A caution – Carrier 58DX User Manual
Page 4
Attention! The text in this document has been recognized automatically. To view the original document, you can use the "Original mode".
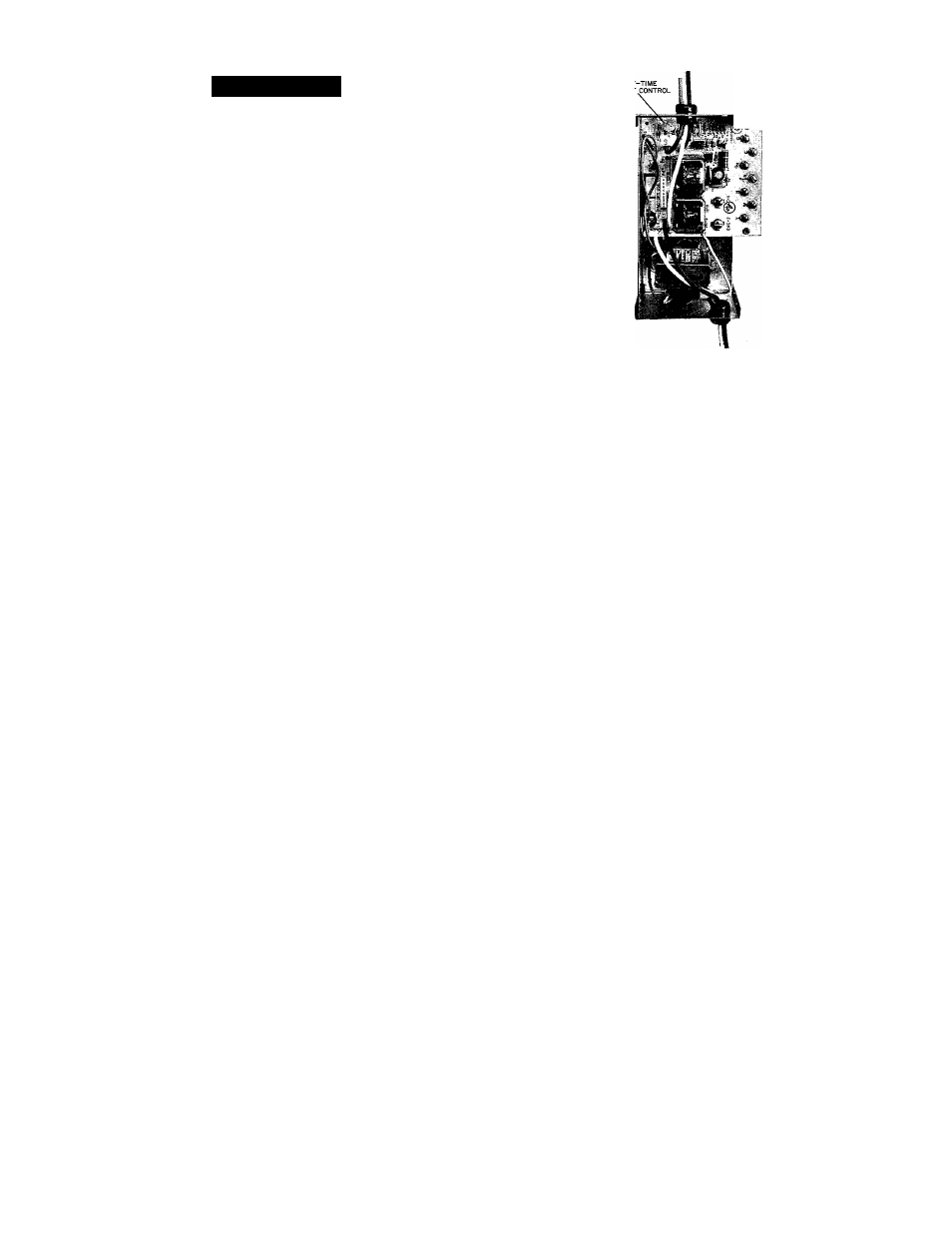
A CAUTION
If a manual disconnect switch is to be mounted on the
furnace, select a location where a drill or fastener will
not come in contact with electrical or gas components.
Check all electrical connections (both factory and field)
for tightness. This check should also be done after the
unit has reached operating temperatures.
If 115-volt wiring to the unit is encased in a nonmetallic
sheath, connect the incoming ground wire to the grounding
wire inside the furnace J-box. If properly grounded metallic
conduit is used, it will serve as the furnace ground.
