Every 2 months, Every 6 months, Every year – Carrier 16JA User Manual
Page 4
Attention! The text in this document has been recognized automatically. To view the original document, you can use the "Original mode".
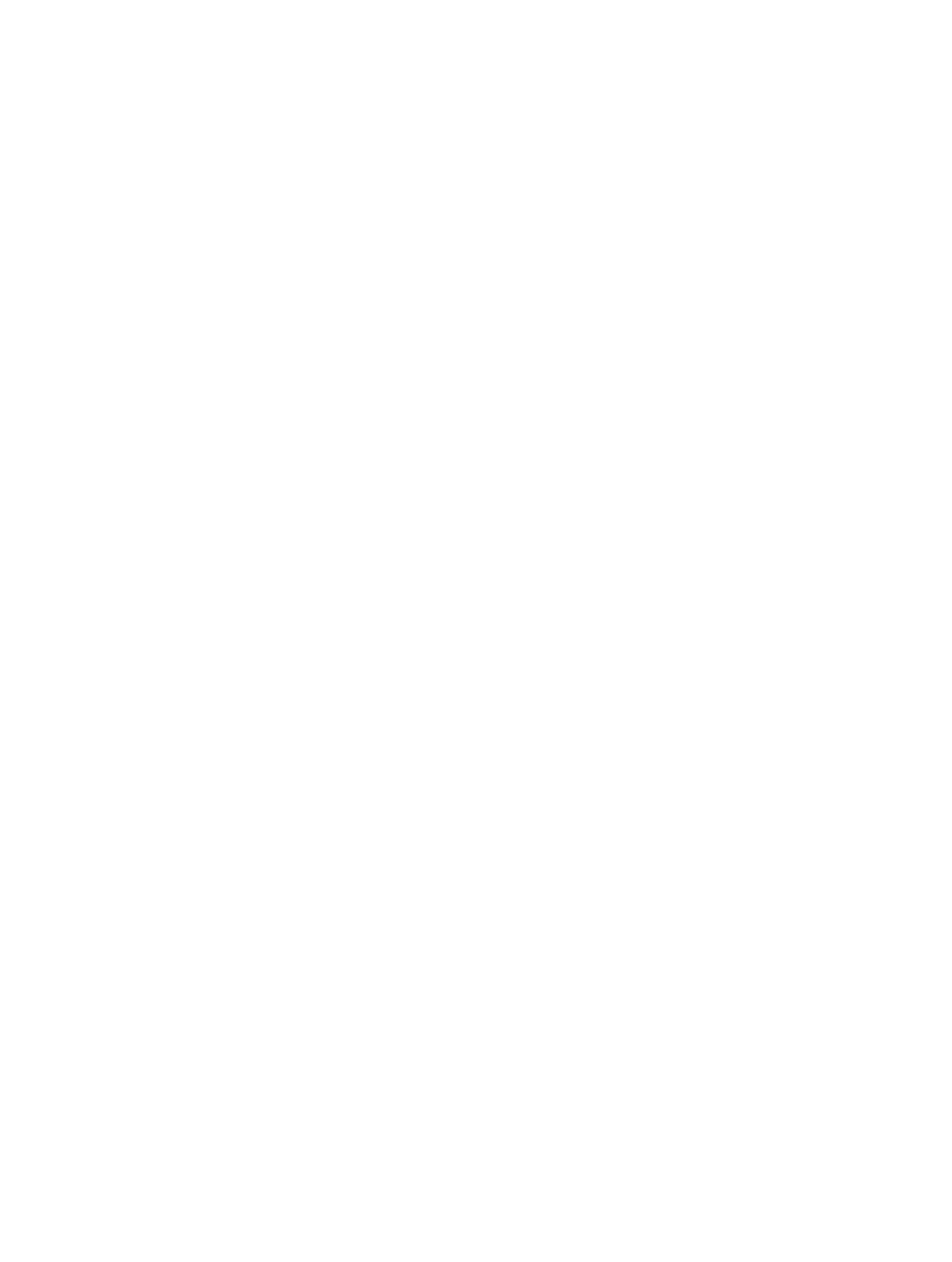
Check Machine Tightness
- The most important
maintenance item on the absorption machine is
maintaining vacuum tightness within acceptable
limits. Check machine tightness by determining
the noncondensable accumulation rate. Use pro
cedures given in Carrier Standard Service Tech
niques, publication SM-16.
