Start-up, Unit controls and safety devices – Carrier 50WQ User Manual
Page 4
Attention! The text in this document has been recognized automatically. To view the original document, you can use the "Original mode".
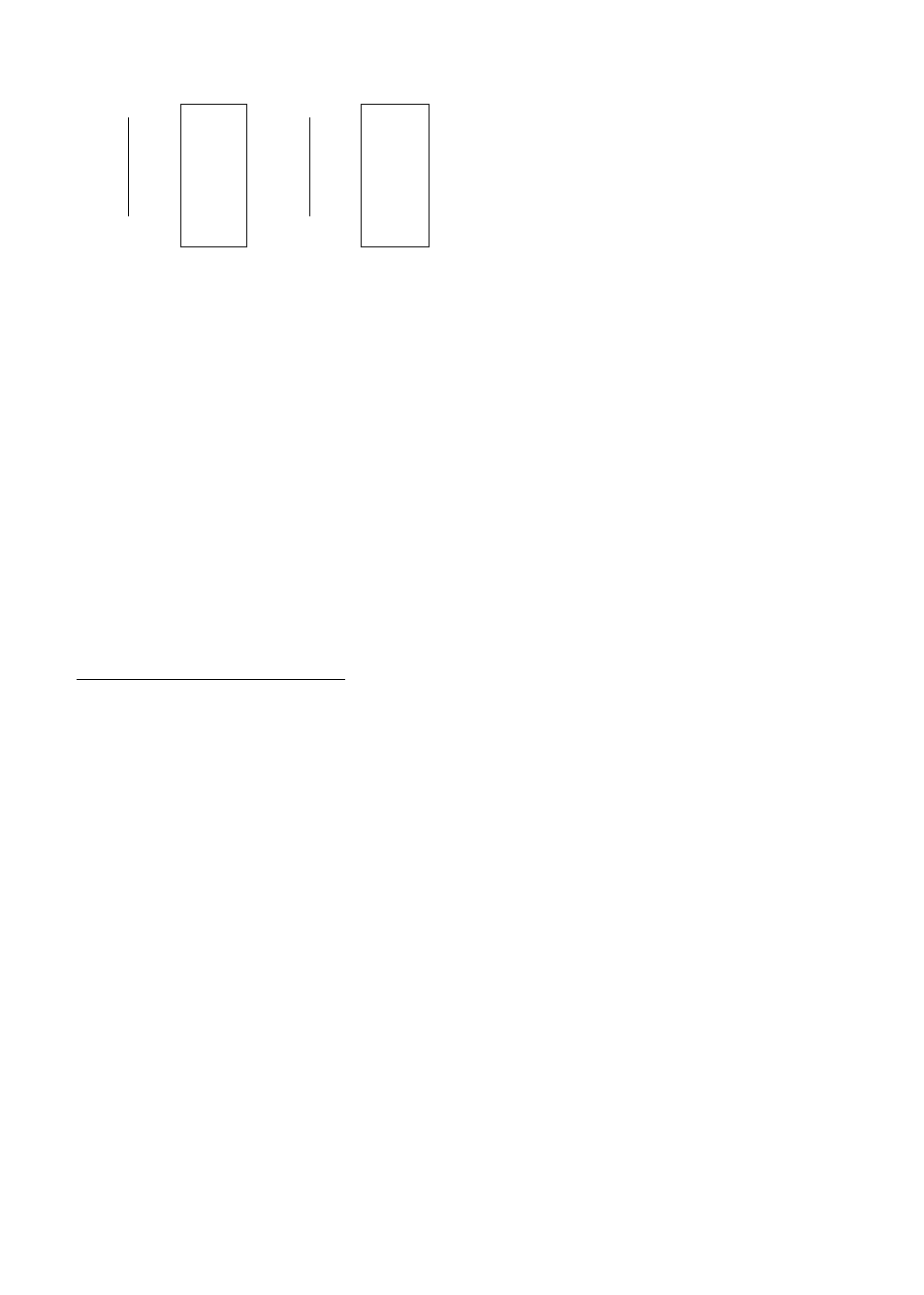
M
_____
—^YEL —
_____
—^YEL —
1-PHASE
CONN TO
DISCONNECT-
PER NEC
GROUND
LEAD
—^BLK —
,__^GROUND
—Hä] LUG
3-PHASE
CONN. TO
DISCONNECT-
PER NEC
---- - _
^^YEL-
^^YEL-
GROUND
LEAD
,__^GROUND
—C
ö
J
lug
50WQ
HEAT PUMP
CONTROL BOX
50WQ
HEAT PUMP
CONTROL BOX
I-PHASE
3-PHASE
Fig. 3 — Line Power Connections
SET FAN MOTOR SPEED — All units are factory
wired for high fan speed operation. Set fan motor
for medium or low speed operation as follows:
