Error code & troubleshooting – Delta Electronics Position Control Module DVP01PU-H User Manual
Page 2
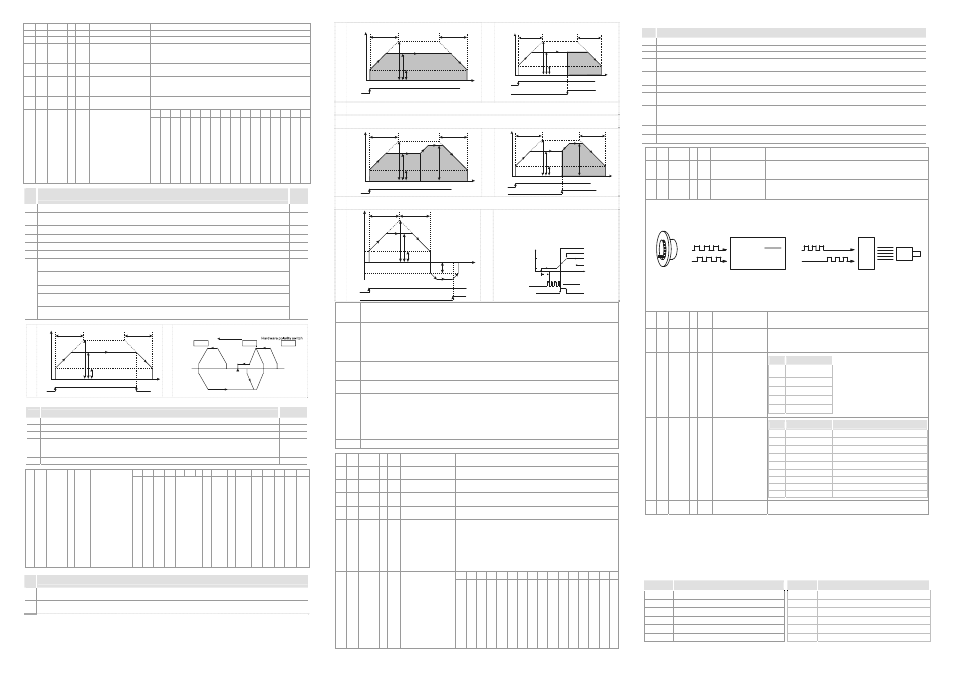
#20 #19 H’41A3 9 R/W Zero point setting (HP) Range: 0 ~ ±999,999 unit*1, factory setting: 0 unit*1
#21 H’41A5 9 R/W Acceleration time T
acc
Range: 10 ~ +32,767 ms, factory setting: 100 ms
#22 H’41A6 9 R/W Deceleration time T
dec
Range: 10 ~ +32,767 ms, factory setting: 100 ms
#24 #23 H’41A7
╳
R/W Target position (I) P(I)
Range: -2,147,483,648 ~ +2,147,483,647 unit*1
(-2,147,483,648 ~ +2,147,483,647 pulse transfer value) *2,
factory setting: 0 unit*1
#26 #25 H’41A9
╳
R/W Running speed (I) V(I)
Range: -2,147,483,648 ~ +2,147,483,647 unit*1 (10 ~ 200K
PPS pulse transfer value) *2, factory setting: 1,000 unit*1
#28 #27 H’41AB
╳
R/W Target position (II)P(II)
Range: -2,147,483,648 ~ +2,147,483,647 unit*1
(-2,147,483,648 ~ +2,147,483,647 pulse transfer value) *2,
factory setting: 0 unit*1
#30 #29 H’41AD
╳
R/W
Running speed (II)
V(II)
Range: 0 ~ +2,147,483,647 unit*1 (10 ~ 200K PPS pulse
transfer value) *2, factory setting: 2,000 unit*1
b15 b14 b13 b12 b11 b10 b9 b8 b7 b6 b5 b4 b3 b2 b1 b0
#31 H’41AF
╳
R/W
Running instruction
factory setting: H’0000
-
-
CLR output (On/Of
f)
CLR signal output mode
-
Current position = 0 (CP=0)
-
Sof
tware ST
AR
T
ABS/REL
Coordinate
Zero return st
art
JOG-
JOG+
CCW pulse ST
OP
CW pulse ST
OP
Sof
tware ST
OP
Error reset
bit
#
Description
Timing
0 When b[0]=1, Error reset. Error indicator is off and FLAG in CR (CR#43.b[5]) is cleared to 0.
0→1
1
When b[1]=0→1 ,this is the same function as external input signal that forces to stop. When
external signal that forces to stop is inputted or when b[1]=0→1, PU will decelerate to stop.
