Groth 3000 Series User Manual
Page 16
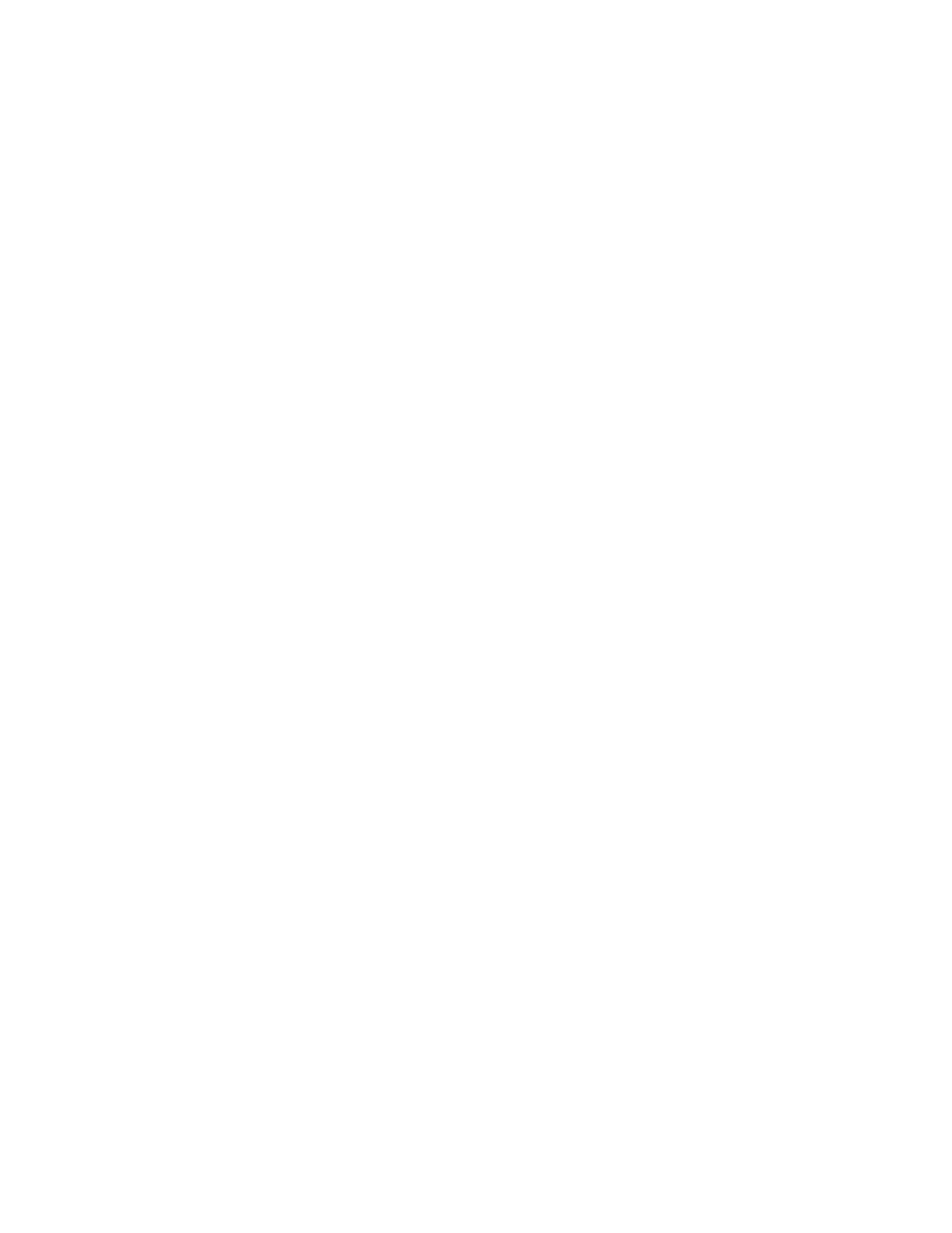
13
RECOMMENDED TESTING AND SETTING PROCEDURE
1.0) Equipment
1.1) A high pressure air (or inert gas) supply
system capable of maintaining supply pressure
at 0-200 PSI. Flow may be controlled by a
reducing regulator or valve.
1.2) A low pressure air (gas) supply system
capable of maintaining sense pressure at 1/2"
WC to 10 PSI. Pressure may be controlled by
a regulator or needle valve and a small
accumulator. If a needle valve is used, it will
require frequent adjustment because the
regulator consumes a significant volume of air
when operating.
1.3) A means of indicating or measuring air flow
with a capacity of approximately 30 SCFH.
1.4) A means of soap bubble shell testing the
assembly.
2.0) Test procedure and Acceptance Criteria.
2.1) Connect the high pressure air supply to the
regulator inlet port.
2.2) Connect the low pressure air supply to the
regulator sense port.
2.3) Connect a reduced size manual shut-off valve
to the outlet port.
2.4) Connect a small diameter hose or plastic tube
to the inlet of the flow indicator or flow meter.
Use a hand held port cover to attach the flow
meter to the regulator outlet port. Never
connect the flow meter rigidly to the regulator
unless the flow meter is rated for full air
supply pressure.
2.5) Connect a small diameter hose or plastic tube
to the outlet of the flow indicating device so
the end may be immersed in a container of
water.
2.6) Close the outlet valve and set the supply air
pressure to the maximum available, but not
greater than 300 PSI. Soap bubble test the
entire assembly at this pressure. Open the
outlet valve and reduce the supply until a
minimum audible flow is observed.
2.7) Adjust the sense pressure to the specified
regulator set pressure. Adjust the regulator
screw to shut off (no audible flow). Now
increase the sense pressure to 2 times the
specified set pressure or 1.5 times the
specified tank MAWP, whichever is greater.
Soap bubble test the actuator housing.
2.8) Increase the supply pressure to the specified
system pressure (100 PSI if not specified).
2.9) Slowly decrease the sense pressure and adjust
the regulator screw until the air flow is 5-20
SCFH at the specified setting. Lock the
adjusting screw at this setting.
2.10) While immersing the outlet tube in water,
increase the sense pressure until the regulator
is bubble tight. If this pressure exceeds 15%
or 2" WC greater than the set pressure,
examine the seat and O-Ring. Do not adjust
the regulator screw to improve bubble
tightness.
2.11) Remove the bonnet vent. Shut off the supply
pressure. Slowly decrease the sense pressure
to zero, while observing the stroke of the
piston thru the bonnet vent port. The stroke
must be 0.18" minimum. Replace the bonnet
vent.
3.0) Test report data.
3.1) The following data should be recorded for
future reference:
Model, Tag & Serial numbers
Test
media
Body & Actuator shell test pressure
Supply
pressure
Set
pressure
Bubble tight pressure