1. Remove unit fan section access panel.
2. Locate Molex fan speed selector block on fan
housing, Fig. 5. Selector block receptacle 1 is
high fan speed, receptacle 2 is medium fan speed
and receptacle 3 is low fan speed. Yellow and
black fan motor power leads from control box
are connected to selector block receptacle C and
1. Yellow lead is common, black lead is speed-
change lead.
3. Change fan motor speed by removing black lead
from selector block receptacle 1 and plugging it
into receptacle 2 or 3. Receptacle 4 is not used.
CAUTiONt For proper rniit operaiioit, set unit
fast inoitor ;^>eed ibr air tjuantity
m tìàa
range
&ÌK>wn in Tabie
4,
Set fan motor speed on 460-volt units — Two-speed
fan motor is factory wired for high-speed operation.
(Yellow and black power leads from control box are
connected to the yellow and black fan motor leads.)
Change fan motor to low speed by wiring as follows:
1. Splice the violet and black fan motor leads
together.
2. Splice yellow and black power leads from control
box to yellow and red motor leads. (Yellow-to-
yellow and black-to-red.)
CONNECT CONTROL POWER WIRING (24-v)
— Power leads are brought thru 1 / 2-in. hole pro
vided in unit. Fig. 1. Extend leads to low-voltage
terminal board located on top of control box. Fig. 5.
Connect leads to terminal board as shown in Fig. 3.
Use room thermostat HH01AD042 and thermo
stat subbase HH93AZ044 for proper unit operation.
Be sure that field-installed jumper wire is connected
between subbase terminals W and Y. Set thermo
stat heat anticipator at 0.45 amp for 1-phase units
and 0.50 amp for 3-phase units.
START-UP
Water Flow and Temperature Data
1. Consider design water flow rates for efficient
operation. See Table 4 for permissible water flow
range.
2. Ensure that water temperature entering unit is
between 45 F minimum and 90 F maximum. For
water temperature below 60 F, insulate supply
line and install a secondary drain pan under the
unit to remove condensate from heat exchanger
and internal plumbing.
CAUTION: Water teniperattJre otttside
specified temperature range may cause
damage to uiijt.
3. Ensure that supply water is clean and air is
purged from system. Air in supply water causes
scaling in heat exchanger. Foreign material in
water and/or excessive velocity of water can
cause damage to tubing.
4. When using a semi-closed system with an “open”
cooling tower, a water treatment system should
be operational with initial water flow.
To Start Unit
— Ensure that air filter is in place on
unit filter flanges provided. Do not operate unit
without filter in place. Adjust the thermostat as
follows:
1. Set selector switch at OFF.
2. Turn on main disconnect switch to unit.
3. Set fan switch as desired (ON or AUTO.).
4. Set thermostat dial at desired temperature.
5. Set selector switch at HEAT or COOL.
Check system refrigerant charge. See Refrigerant
Charging on page 6.
-^Unit
Single-Phase
Compressors
that
are
equipped with a compressor start thermistor (PTC
device) — When supply voltage is within limits
indicated on nameplate and compressor will not
start, check the thermistor with an ohmmeter.
If the PTC is good, and the compressor does not
start, disconnect the PTC from the starting circuit
and give unit a temporary capacitance boost. Refer
to Carrier Standard Service Techniques Manual,
Chapter 2, for details on capacitance boost pro
cedure. If unit does not start with capacitance boost,
compressor may be defective. If unit does not start,
check starting capability with PTC assistance. If
questionable, remove PTC, add start capacitor and
start relay per start kit installation instructions.
WARNINGc Caftaciiaace boosa or ijistaliatioa
of start capadtor and start shtutki be per^
fonued by irauted persoaaet improper pro-
cedrn» couici cause
tajtjry or equipoaeat
damage.
Unit Controls and Safety Devices
HIGH-PRESSURE RELIEF VALVE (except
50WQ0I4) is located in compressor. Relief valve
opens at a pressure differential of approximately
550 psi between suetion (low side) and discharge
(high side) to allow pressure equalization.