Instructions – Basler Electric AVC63-7 User Manual
Page 2
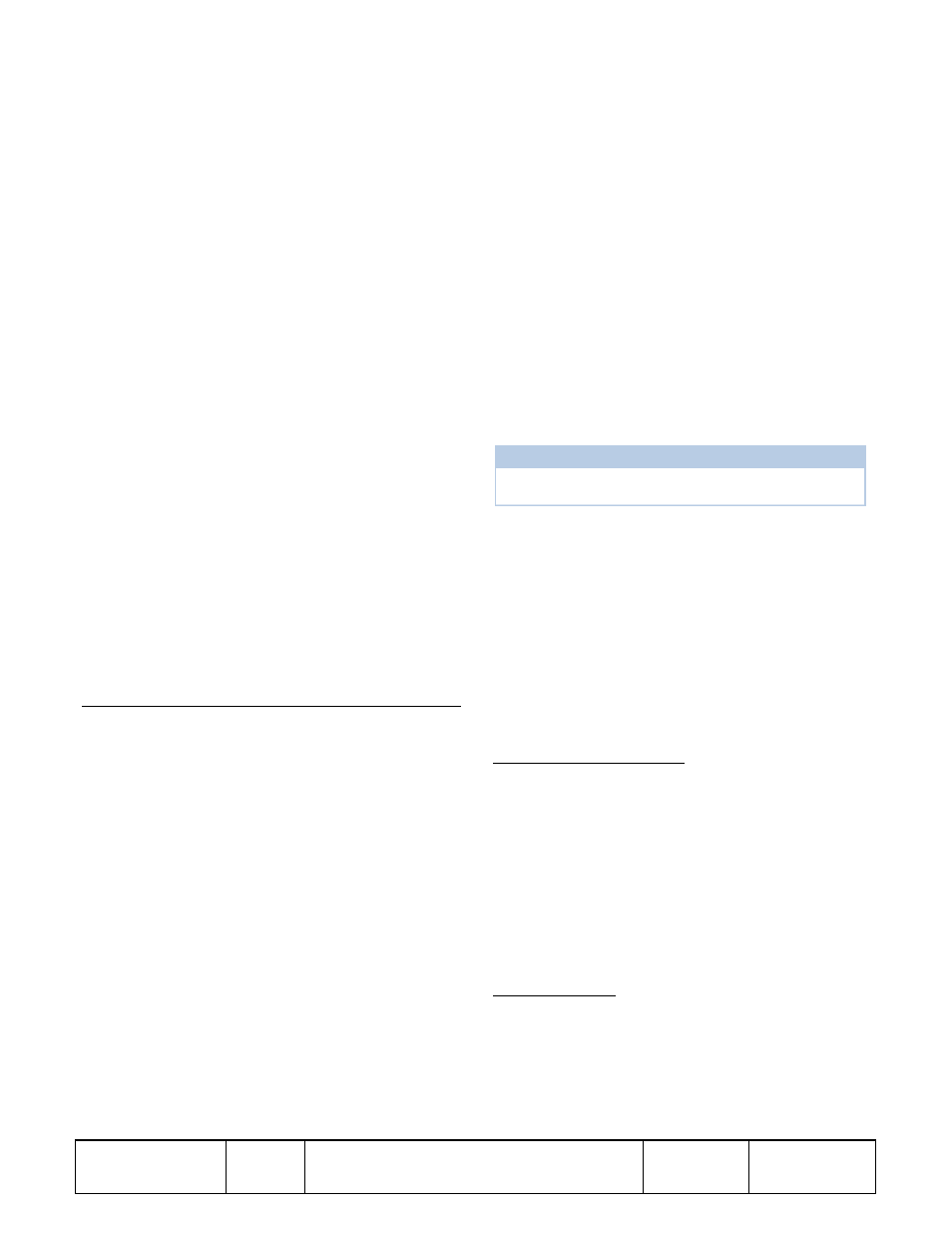
Publication
9302800991
Revision
B
Instructions
Date
03/12
Page
2 of 4
Figures 4 and 5 show the correct CT polarity for ABC phase
rotation sequence. If the phase rotation sequence is ACB,
the CT secondary leads must be interchanged.
Reactive Droop Compensation
For reactive droop compensation, connect the CT to its
respective regulator as shown on Figures 4 and 5.
