Controls (cont) – Carrier 30GB060 User Manual
Page 12
Attention! The text in this document has been recognized automatically. To view the original document, you can use the "Original mode".
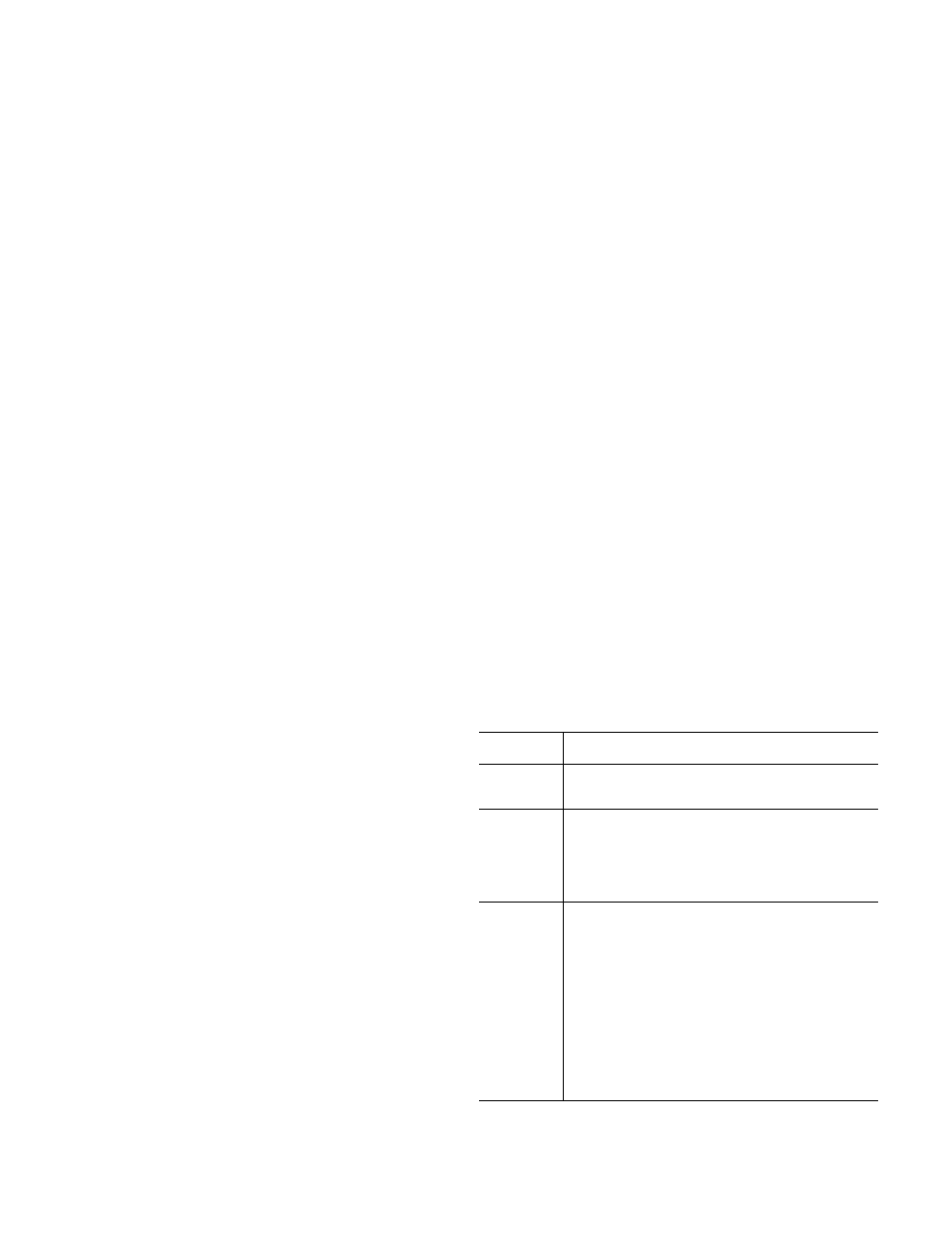
Controls (cont)
compressor runs to pump out any refrigerant that has
migrated to the cooler. The oil pressure switch is bypassed
for one minute during start-up and for 45 seconds during
normal operation.
Thermistors — Eight thermistors are used for tempera
ture sensing inputs to microprocessor. (A ninth [TIO]
may be used as a remote temperature sensor for optional
LCWT reset.)
