Troubleshooting summary general, 3 troubleshooting summary general – Bronkhorst Mini CORI-FLOW User Manual
Page 36
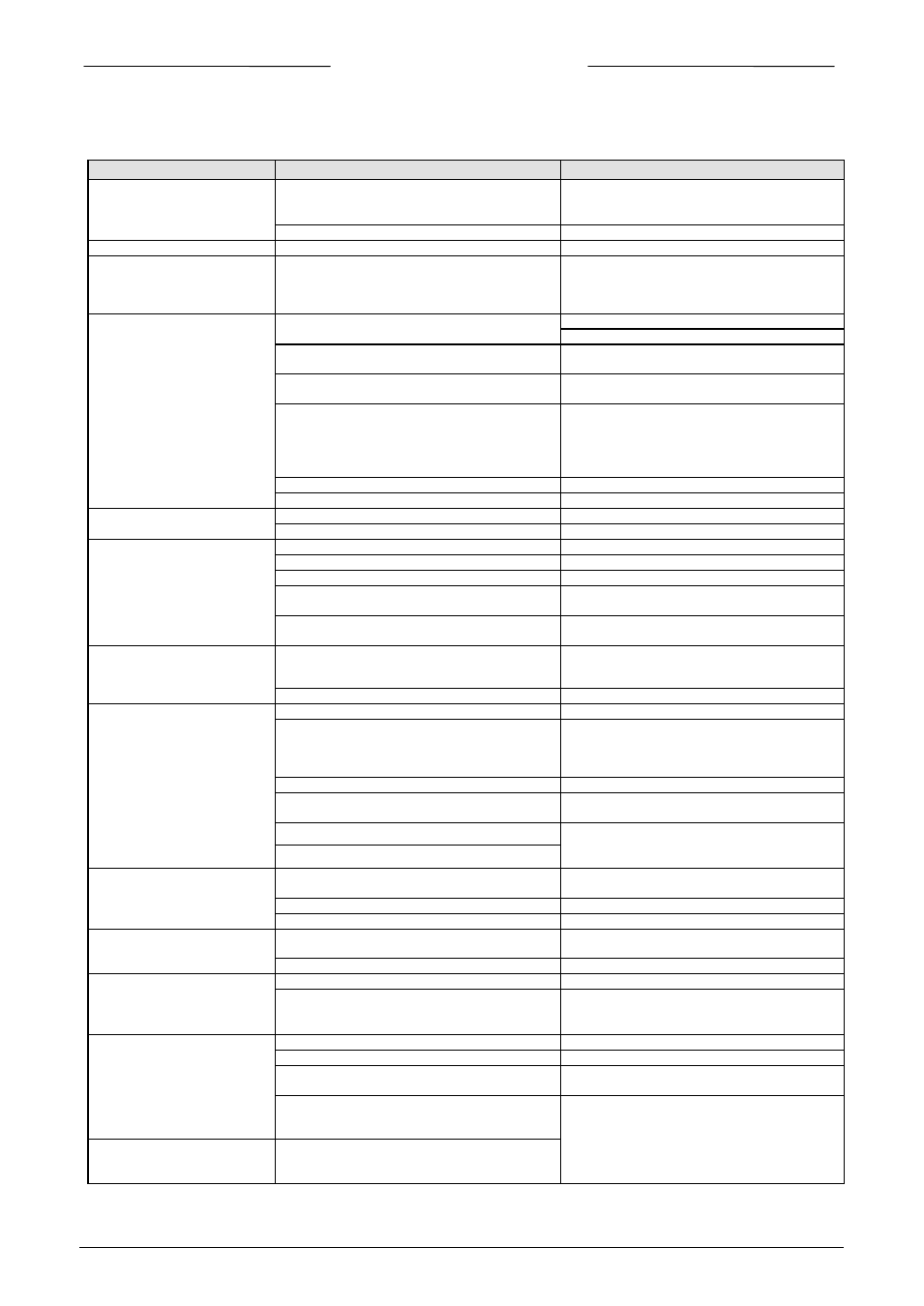
BRONKHORST CORI-TECH B.V.
