BECKHOFF CX51x0 User Manual
Page 9
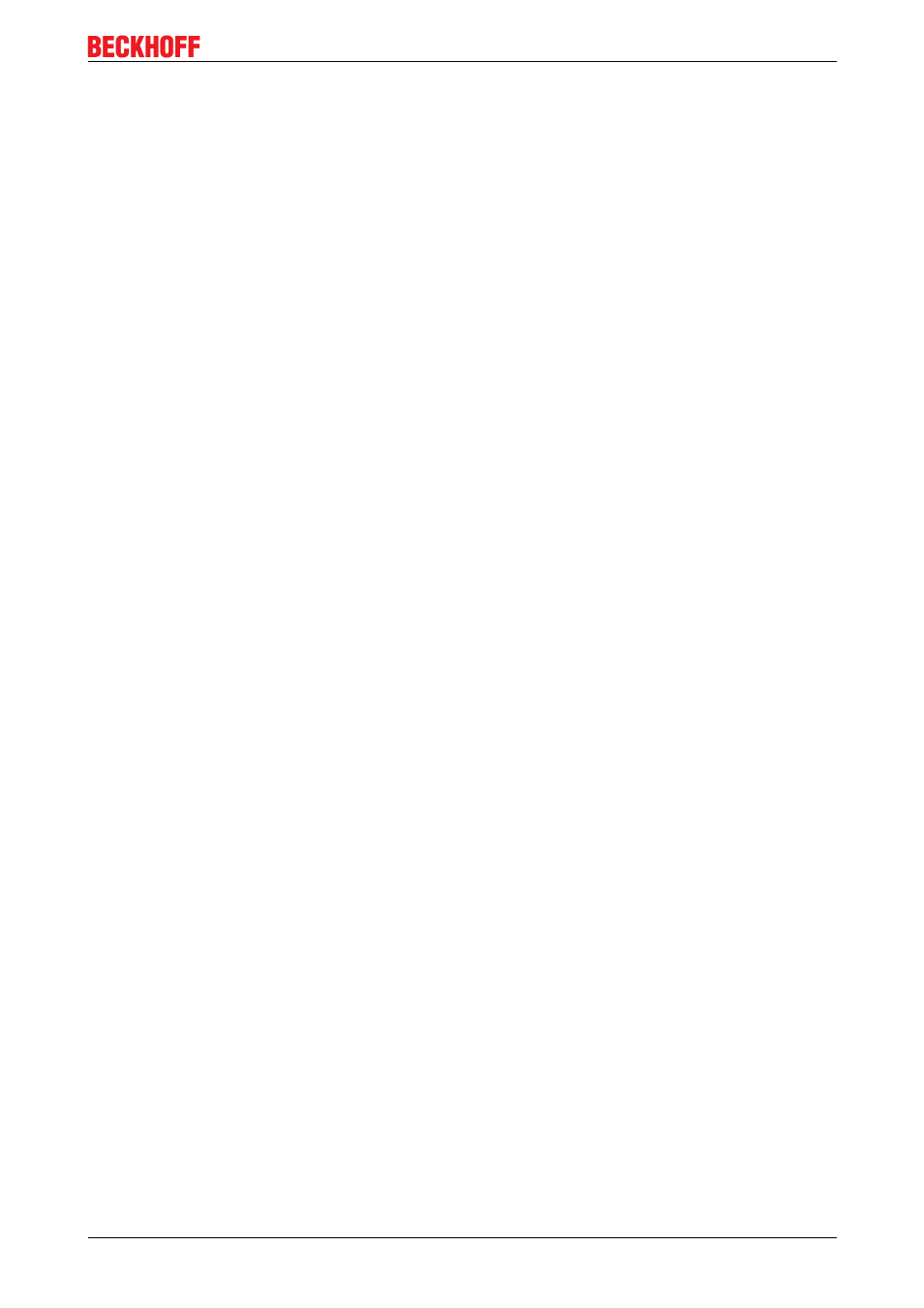
Product overview
In addition to realtime execution of control tasks, the TwinCAT realtime kernel ensures that enough time
remains for the user interface (HMI), to communicate with the realtime components via software interfaces
such as ADS or OPC.
For CX51x0 the familiar basic principle applies: it is a programming tool for all controllers.
The complete programming of PLC, Motion Control and visualization is transferable to all PC controls from
Beckhoff, which is reassuring in cases where it becomes apparent during a project that more processing
power is required after all. In this case a system with higher performance can be used.
Optional interfaces:
The optional interfaces can be used to connect singlechannel fieldbus interfaces. Operation is limited to one
interface at a time. If several fieldbus interfaces are required, they can be added as Ebus terminals
(EL67xx). The following fieldbus interfaces are available:
• CX51x0N030 = RS232, DSub connector
• CX51x0N031 = RS422/RS485, DSub socket
• CX51x0M310 = PROFIBUS master, DSub socket, 9pin
• CX51x0B310 = PROFIBUS slave, DSub socket, 9pin
• CX51x0M510 = CANopen master, DSub connector, 9pin
• CX51x0B510 = CANopen slave, DSub connector, 9pin
• CX51x0M930 = PROFINET RT, controller, Ethernet (2 x RJ45 switch)
• CX51x0B930 = PROFINET RT, device, Ethernet (2 x RJ45 switch)
• CX51x0B951 = Ethernet/IP slave, Ethernet (2 x RJ45 switch)
• CX51x0B100 = EtherCAT slave, EtherCAT IN and OUT (2 x RJ 45)
• CX5130N020 = second DVID interface
• CX5140N020 = second DVID interface
The software
In combination with the TwinCAT automation software, the CX51x0 Embedded PC becomes a powerful IEC
611313 PLC with up to four user tasks. Additionally, Motion Control tasks can also be executed. Depending
on the required cycle time, several servo axes can be controlled. Even special functions such as “flying saw”,
“electronic gearbox” and cam plate can be realized.
The CX51x0 system is programmed in the same way as other bus controllers:
Remote programming via Ethernet
The CPU generally features a PLC runtime. A laptop or a desktop PC connected with the CX via Ethernet
(network) is used for programming. The programs are developed on the laptop with a standard TwinCAT
software license and then loaded into the target device.
Visualization
The visualization feature integrated in TwinCAT can be used, or one of the other commercially available
visualization solutions. The Beckhoff OPC server is available for interfacing with SCADA packages. In other
words, the CX51x0 also offers visualization and simultaneous control in realtime on a single system.
CX51x0
9
Version 1.0