T1 Cooler leaving chilled water temperature
T2 Cooler entering water (return temperature)
T3 Saturated condensing temperature — Circuit #1
T4 Saturated condensing temperature — Circuit #2
T5 Cooler saturation temperature — Circuit #1
T6 Cooler saturation temperature — Circuit #2
T7 Return gas temperature entering compressor
cylinder — Circuit #1
T8 Return gas temperature entering compressor
cylinder — Circuit #2
TIO Remote temperature sensor (accessory)
The microprocessor uses these temperatures to control
capacity, fan cycling and electronic expansion valve
(EXV) operation.
Electronic expansion valve (EXV) — To control flow
of refrigerant for different operating conditions, EXV
piston moves up and down over slot orifices through which
refrigerant flows to modulate size of opening. Piston is
moved by a stepper motor through 760 discrete steps. The
piston is repositioned by microprocessor every 3 seconds.
The EXV is used to control superheat in compressor.
Two thermistors in each circuit (T5 and T7/T6 and T8) are
used to determine superheat. One thermistor (T5/T6) is
located in cooler and other (T7/T8) in compressor after
motor in the gas passage entering the cylinders. The EXV
is controlled to maintain superheat entering pistons at
approximately 15 F (8.3 C) to20F (11.1 C), which results
in slightly superheated refrigerant leaving cooler.
Both on shutdown and start-up, unless compressor has
run in last 15 minutes, compressor runs for 10 seconds,
while EXV is closed and removes refrigerant from cooler.
These pumpout cycles minimize amount of excess
refrigerant that can go to compressor on start-up and cause
oil dilution which would result in eventual bearing wear.
The microprocessor software is programmed so that
EXV functions as an MOP. (maximum operating pressure)
valve, limiting the suction temperatures to 55 F (12.8 C).
This makes it possible to start unit at high water tempera
tures, up to 95 F (35 C), without overloading compressor.
Another feature that is factory set (which may be eliminated
in the field by repositioning a dip switch on the micro
processor) limits rate of pulldown to 1°F (0.6°C) per minute
thereby reducing the kW demand on start-up.
Accessory controls — Demand can be further limited
by keeping a selected number of compressors from
turning on by utilizing demand limit control accessory.
This interfaces with microprocessor to control unit so
that chiller’s kW demand does not exceed its setting.
It is activated from an external switch.
Microprocessor is programmed to accept various
accessory temperature reset options, based on return
water temperature, outdoor temperature, or space
temperature, that reset the LCWT. An accessory
thermistor (TIO, above) is required if outdoor tempera
ture or space temperature reset is elected.
Compressor protection and control system (CPCS)
(30GB060) — Compressor protection boards are used
to control and protect compressors. One board is used
for each compressor to control compressor contactor(s)
and crankcase heater(s) in response to a command from
microprocessor. The board also provides compressor
ground current protection, shutting off compressor if a
2 to 3 ampere ground current is sensed by a toroid around
the compressor power leads. A high-pressure protector
and a discharge gas temperature protector are connected
in series with CPCS board, so that if they open, compressor
stops. Microprocessor senses this through feedback
switch input.
The CPCS control system is available as an accessory
on 30GB060. The 30GB060 unit is factory equipped with
a control relay that operates same as CPCS except that
ground current refrigerant circuit protection is not
provided.
Complete electronic control system contains several
additional components.
Relay board — Relay board, connected to microprocessor
by a ribbon cable, drives all of 24-v, 115-v, or 230-v loads.
Relays control compressors, fans, and unloaders, if used.
Display board — Display board, also connected to
microprocessor by a ribbon cable, is used to communicate
with operator. In addition to leaving water set point
potentiometer, board contains 2-digit LED display. The
LED display is normally off after initialization period,
to extend its life. Pressing display button will result in
LED displaying the appropriate overload or status code.
If this is done, display will show from one to 3 codes
alternating every 2 seconds, as follows:
CODE
STATUS
1. 0-12
Capacity stage
Number of stages in operation
2. 20-24
Operating Mode
20
Initialization
21
Temperature Reset
22
Demand Limit
24
Pulldown Control
3. 51-87
Overload Codes
Alarm light/circuit energized.
NOTE: These codes take priority.
51-58
Compressor fault
59,60
Loss of charge (circuit 1, circuit 2)
61
Low water flow
63,64
Low oil pressure (circuit 1, circuit 2)
65
Low water temperature
70
Illegal configuration
71-80
Thermistor failure
81-87
Reset/Set Point/Limit Failure
These codes are summarized on a chart in each unit’s
control box, and are described in detail in the Controls
and Troubleshooting book.
12