Groth 8450.0 User Manual
Installation, Operation, Maintenance
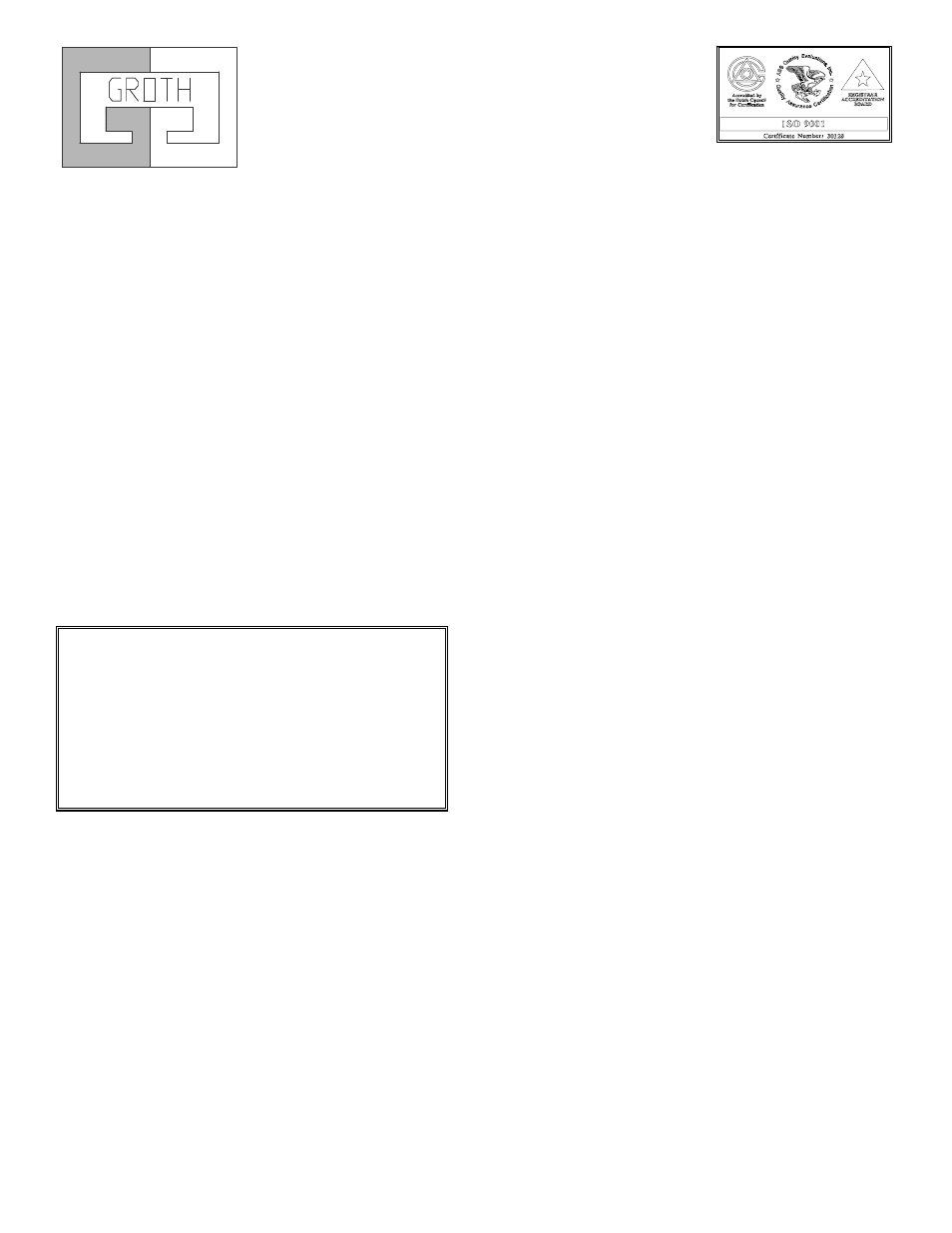
1
©
IOM 8450.0
November 1994
INSTALLATION, OPERATION AND MAINTENANCE
GROTH MODEL 8450 AUTOMATIC DRIP TRAP
Installation:
The drip trap should be installed with the axis of the
bowl in a horizontal position and the inlet/outlet
ports along a vertical axis with the outlet at the
bottom. Additionally, the bowl should be oriented
with the small plugged drain port at the bottom. If
the condensate is to be piped away, use appropriate
fittings, pipe and/or tubing to pipe away at the 1”
outlet port only. Do not pipe away at the small
plugged drain port. Provide sufficient clearances
for easy access to perform maintenance when
required.
WARNING
The model 8450 should not be used in systems
with pressure exceeding 10 psig. Higher system
pressure may prevent the drip trap from open-
ing. Align and install inlet and outlet piping so
that no undue stress is imposed on the drip trap.
Do not overtighten threaded connections;
damage or breakage may result.
Operation:
The operation of the drip trap is fully automatic.
When the liquid level rises sufficient to lift the float,
the seat will open to drain. The seat will close when
the liquid level drops in the bowl. The geometry of
the float and seat is such that the seat will close
when the liquid level is still above the seat. This
provides a liquid seal to prevent gas from escaping.
Maintenance:
It is important to regularly inspect and clean drip
traps and their seating surfaces. Frequency of
maintenance depends on the severity of the service.
Before any maintenance is attempted, be certain that
all pressure to the inlet is blocked and internal
pressure has been safely vented.
To clean, remove the bowl [1] from the cover [6]
and clean as required. No further disassembly is
necessary unless worn parts need replacing.
If disassembly is necessary, refer to the assembly
drawing,
C-85052
(or
similar
drawing).
Reassemble in reverse order with special attention
to the following:
1. Inspect the drilled hole in the seat bushing [10].
It must be completely cleaned or it will obstruct
the discharge of liquid. Lap the plunger [12]
and bushing [10] together if there is corrosion
or pitting on the seating surfaces; replace as
required.
2. The flat washer-like plastic thrust bearings [16]
should be installed adjacent to the pivot arm,
one on each side.
3. The single longer sleeve bearing [18] fits inside
the pivot arm and the two shorter ones [17] fit
between the thrust bearing and the cast ears, one
on each side of the pivot arm.
4. The threaded rod [8] attached to the float [9]
should be adjusted while the cover [6] is in the
normal vertical position (seat closed). The gap
between the end of the threaded rod [8] and the
cover [6] should be 1/8" to 3/16".
NOTICE: Please specify model, size and serial number when ordering
replacement part