Where buea ccmrseoi to cuudeuser cou, Caliridn: tm 3sgìc mit h Page 7: Addllloaai may cnuse units to, Rsikve ihru luiemal pmsmm mief
Page 7: Addllloaai may cnuse units to, Rsikve ihru luiemal pmsmm mief
Attention! The text in this document has been recognized automatically. To view the original document, you can use the "Original mode".
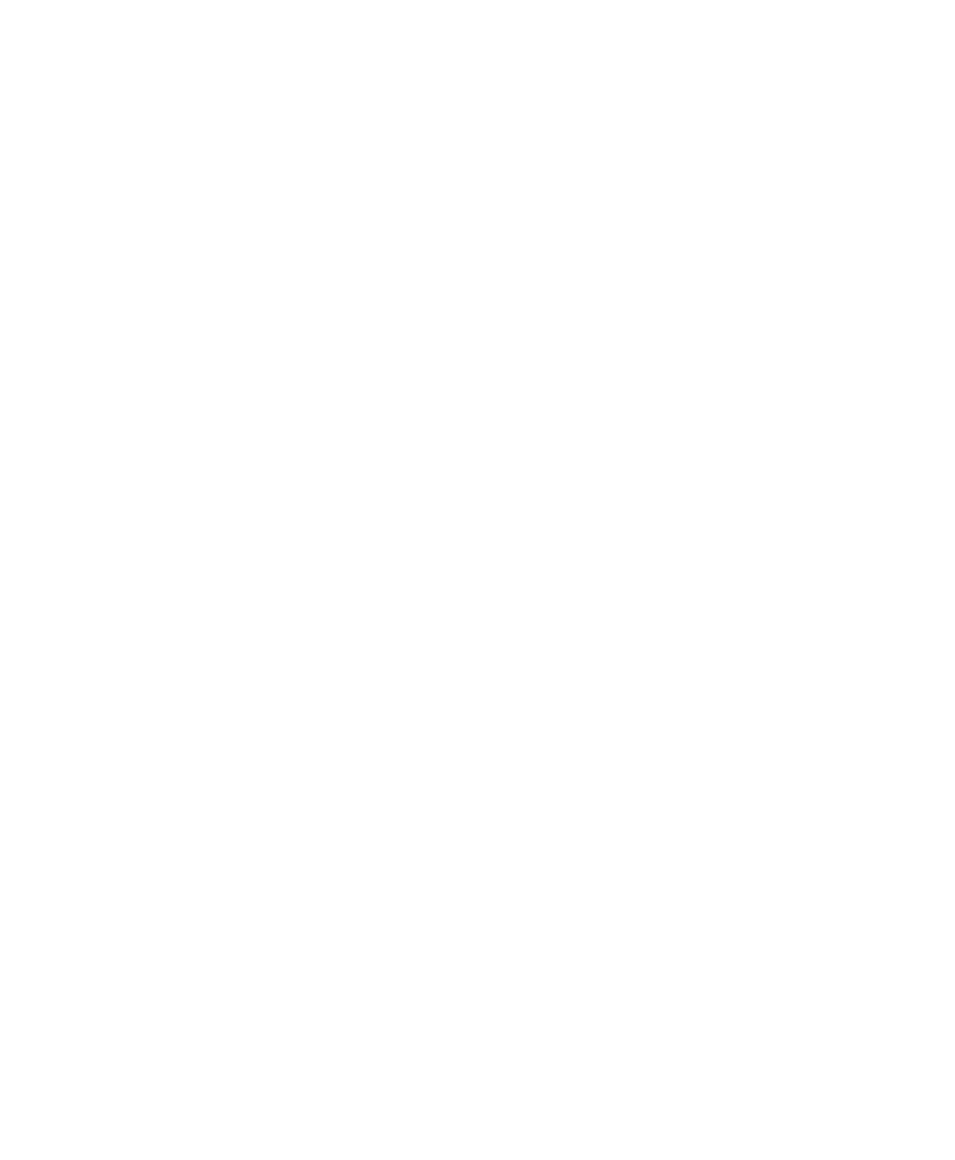
Compressor Protection
— Compressor motor is
protected by an internal current and temperature
sensitive overload. Excessive current or tempera
ture will cause overload to open, giving the
indication of an open circuit in the motor wind
ings. The overload will reset automatically when
internal motor temperatures drop to a safe level
(overloads may require up to 30 minutes to reset).
When an internal overload is suspected of being
open, check by using an ohmmeter or continuity
tester. See Carrier Standard Service Techniques
Manual, Chapter 2, for complete instructions.
Compressor Removal
— Follow safety codes, and
wear safety glasses and Work gloves. Have quench
ing cloth available (step 7).
CAUfiON; Atumiisii» iuMag Is used
ist
38GK
unic Do not overhaul
or
|>bce excessive
stralu ou tubiug
m
my result
1. Shut off power to unit. Remove unit rear
access panel.
2. Remove refrigerant from system using refrig
erant removal methods describing in Carrier
Standard Service Techniques Manual, Chapter 1.
3. Disconnect compressor wiring at compressor
terminal box.
4. Using a tubing cutter, cut suction and dis
charge (hot gas) lines at convenient place near
compressor for easy reassembly to new com
pressor with copper slip couplings.
CAliHON: Excmive movuuieut
ofmppot
Hues M
ceusu a. break
where buea ccmrseoi
to
cuudeuser coU>
5. Remove compressor hold-down bolts and lift
compressor out.
6. Remove mounting grommets on springs from
old compressor and install on new compressor.
7. Carefully unbraze suction and discharge line
piping stubs from old compressor. If oil vapor
in piping stubs ignites, use quenching cloth.
Braze piping stubs onto new compressor.
8. Install new compressor in unit. Braze suction
and discharge lines to compressor piping stubs
at points where cut (step 4), using field-
supplied copper couplings. Ensure that com
pressor hold-down bolts are in place. Connect
wiring.
9. Clean system. Add new liquid line filter-drier.
10. Evacuate and recharge unit.
Pumpdown Procedure
— The 38GK units may be
pumped down in order to make repairs on low side
of system without losing complete refrigerant
charge.
1. Attach pressure gag^ to suction service valve
gage port.
2. Frontseat the liquid line valve.
3. Start unit and run until suction pressure reaches
5 psig (see CAUTION).
4. Shut unit off and frontseat suction valve.
5. Vent remaining pressure to atmosphere.
CALiriDN: TM 3SGÌC
mit h
only lb«fory
amonat
of
Addllloaai
may cnuse units to
rsikve
iHru luiemal
pmsmm
MIef
vdvo
(mdieatesd by a sudden rise of sncilou
befcuo suction
resets
$
psig, if tÈk
ùcoiiUf
shut unit off itnsnodmto“
ly; firnniseat suction vulyo, nud vout
k
>~
mnluing i^ressnre to ntiunspbenj.
Cleaning Condenser Coil
— Clean by washing with
dry refrigerant, low-pressure water or steam. Direct
spray from inside out.
Lubrication
FAN MOTOR BEARINGS are prelubricated.
COMPRESSOR contains factory oil charge. If oil
must be added, see Carrier Standard Service Tech
niques Manual, Chapter 1, page 1-21 for instruc
tions. Use Carrier PP33-1, Texaco Capella B or
Suniso 3G oil.