6.3 Troubleshooting summary general
Symptom
Possible cause
Action
Red LED is irregular or
continuously on.
Gas bubbles in tube (of liquid meter)
Purge to get rid of gas bubbles
Advise: use frequency and/or density signal
to detect if gas or liquid is in the tube.
Too much vibrations
Mount isolation rubbers and flexible tubing.
Red LED is continuously on
Hardware error
Have instrument checked by specialist
Wanted flow is not reached
Clogging of the instrument
Purge at outlet and/or inlet with dry air if
possible and compare max flow with fixed inlet
pressure to values in the table of the brochure
or using CoriCalc pressure calculations.
No output signal
No power supply
1a) check power supply
1b) check cable connection
Output stage damaged due to long lasting
shortage and/or high-voltage peaks
1c) return to factory
Supply pressure too low, or differential pressure
across meter too low
1d) increase supply pressure
Valve blocked/contaminated
1e) connect 0 .. 15 Vdc to valve and slowly
increase voltage while supply pressure is ‘on’.
The valve should open at 7V ± 3V; if not open,
then clean parts and adjust valve (qualified
personnel only)
Piping or filters blocked
1f) clean system
Sensor failure
1g) return to factory
Maximum output signal
Output stage damaged
2a) return to factory
Sensor failure
2b) return to factory
Output signal much lower than
setpoint signal or desired flow
Piping or filters blocked/contaminated
3a) clean system
sensor blocked/contaminated
3b) clean sensor with a gas or fluid
Valve blocked/contaminated
3c) clean valve
Valve internal damage (swollen seat in plunger)
3d) replace plunger assembly and adjust valve
or return
Incorrect type of gas is used and/or
pressure/diff. pressure is to low
3e) try instrument on conditions for which it was
designed
Flow is gradually decreasing
Condensation, occurs with
NH
3
, hydrocarbons
such as
C H ,C H
3 8
4 10
etc.
4a) decrease supply pressure and/or heat gas
to be measured
Valve adjustment has changed
4b) see ‘1e’
Oscillation
Supply pressure/diff. pressure too high
5a) lower pressure
Pipeline too short between pressure regulator
and mini CORI-FLOW
5b) increase length or diameter of piping
upstream
Increase between pressure regulator and mini
CORI-FLOW
External vibration is present
5c) Remove external vibration
Valve sleeve or internals damaged
5d) replace damaged parts and adjust valve,
see ‘1e’ or return to factory
Controller adjustment wrong
5e) adjust controller
Software like FLOWPLOT can be used to do
this. Please contact the distributor for details.
Unstable upstream pressure
Small flow at zero setpoint
Valve leaks due to damaged plunger or dirt in
orifice
6a) clean orifice and/or, when replacing plunger
assembly, see ‘1e’
Pressure too high or much too low
6b) apply correct pressure
Zero procedure not done or with gas in the tube
6c) Purge and Zero the instrument
High flow at zero setpoint
Damaged diaphragm (only applicable to valves
with membrane)
7a) replace membrane seal
Zero procedure not done or with gas in the tube
7b) Purge and Zero the instrument
Disturbances in the flow
Gas in the system
8a) Purge the system
Expansion of liquids to gasses
8b) Check properties fluid used
Advise: use frequency and/or density signal
to detect if gas or liquid is in the tube
Calibration error
Zero procedure not done or with gas in the tube
9a) Purge and Zero the instrument
Gas in the system
9b) Purge the system
Measure time to short
9c) Measure long enough to get a reliable
measurement
Right reference instrument
9d) The mini CORI-FLOW is a mass-flow
meter/controller and should not be checked with
a volume-meter.
Totalization error
Pulsating or fast changing flow
Used special CORI-FILL (> 8V16) firmware
specially optimized for totalizing flow.
(Use dampener to stabilize inlet pressure.)
Note: For other (more specific) problems see also troubleshooting parts in other documents.
page 36
9.17.050