Understand and optimize cut quality, Understand and optimize cut quality -13, Powermax – Hypertherm Powermax45 Service Manual User Manual
Page 73
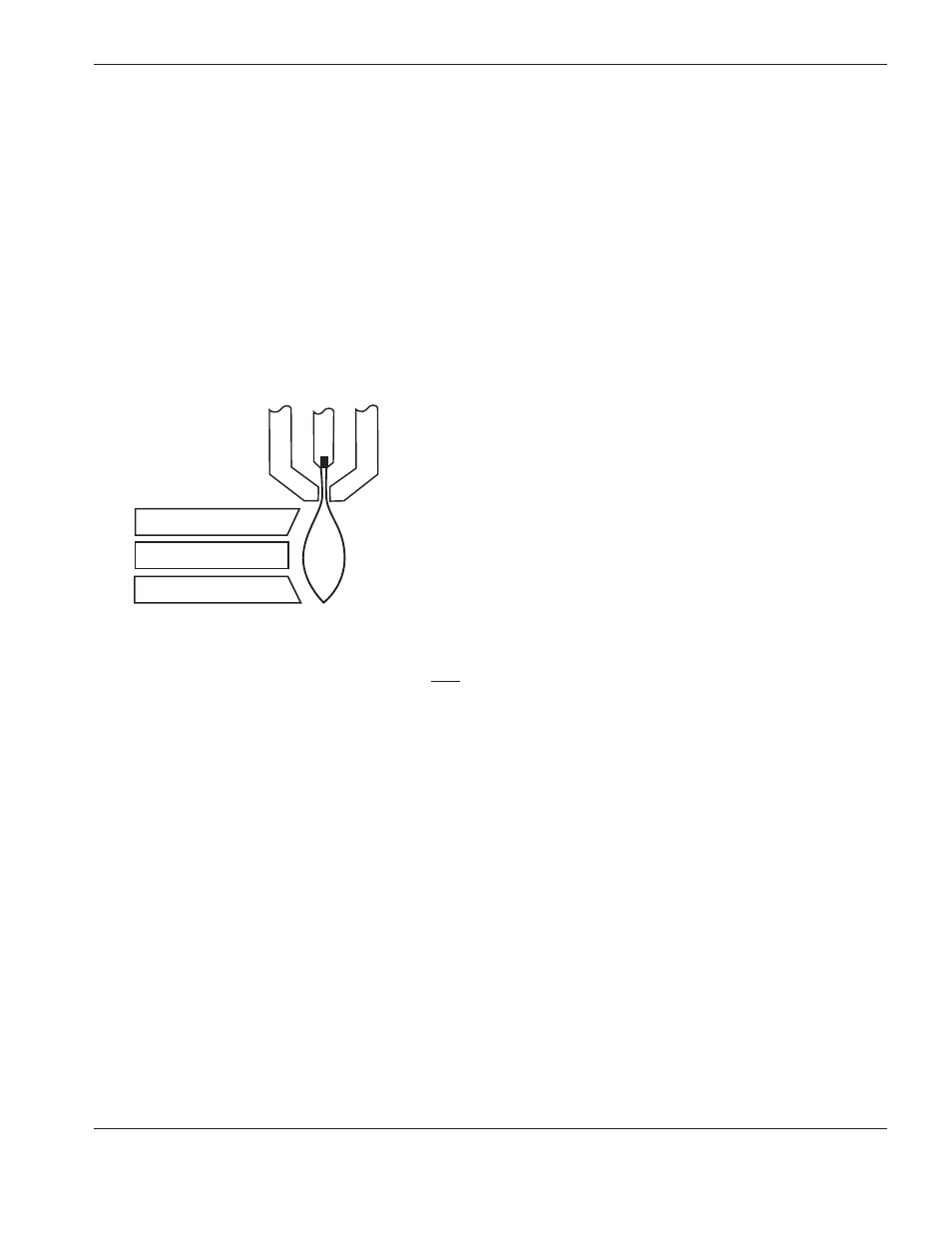
operation
powermax
45
Service Manual
4-13
Understand and optimize cut quality
There are several factors to consider in cut quality:
• Cut angle – The degree of angularity of the cut edge.
• Dross – The molten material that solidifies on the top or bottom of the workpiece.
• Straightness of the cut surface – The cut surface can be concave or convex.
The following sections explain how these factors can affect cut quality.
Cut or bevel angle
• A positive cut angle, or bevel, results when more material is removed from the top of the cut than from the bottom.
• A negative cut angle results when more material is removed from the bottom of the cut.
Notes: The squarest cut angle will be on the right side with respect to the forward motion of the torch. The left side
will always have some degree of bevel.
To determine whether a cut-angle problem is being caused by the plasma system or the drive system, make a test cut
and measure the angle of each side. Next, rotate the torch 90° in its holder and repeat the process. If the angles are the
same in both tests, the problem is in the drive system.
If a cut-angle problem persists after “mechanical causes” have been eliminated (see
Ensure the torch and table are set
), c
heck the t
orch-to-work distance, especially if the cut angles are all positive or all negative.
Also consider the material being cut. If the metal is magnetized or hardened, you are more likely to experience cut angle
problems.
dross
Some amount of dross will always be present when cutting with air plasma. However, you can minimize the amount and
type of dross by adjusting your system correctly for your application.
Dross appears on the top edge of both pieces of the plate when the torch is too low (or voltage is too high if using a
torch height control). Adjust the torch or the voltage in small increments (5 volts or less) until the dross is reduced.
Low-speed dross forms when the torch’s cutting speed is too slow and the arc shoots ahead. It forms as a heavy,
bubbly deposit at the bottom of the cut and can be removed easily. Increase the speed to reduce this type of dross.
Cause
The torch is too high.
Solution
Lower the torch; or if you are using a torch
height control, decrease the arc voltage.
Negative cut angle
Problem
The torch is too low.
Raise the torch; or if you are using a torch
height control, increase the arc voltage.
Square cut
Positive cut angle