EVERY 2 MONTHS
Check Dilution Thermostat
- The dilution thermo
stat should be open when the strong solution drops
to 140 F. If temperature cutout point is not 140 F,
insert screwdriver in slot on face of thermostat
(located on strong solution line) and turn adjust
ment dial until cutout occurs at 140 F.
Check Low-Temperature Cutout
- Remove low-
temperature cutout sensing element from sep
arable well in the evaporator shell. Place it in
an ice bath. Low-temperature cutout should trip
at 5 F below design leaving chilled water tem
perature or a minimum of 36 F. The actual cutout
point is the dial setting less 3 F differential. When
the control trips, the machine will shut down
immediately without going thru a dilution cycle.
NOTE: The chilled water pump will continue
to run if hooked up in the standard wiring
arrangement.
EVERY 6 MONTHS
Check Evaporator Water Charge
-Check the evap
orator water charge to determine if the reclaim
valve has energized. If valve has energized then
either tube leakage or excess refrigerant is
indicated.
Reclaim should start at full load (corresponds
to approximately 62 percent lithium bromide in
absorber for standard nominal conditions). Check
as follows:
1. Operate machine at full load with design en
tering condensing water and design leaving
chilled water.
2. Remove a sample of evaporator water from
refrigerant pump service valve and check the
specific gravity. If specific gravity is below
1.02 proceed with step 3. If specific gravity
is above 1.02 reclaim solution (see instruc
tions for Reclaim Solution, page 3) until specific
gravity is below this point, then proceed with
step 3.
3. Evaluate absorber loss. Should be 2 F or less.
If more, purge air from machine.
4. Check reclaim line by feel. Listen for refrig
erant flow (audible). If reclaim line is already
cold, with audible refrigerant flow, remove
refrigerant until reclaim valve closes (audible
click) and refrigerant flow ceases.
If machine is operating under light load, it will
be necessary to concentrate the absorber weak
solution to 62 percent. To do this, raise entering
condenser water temperature. Turn down control
point adjuster below design leaving chilled water
temperature setting. Repeat steps 1 thru 4.
Continual removal of water indicates leakage in
one of the tube bundles. Leak test by using proce
dures outlined in Carrier Standard Service Tech
niques, publication SM-16.
Check Capacity Control Valve
- Check to see if
leaving chilled water is being maintained at design
temperature. If not, adjust the electronic or
pneumatic control.
TO ADJUST ELECTRONIC CONTROL
1. Move control point adjuster clockwise to in
crease temperature, or counterclockwise to
decrease temperature. If this fails to bring
leaving chilled water within design temper
ature, perform step 2.
2. Replace vacuum tubes in control motor. Make
sure that new tubes are installed in correct
plugs. If this fails to bring leaving chilled
water
within
design
temperature,
proceed
with step 3,
3. Clean relay contacts with stiff paper. If this
fails to correct problem, contact Carrier
immediately.
TO ADJUST PNEUMATIC CONTROL
1. Reset control point setting to design.
2. If above fails to correct problem, contact
Carrier immediately.
Check Cooling Tower Bypass Control
- If control
is not maintaining design entering condensing
water temperature, recalibrate the control ther
mostat. For information, contact the valve (or
control) manufacturer.
EVERY YEAR
Check for Absorber and Condenser Scale
- Check
absorber and condenser tubes to see if cleaning
is required. Soft scale may be removed with tube
cleaning brushes. When hard scale has formed,
it may be necessary to chemically clean the tubes.
If a scale problem occurs, contact a water treat
ment representative. Annual tube cleaning may
not be required if adequate water treatment is
maintained.
Recharge Lithiunn Bromide
- Recharge lithium
bromide when the purge exhaust bottle becomes
filled.
PROCEDURES
1. Open the exhaust valve and allow solution to
be forced back into the purge,
2. Close the exhaust valve when the level nears
the end of the tube. Do not allow air to be
drawn into the tube.