decreases the usable angle of rotation of the rotary
drive. In this angle range, close to the inner end stops, positioning behaviour is affected
excessively by the damping elements.
[L]
Electric reserve of the measuring system. This is used to monitor the electrical connection.
In the DSMI, this reserve is already built in, and does not have to be considered by the user.