0→1
2 When b[2]=1, CW running is forbidden, CW running instruction is disabled.
1
3 When b[3]=1, CCW running is forbidden, CCW running instruction is disabled.
1
4 When b[4]= 0→1, CW pulse is generated in JOG+ mode.
1
5 When b[5]= 0→1, CCW pulse is generated in JOG- mode.
1
When b[6]=0→1, zero return is performed. Zero return is performed differently by the different
current position (CP) as the four following conditions:
Position(1): Start position (as the right picture below [1] ) is at the right of zero point and DOG(near
point signal), DOG=Off.
Position(2): Start position (as the right picture below [2] ) is at the right of zero point, DOG=On.
Position(3): Start position (as the right picture below [3] ) is at the left of zero point and DOG(near
point signal), DOG=Off and LSN (hardware limit switch) signal=Off.
6
Position(4): Start position (as the left picture below [4] ) is at the left of zero point and DOG(near
point signal), DOG=Off and LSN (hardware limit switch) signal=On.
0→1
JOG operation
mode
Speed
Tacc
Tdec
Vmax
Time
Vbias
JOG
Vjog
Zero return operation route
LSN
DOG
LSP
Hardware polarity switch
Zero point return direction
Zero point
[4]
[3]
[2]
[1]
bit #
Description
Timing
7
When b[7]=0, it is absolute position. When b[7]=1, it is relative position.
0/1
8
When b[8]=0→1, start running by the work mode of CR#32.
0t1
10 When b[10]=0→1, current position (CP) is cleared to 0.
0t1
12
When b[12]=0, CLR outputs 130ms to Servo when zero return is completed. It is for the clear
signal of servo internal error counter.
When b[12]=1, CLR is common output point and the status(On/Off) is controlled by b[13].
0/1
13 When b[13]=0, CLR output point is Off. When b[13]=1, CLR output point is On.
0/1
b15 b14 b13 b12 b11 b10 b9 b8
b7
b6 b5
b4 b3 b2 b1
b0
#32 H’41B0
╳
R/W
Work mode
factory setting:
H’0001
-
-
-
Return to factory setting
MASK settin
g
LSP/LSN sto
p mode
Manual pulse generator range setting
ST
OP
mode
Manual pulse generator input operation
V
ariable speed operation mode st
art
Interrupt 2nd-speed position mode st
art
2nd-speed position mode st
art
Interrupt 1st-speed position mode st
art
1st-speed position mode st
art
bit
#
Description
0
When b[0] is triggered and START ON, it starts to execute 1st-speed position program. Step number and
speed are decided by P(I)& V(I).
1
When b[1] is triggered, START ON, and DOG external near point signal is performed, it starts to reload the
value of the target position (I) P(I).
1st
-speed position
operation m
ode
Speed
Tacc
Tdec
Vmax
Time
Vbias
Start
V(I)
P(I)
Interrupt 1st
-speed position
operation
mode
Speed
Tacc
Tdec
Vmax
Time
Vbias
Start
V(I)
P(I)
DOG
2
When b[2] is triggered and START ON, it starts to execute 1st-speed position operation and then the
2nd-speed position operation will be started immediately after 1st-speed operation is completed.
3
When b[3] is triggered and START ON, if the DOG external near point signal is executed during 1st-speed
position operation, the 2nd-speed position operation will be started immediately.
2nd
-sp
eed position
operation mode
Speed
Tacc
Tdec
Vmax
Time
Vbias
Start
V(I)
V(II)
P(II)
P(I)
Interrupt 2nd
-speed
position
operation mode
Speed
Tacc
Tdec
Vmax
Time
Vbias
Start
DOG
V(I)
V(II)
P(II)
4
When b[4] is triggered, it starts to execute variable speed operation and PU starts to send pulse as well.
The pulse direction is set by the sign bit of V(I) value.
V
ariable speed operation mode
Speed
Tacc
Vmax
Time
Vbias
Start
Stop
V(I)
Vbias
0
Tdec
Zero return operation mode
Description Chart: (1)DOG rising-edge is triggered in
normal mode. (2)DOG falling-edge detecting is On in zero
return mode (CR#18_b1,0=00). (3)the number of PG0 in
zero return mode N(CR#16). (4)the number of pulse in
zero return mode P(CR#17).