A unit-parallel switch shorts the parallel CT secondary to
prevent any droop signal from being injected into the
regulating system during single unit operation. The switch
may not be required on parallel droop compensation
applications where a voltage drop is not objectionable.
Reactive Differential Compensation
On parallel reactive differential compensation applications a
contact should be used to short out the paralleling CT
secondary when that generator is not paralleled to the bus.
If the switch is not used, a voltage droop will be introduced
into the system. This is due to the unloaded generator
parallel CT not supplying its compensating signal, but
allowing a voltage drop to occur across it. Lack of this
shorting contact will also cause the voltage of the incoming
generator to fluctuate prior to paralleling. Ideally, this contact
is an auxiliary on the circuit breaker contactor that opens
when the circuit breaker is closed.
For reactive differential compensation, connect each CT to
its respective regulator. Then connect the finish of the first
CT to the start of the second CT, the finish of the second CT
to the start of the third CT, etc. Continue until all CT’s are
connected in series. The final step will be to connect the
finish of the last CT to the start of the first CT. (See Figure
5).
Reactive differential compensation cannot be used when
paralleled with the utility or any infinite bus. If this
compensation system is used, a switching circuit must be
used to convert the system to a reactive droop
compensation system. Contact the factory for additional
information.
OPERATION
The following procedures provide instructions for setting up,
starting, operating, and adjusting the AVC 63-7 Voltage
Regulator. Symptoms of problems occurring during startup
that result from incorrect regulator adjustment and certain
generator system problems that resemble faulty regulation
are included together with possible solutions.
Preliminary Setup
To prevent damage to the regulator, complete the following
steps before proceeding with system startup.
1. Verify that the voltage regulator specifications conform
to the generator system requirements.
2. Ensure that the regulator has been installed and
connected in accordance with the paragraphs on
installation.
Operation at Reduced Speeds
During periods of prime mover idling, use the shutdown
switch to remove power from the regulator.
System Startup
1. Perform preliminary setup as described in the above
paragraphs.
2. Start the prime mover and bring up to rated speed.
Result: Voltage should build up. If not, perform field
flashing.
3. Slowly adjust VOLT adjustment or external voltage
adjust rheostat until the generator output voltage
reaches the nominal value.
4. Apply and remove load to check stability.
5. Check the regulator under normal operating conditions.
Result: If regulation is not within range, verify the prime
mover is at rated speed.
6. Reduce generator frequency to approximately 5 Hz
below nominal.
Result: Generator output voltage should decrease at
desired frequency.
Adjustments
Field Flashing. When the regulator is operated with the
generator for the first time, the polarity of the residual
magnetism may not be correct or of sufficient magnitude. If
the residual voltage at terminals 3 and 4 is greater than 6
Vac, replace the regulator. If generator residual voltage is
less than 6 Vac at terminals 3 and 4, shut down the prime
mover and proceed with the following steps.
CAUTION
Do not flash the field with the generator in motion.
Damage to the regulator may result.
1. With the prime mover at rest, apply a dc source
(ungrounded), of not more than 48 Vdc, to terminals F+
(positive) and F– (negative) in series with a limiting
resistor. Use one ohm of resistance for each volt from
the dc power source with a power rating of least one
watt per ohm.
EXAMPLE: If using a 24 Vdc source, use a 24 ohm, 24
watt resistor.
2. Allow the field to be flashed for approximately 10
seconds before removing the dc source.
3. If voltage buildup does not occur after performing steps
1 and 2, verify the polarity of the dc source used in
steps 1 and 2 and perform again.
The AVC 63-7 underfrequency adjust is factory preset to
cause an average 1 volt drop in the generator's line input
voltage to the regulator when the frequency is between 54.5
and 55.5 Hz (for 60 Hz applications). For 50 Hz applications,
the frequency roll-off is factory preset to between 44 and 46
Hz. To reset the frequency roll-off, proceed as follows:
Frequency Roll-Off Adjustment
1. Adjust the prime mover rpm to the desired frequency
compensation (corner frequency roll-off) point.
2. Adjust the front panel FREQ control CW until the output
voltage starts to drop off.
3. Bring the prime mover up to rated speed. The output
voltage should return to normal.
An oscilloscope or other voltage recording device should be
used if a stability setting is desired that will provide the
fastest possible voltage response with good generator
stability.
Stability Adjustment
1. Rotation of the front panel STAB control in the
clockwise (CW) direction will slow response time.