Electronic lineshaft with alignment, 4 alignment operation description – Yaskawa G5 Electronic Lineshaft Alignment User Manual
Page 5
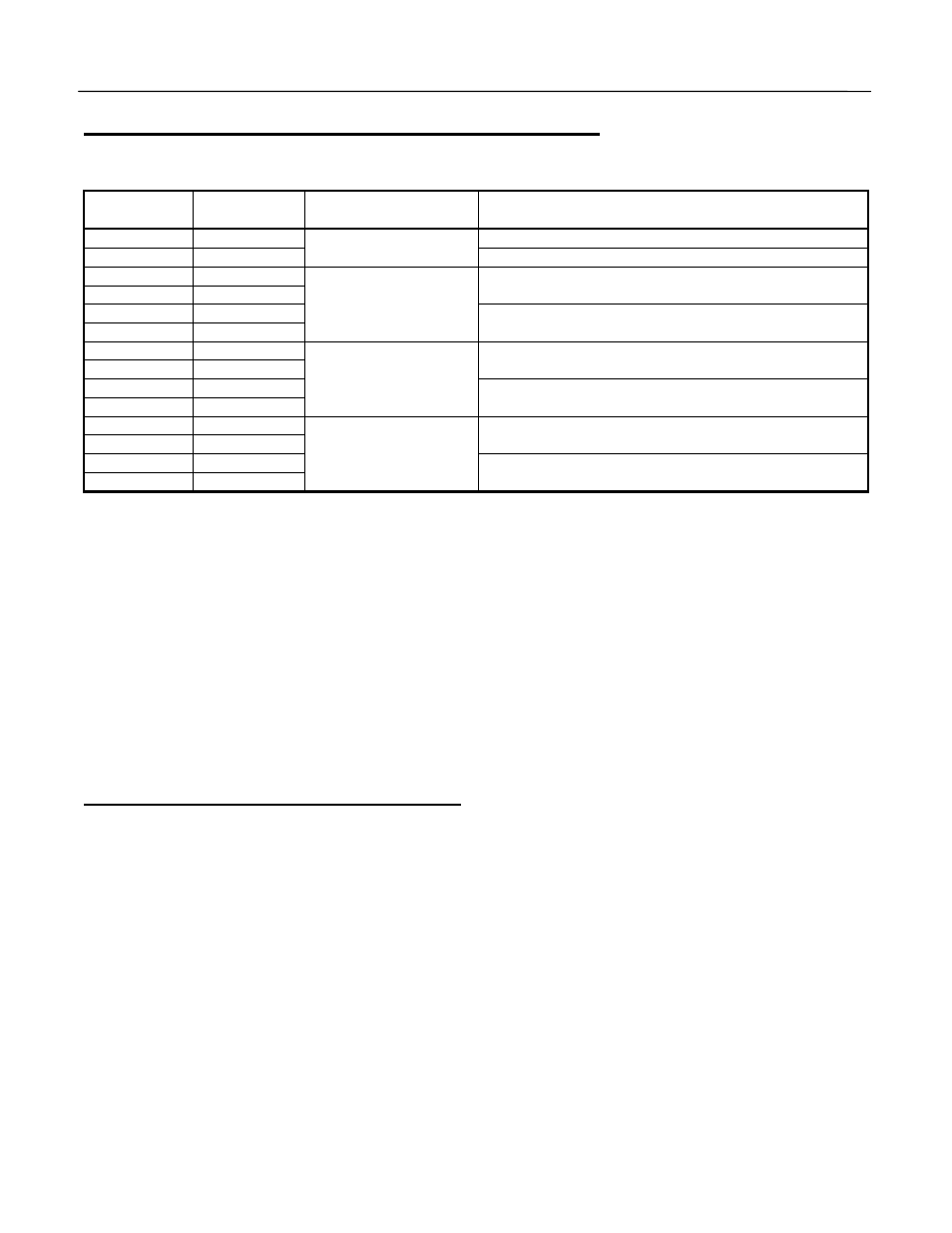
Electronic Lineshaft with Alignment
Date: 07-01-04, Rev: 04-07
Page 5 of 15
TM.G5SW.046
1.3 PG-W2 Terminal Description and Wiring Notes
Refer to the GPD515/G5 User’s Manual for additional information regarding encoder feedback option cards.
PG-W2
Terminal #
Designation Function Remarks
1
IP12
+12V supply to power encoder
2 IG12
Power Supply
0V, Common for 12V power supply
3 +A
4 -A
Channel 1, Pulse Input A
5 +B
6 -B
Follower Motor
Feedback
Channel 1, Pulse Input B
10 +A
11 -A
Channel 2, Pulse Input A
12 +B
13 -B
Master
Device
Signal
Channel 2, Pulse Input B
17 +A
18 -A
Encoder 2, Pulse Output, Channel A (5V pk)
19 +B
20 -B
Pulse Output
(Mirrors Channel 2)
Encoder 2, Pulse Output, Channel B (5V pk)
For proper lineshaft operation the following conditions must be met:
1) A PG-W2 encoder feedback card must be installed in the follower VFD(s).
2) The pulse reference from the master device must be quadrature, differential line driver type.
3) Encoder feedback from the follower motor must be quadrature, differential line driver type.
4) When the master operates in its normal, forward direction, monitor U1-50 of the follower should display a
positive value. If it does not, it may be necessary to reverse the channel 2 pulse input A wires at
terminals 10 and 11 of the follower’s PG-W2.
5) If the follower’s U1-50 display is positive, when the drive is commanded to run via input to terminal #1, the
motor should rotate in the proper direction and the follower’s U1-05 monitor should display a positive value. If
the motor direction is incorrect, it may be necessary to reverse any two of the motor leads on the VFD output.
If the motor fails to rotate, or is unstable, it may be necessary to reverse the channel 1 pulse input A wires at
terminals 3 and 4 of the PG-W2.
6) Do not use parameter F1-05 to change encoder phasing in this software. Please swap encoder
signals A+ and A- instead.
1.4 Alignment Operation Description
The alignment operation performed by the follower drive requires three external inputs. The “Align Slave” input
enables and disables the alignment feature. The “Master Trigger” input indicates the master drive is at the
aligned position. The “Slave Trigger” input indicates that the slave drive is at the aligned position. The aligned
position is where both trigger switches are activated at the same time.
When the “Align Slave” input is activated the slave drive will monitor the trigger inputs. The slave drive will
accumulate the error count that separates the leading edges of the trigger inputs. When aligned both triggers are
simultaneous. When not aligned the leading trigger will start an error count. The following trigger will stop the
error count and the error will be corrected by advancing or retarding the slave drive at a maximum frequency of 4
Hz. The correction will occur when the leading edge of the following trigger is activated.
The recommended speed range for alignment is between 6 to 12Hz. Alignment can be performed at higher
speeds. The trigger inputs require a minimum signal of 5 milliseconds. If the alignment speed is below 4 Hz the
slave drive may run in the reverse direction to retard.
Parameter P1-02: “Align Offset” has been provided to adjust for misalignment of the trigger switches. The
adjustment allows for + / - 9999 quadrature encoder counts or approximately 2.5 motor revolutions when using a