Speed(PPS)
VCR
VRT
VCR
DOG
Isolate from DOG near signal
Contact DOG near signal
Zero return direction
The number of PG0 in zero return mode (N)
DOG falling-edge detecting
The number of pulse in zero return mode (P)
5
When b[5]= 0→1, manual pulse generator input is started. Please refer to the setting of CR#45~#51.
When b[5]=1Æ0, manual pulse generator input is stopped. Also, b[5] can start running by activating
START command.
6
b[6]=0: When STOP is input, motor will decelerate to stop under running mode. When rerun instruction
is received, the distance that uncompleted will be neglected and motor will go to execute the
next position instruction immediately.
b[6]=1: When STOP is input, motor will decelerate to stop under running mode. When rerun instruction
is received, the distance that uncompleted will be done and then motor will go to execute the
next position instruction.
7
b[7]=0: The output pulse of manual pulse generator is unlimited.
b[7]=1: The output pulse of manual pulse generator is limited between P(I) and P(II). When the output
pulse is out of the range, it will be decelerated and then stopped outputting.
8
b[8]=0: When motor is running, it will decelerate to stop if LSP/LSN signal is received.
b[8]=1: When motor is running, it will stop immediately if LSP/LSN signal is received.
9~11
MASK setting (1st-speed operation, 2nd-speed operation, interrupt 1st-speed operation, interrupt
2nd-speed operation)
b[11~9]=K0(000) or other value: NO MASK function.
b[11~9]=K1(001) : the rising-edge of input terminal ΦA± will trigger MASK.
b[11~9]=K2(010) : the falling-edge of input terminal ΦA± will trigger MASK.
b[11~9]=K3(011) : the rising-edge of input terminal ΦB± will trigger MASK.
b[11~9]=K4(100) : the falling-edge of input terminal ΦB± will trigger MASK.
12
b[12]=1: All parameters return to factory setting.
#34 #33 H’41B1
╳
R/W
Current position
CP(PLS)
Range display: -2,147,483,648~+2,147,483,647 PLS, factory
setting: 0 PLS
#36 #35 H’41B3
╳
R/W
Current speed CS
(PPS)
Range display: 0 ~ +2,147,483,647 PPS, factory setting: 0
PPS
#38 #37 H’41B5
╳
R/W
Current position
(unit*1)
Range display: -2,147,483,648~+2,147,483,647 unit*
1
, factory
setting: 0 unit*
1
#40 #39 H’41B7
╳
R/W
Current speed
(unit*1)
Range display: 0 ~ +2,147,483,647 unit*
1
, factory setting: 0
unit*
1
#41 H’41B9 9 R/W
Communication
address
RS-485 communication address, range: 01~255, factory
setting: K1
#42 H’41BA 9 R/W Baud Rate Setting
Baud rate setting: 4800, 9600,19200bps, 38400 bps, 57600
bps, 115200 bps. ASCII mode data format is 7Bit, even bit and
1 stop bit (7 E 1). RTU mode data format is 8Bit, even bit and 1
stop bit (8, E, 1)
b0: 4800 bps(bit/sec.), b1: 9600 bps(bit/sec.) (factory setting)
b2: 19200 bps(bit/sec.), b3: 38400 bps(bit/sec.)
b4: 57600 bps(bit/sec.), b5: 115200 bps(bit/sec.)
b6~b14: reserved, b15: 0/1: RTU/ASCII mode(1: factory setting)
b15 b14 b13 b12 b11 b10 b9 b8 b7 b6 b5 b4 b3 b2 b1 b0
#43 H’41BB
╳
R/W
Execution status
factory setting:
H’XXXX
-
-
-
-
-
MPG input downward
MPG input upward
-
Route p
aused indication
Position completed indication
Error occurred flag
CP
value overflow
Zero return is done
CCW pulse is outputting
CW pulse is outputting
S
tatus indication
bit #
Description
0
When b[0]=0, system is ready. When b[0]=1, PU is executing position control mode (Pulse is outputting).
1
When b[1]=1, CW pulse is outputting.
2
When b[2]=1, CCW pulse is outputting.
3
When b[3]=1, zero return is completed. b[3] is cleared to 0 by user program. When PU is power on again,
b[3] will be cleared to 0 automatically.
4
When b[4]=1, “Current position CP(PLS)”(CR#34, #33), that is 32 bit, is overflow. When PU is power on
again or complete zero return, b[4] will be cleared to 0 automatically.
5
When b[5]=1, PU error occurred. Error code is stored in CR#44.