B. 24-Volt Wiring
Make field 24-volt connections at the 24-volt terminal strip.
See Fig. 6.
NOTE:
Use AWG
No. 18
“color-coded” copper thermostat
wire for lengths up to 100 ft. For wire lengths over 100 ft,
use AWG No. 16 wire.
IMPORTANT:
The thermostat heat anticipation must be
set to match the amp draw of the gas valve and other elec
trical components in the R-W circuit. The amp reading
should be taken after the blower has started. The room ther
mostat should be located where it will be in the natural cir
culation path of room air. Avoid locations where the ther
mostat would be;
1. Exposed to cold-air infiltration.
2. Exposed to drafts from windows, doors, or other open
ings leading to the outside.
3. Exposed to air currents from warm- or cold-air
registers.
4. Located behind doors, above or below shelves, mantels,
or any other location where the natural circulation of
air is cut off.
5. Exposed to heat from fireplaces, radios, televisions,
lamps, or the rays of the sun.
6. Located on a wall containing pipes or warm-air ducts,
or flue or vent pipes.
7. Located on a wall that is inadequately sealed from the
attic, crawlspace, or basement.
Any hole in the plaster or panel through which the wires
pass from the thermostat should be adequately sealed with
suitable material to prevent drafts from affecting the
thermostat.
C. Blower Control Center
Each furnace features a blower control center. This device
will aid the installer and service technician when installing
or servicing the unit. A 24-volt terminal strip is marked for
easy connection of field wiring. See Fig. 7.
The blower control center features an adjustable blower-off
timing device. The “off” timing delay cem be varied over a
range of
80 to 240
seconds by turning the “off” timing
adjustment control in the direction indicated on the label
attached to the side of the control box. After a change in
adjustment, the time-delay circuit must be energized at
least 4 minutes to achieve the new “off” time delay setting.
The “off” timing adjustment is set at the factory for a delay
of approximately 240 seconds. See Fig. 7. The on-time delay
is not adjustable (60 seconds).
VIII. SEQUENCE OF OPERATION
Heating Cycle
The control circuit of the furnace shown in the schematic
wiring diagram. Fig. 8, results in the following sequence of
Km
Fig. 7—Blower Control Center
A87298
operation for the heating cycle:
5.
6
.
When the blower door is in place, 115 VAC is supplied
through blower door interlock switch ILK. Trans
former TRAN is energized, supplying 24 VAC to heat
ing blower relay HFR, which opens normally-closed
blower relay contacts HFR in the low-speed circuit of
blower motor MTR.
2.
The wall thermostat “calls for heat,” closing thé R and
W circuit. This closed circuit supplies power to the 24-
VAC safety circuit containing automatic reset limit
switch LSI and manual reset auxüiary limit switch
LS2. Auxiliary limit switch LS2 will break electrical
circuit to gas valve if blower compartment or filters
overheat. The switch must be manually reset after
cause of overheat condition is corrected.
3. The inducer motor relay coU IDR is energized. Inducer
motor relay contacts in the 115-VAC circuit close,
starting inducer motor IDM. Simultaneously, another
set of contacts in inducer motor relay IDR close in the
24-VAC circuit, and lock in inducer motor relay coil
IDR. The coil is locked in until the R and W circuit or
safety circuit opens.
4. As inducer motor IDM comes up to speed, flow sensing
switch AFS actuates energizing the PILOT solenoid
coil of gas valve GV and the time-delay relay in spark
generator ICP through fusible link FL.
When the PILOT solenoid coil is energized, gas flows
to the pilot. The internal pressure switch within gas
valve GV senses the pilot gas pressure and closes, com
pleting the HOLD circuit. The normally open time-
delay relay within spark generator ICP closes after a
10-second purge delay, energizing spark generator. The
pilot gas is ignited by a spark produced by spark
generator.
After a short time delay, during which the pilot flame
heats up flame sensing contacts PS, the normedly
closed contacts PS open. The PILOT solenoid coil
remains energized through the HOLD circuit. Spark
generator ICP shuts off when flame is sensed at the
spark electrode. The normally open flame-sensing con
tacts PS close 5 to 20 seconds later, energizing the
MGV solenoid coil of the GV. Six to 15 seconds later,
the MGV solenoid opens, allowing gas to flow to the
main burners where the gas is ignited by the pilot
flame.
7. Simultaneously, time-delay circuit AR in the blower
control center is energized. Approximately 50 seconds
I