Electrical data ~ 60 hz, Controls, Controls ,12 – Carrier 30GB060 User Manual
Page 11
Attention! The text in this document has been recognized automatically. To view the original document, you can use the "Original mode".
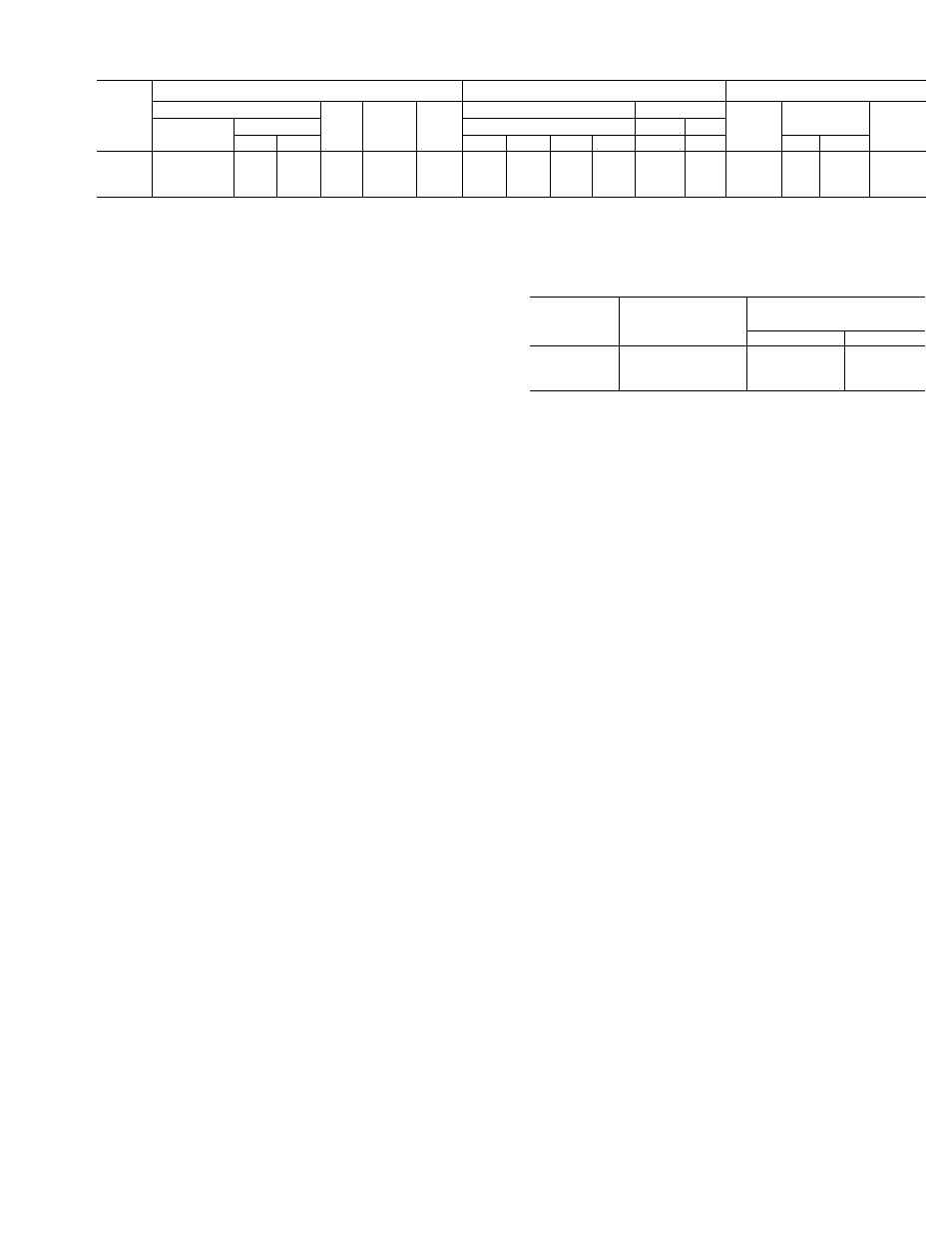
Electrical data ~ 60 Hz
30GB
UNIT
COMPRESSORSt
FAN MOTORS*
Volts
MCA
MORA
(Fuse)
ICF
RLA (ea)
LRA (ea)
Total MTA
Total
Fans
(Ph)
FLA (ea)
Fan No.
MTA
(FCB)
Nameplate
Supplied*
Compressor No.
CB
h
O.
Min
Max
1
2
1
2
1
2
1,2
3,4,5,6
208-230
187
254
342
500
846
119
158.5
506
690
166
222
6
(
1
)
4.6
7 7
35
060
460
414
508
155
225
415
53
73
253
345
73
90
6
(
1
)
2.3
3.3
18
575
518
632
128
125
335
45
59
176
276
63
82
6
(
1
)
1.8
2.6
14
NOTE: As shipped, all units are XL (across the line) start.