6
When PU starts to execute zero return or error reset (only when error occurred), it will clear b[6] to 0. When
zero return or position control is completed, it will set b[6] to 1.
7
When PU is running, STOP status is on. PU will stop output, and b[7] will be set to 1 at this time. It means
that PU is pause and it will execute the uncompleted route and b[7] will be cleared to 0 after STOP status is
off.
9
When b[9]=1, it means manual pulse generator inputs with counting upward.
10 When b[10]=1, it means manual pulse generator inputs with counting downward.
#44 H’41BC
╳
R
Error code
Please refer to “Error Code & Troubleshooting” for detail.
Factory setting: H’0000
#45 H’41BD
╳
R/W
Electronic gearing
numerator of MPG
input
Please refer to the following description. Factory setting: H’1
#46 H’41BE
╳
R/W
Electronic gearing
denominator of
MPG input
Please refer to the following description. Factory setting: H’1
z
Input operation of manual pulse generator:
1. Manual pulse generator input operation is ON when b5 of CR#32 is set to 1.
2. 2-phase(A phase/B phase) can be input from the manual pulse generator to ΦA and ΦB. FP/RP I/O pulse
is as follows:
A phase
B phase
FP
R
P
Servo drive
Servo motor
Input pulse X
= output pulse
CR#45
CR#46
3. When it arrives the (LSP/LSN) limit, output will stop immediately. When LSP is ON, CCW is allowed. When
LSN is ON, CW is allowed. The position complete flag is not turned ON.
4. Position complete indication (CR#43, b6=Off). When position is done, the actual operation is expressed:
(CR#43 b6=On).
5. The PU output pulse, pulse frequency of manual pulse generator, and the electronic gearing (CR#45,
CR#46) are proportional to each other.
#48 #47 H’41BF
╳
R/W
Input frequency of
manual pulse
generator
The input frequency of manual pulse generator, factory setting:
0
#50 #49 H’41C1
╳
R/W
Accumulated pulse
number of manual
pulse generator
The count value of CW manual pulse input is “ +” symbol, on
the contrary, the CCW manual pulse input is “-“symbol. And the
count value is nothing to do with the ratio setting of manual
electronic gearing (CR#45, #46). Factory setting: 0.
#51 H’41C3
╳
R/W
Response speed
of manual pulse
generator
Value Response speed
≧
5
4ms (factory
setting)
4 32ms
3 108ms
2 256ms
1or 0 500ms
When response speed setting is
faster, the commands of pulse output
and manual pulse generator input
will be more synchronous. When
response speed setting is slower, the
command of pulse output is slower
than the command of manual pulse
generator input. Factory setting: 5
#52 H’41C4
╳
R
Terminal status
bit #
Status
Description
b0 START input
When START input is On, b0 is On
b1 STOP input
When STOP input is On, b1 is On
b2 DOG input
When DOG input is On, b2 is On
b3 PG0 input
When PG0 input is On, b3 is On
b4 LSP input
When LSP input is On, b4 is On
b5 LSN input
When LSN input is On, b5 is On
b6 A phase input
When A phase input is On, b6 is On
b7 B phase input
When B phase input is On, b7 is On
b8 CLR output
When CLR output is On, b8 is On
#53 H’41C5 9 R
System version
System version: in hexadecimal system. Ex.: H’0100, the
software version is V1.00.
*1: Unit setting is according to the varying of “ b0, b1” unit setting of CR#5.
*2: Convert setting value to pulse unit: (1) output the maximum pulse if it exceeds the maximum range. (2) output the minimum
pulse if it’s lower than the minimum range.
[
Error Code & Troubleshooting
It indicates 01PU hardware malfunction or error parameter setting when error LED flashes. ERR code is recorded in
CR#44.
Error code
Description
Error code
Description
H’0000
No error
H’0013
Zero return deceleration (V
RT
) setting error
H’0001
Target address (I) setting error
H’0014
JOG speed (V
JOG
) setting error
H’0002
Target address (II) setting error
H’0020
CW pulse is forbidden
H’0010
Running speed (I) setting error
H’0021
CCW pulse is forbidden
H’0011
Running speed (II) setting error
H’0080
Hardware error in internal memory
H’0012
Zero return deceleration (V
CR
) setting error
H’0081
Data write in error in internal memory
The content of this instruction sheet may be revised without prior notice. Please consult our distributors or
download the most updated version at http://www.delta.com.tw/industrialautomation