•Units are suitable for use on electrical systems where voltage
supplied to the unit terminals is not below or above the listed
minimum and maximum limits.
f30GB060 has 2 compressors.
jaOGBOeO has one FOB for all fans.
GENERAL ELECTRICAL NOTES:
1 Unit listings are:
UL — Underwriters Laboratories: 30GB060
2. Electrical data based on unit conforming to ARl Standard 590,
Section 8.1.
Maximum Loading Conditions
(115 F ambient at
-
10
% voltage)
3. All units have single-location power connection to simplify field-
power wiring Main power must be supplied from a field-supplied
fused disconnect. Unit must be properly grounded.
4. Control circuit power must be supplied from a separate source
through a field-supplied fused disconnect. (See Note 9.)
5. Crankcase and cooler heaters are wired into the control circuit
so they are always operable as long as the control circuit power
supply disconnect is on, even if any safety device is open or the
unit CN/CFF switch is off.
6
. Heaters are wired ahead of the control circuit fuse; thus, they are
protected by the overcurrent protective device in the control
circuit power supply.
7. Cn all voltages, 30GB060 has one terminal block, with 3 con
ductors from the fused disconnect.
8
. Maximum incoming wire size for each terminal block is 500 MCM.
9. Amperage required for control circuit is as follows:
UNIT
30GB
POWER
SUPPLY
CONTROL
CIRCUIT
Power
Amps
208/230-3-60
115-1-60
15
060
460-3-60
115-1-60
15
575-3-60
115-1-60
15
10. Power draw of control circuits includes both crankcase heaters
and cooler heaters Each compressor has a crankcase heater
that draws
200
watts of power
Cooler heaters: 060 - 360 watts — band heaters (360 watts total).
Controls
Microprocessor — Microprocessor controls overall
unit operation. Its central executive routine controls a
number of processes simultaneously. These include
internal timers, reading inputs, A to D conversions, fan
control, display control, diagnostic control, output relay
control, demand limit, capacity control, head pressure
control and temperature reset. Some processes are
updated almost continuously, others every 2 to 3 seconds,
and some every 30 seconds.
The microprocessor routine is started by switching
control circuit ON-OFF circuit breaker switch to ON.
(This switch is also used to reset microprocessor should
any safety trip and also functions as circuit breaker for
electronic processor and relay boards.)
When the switch is closed, a 2-minute initialization
routine is begun. During this time, inputs are checked,
EXV and internal constants are initialized and a 20
appears on display. If display button is pushed during this
period, control goes into a 42-step Quick Test routine,
normally used for a readiness check during start-up, or
for service.
Microprocessor controls capacity of chiller by cycling
compressors and unloaders on and off at a rate to satisfy
actual dynamic load conditions. Control will maintain
leaving water temperature set with dial on display board
through intelligent cycling of compressors. Accuracy will
depend on loop volume, loop flow rate, load, outside air
temperature, number of stages, and particular stage
being cycled off. No adjustment for cooling range or
cooler flow rate is required, because the control auto
matically compensates for cooling range by measuring
both return water temperature and leaving water
temperature. This is referred to as leaving water tem
perature control with return water temperature
compensation.
The basic logic for determining when to add or remove
a stage is a time band integration of deviation from set
point plus rate of change of leaving water temperature.
When leaving water temperature is close to set point and
slowly moving closer, logic prevents addition of another
stage. If leaving water temperature is less than 35 F
(1.7 C) for water, or 6°F (21°C) below the set point for
brine units, the unit is shut off until the water tempera
ture goes 6°F (3.3°C) above the set point, to protect
against freezing.
If l°F/minute (0.6°C/minute) pulldown control has
been selected (factory setting), no additional steps of
capacity will be added as long as difference between
leaving water temperature and set point is greater than
4°F (2.2°C) and rate of change in leaving water tempera
ture is less than l°F/minute (0.6°C/minute).
If it has been less than 90 seconds since the last capacity
change, compressors will continue to run unless a safety
trips. This prevents rapid cycling and also helps return oil
during short on periods.
Where available (requires accessory unloaders on some
units), 2 sequences are used to obtain circuit lead-lag
operation, which evens out compressor operating hours.
First, as unit turns on, microprocessor functioning as a
random number generator, determines which circuit will
start first. Also, when decreasing from maximum stage,
control will again randomly select which circuit to run
longest.
The control also performs other special functions
when turning on or off. When a circuit is to be turned off,
EXV is closed first and compressor is run for an additional
10 seconds to pump out refrigerant that was in the cooler.
Again, at start-up, if compressor hasn’t run in the last
15 minutes, EXV is held closed for 10 seconds while
11