Carrier 38GK User Manual
Page 3
Attention! The text in this document has been recognized automatically. To view the original document, you can use the "Original mode".
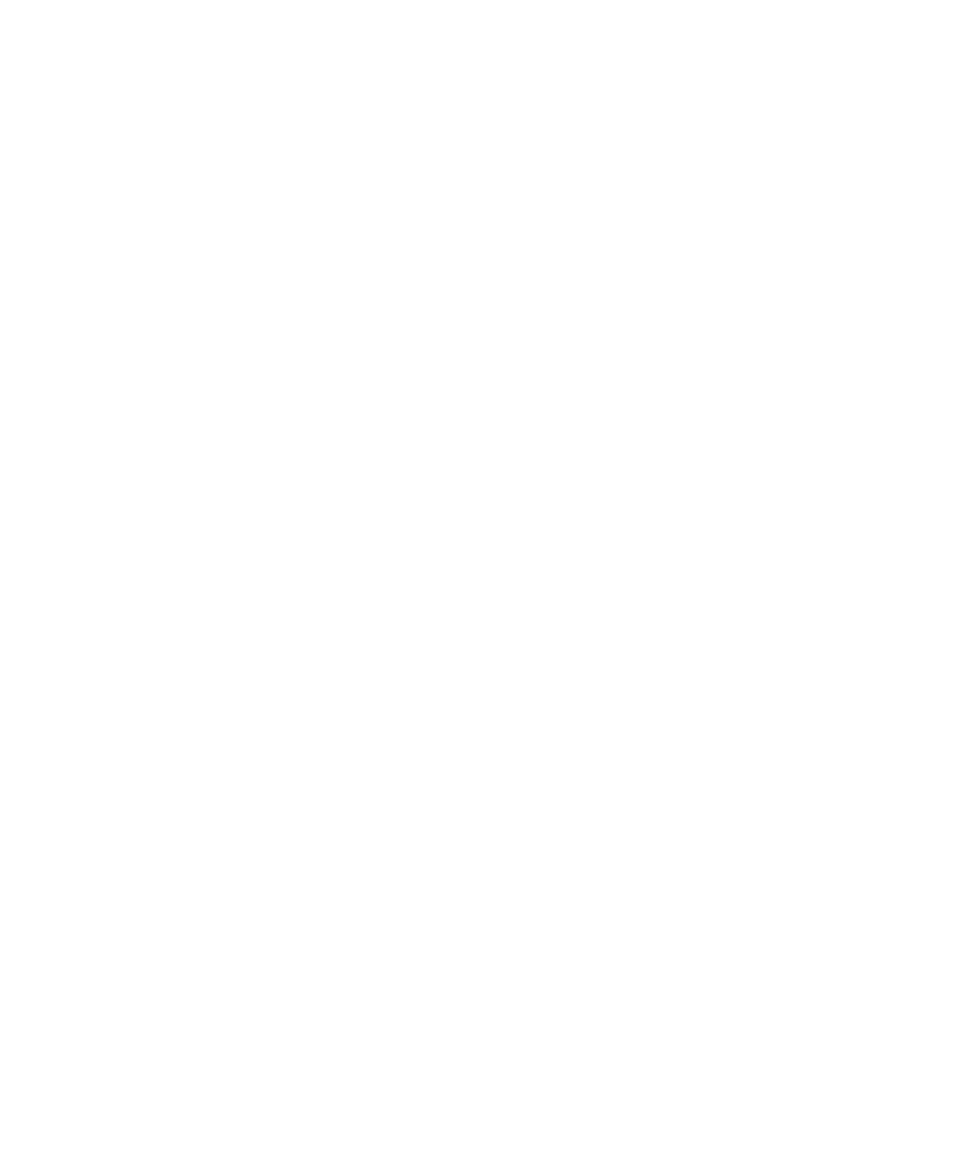
INSTALLING REFRIGERANT LINES
General
— The condensing unit is fully charged at
the factory. Be sure both service valves are front-
seated (turned clockwise) to avoid loss of the
charge. Do not remove refrigerant line connection
seals from the condensing unit, the matching coil,
nor the refrigerant tubing, until ready to make the
actual connection at the point of seal.
If accessory tubing package or evaporator coil
has been open for more than 15 seconds per
connection, evacuate or purge evaporator coil and
tubing system (use field-supplied refrigerant, not
unit refrigerant). Always evacuate or purge if
field-supplied tubing is used. See Purging.
Ensure field-supplied tubing is of refrigerant
grade. Insulate the suction line with insulation that
has an adequate vapor barrier (Armaflex or
Ensolex). Evacuate tubing.
When a complete Carrier system is used, a
filter-drier is not required. However, if other than
Carrier accessory tubing package or evaporator is
used, or if refrigerant tubing or coil is exposed to
atmospheric conditions for longer than 10 minutes,
install a filter-drier in the system near evaporator
coil. Additional refrigerant must be added to the
system to compensate for the additional volume of
the filter-drier.
Installation
1. Run refrigerant lines as directly as possible,
avoiding all unnecessary turns and bends.
2. Tape the liquid line to the top of the insulated
suction line for support.
3. Suspend the refrigerant lines so that they do
not damage the insulation on the suction line
and do not transmit vibration to the structure.
4. If the refrigerant lines are too long, the lines
should be rolled into a loop and placed in a
horizontal plane, or the excess may be cut off.
5.
Check to be sure both service valves are
frontseated (turned clockwise). It is necessary
to remove the valve stem caps to check.
6. Connect tubing to the condensing unit. The
refrigerant tubing and evaporator coil should be
leak tested upon completion.
Connection Procedure
— When making piping
connections, be sure to provide clearance at unit
for electrical connections.
Connect refrigerant liquid and suction lines to
condensing unit. Fig. 1 (page 1). Unit Compatible
Fittings permit 2 methods of refrigerant line
connection: mechanical (quick connect) or sweat
connection. Make suction line connection first.
MECHANICAL CONNECTION (Mate one set of
connections at a time.)
1. Loosen nut on Compatible Fitting one turn. Do
not remove.
2. Remove plug and be sure 0-ring is in the groove
inside the Compatible Fitting.
3. Cut tubing to correct length.
4.
Insert tube into Compatible Fitting until it
bottoms. Be sure tube is bottomed while nut is
being tightened.
5. Tighten nut until it bottoms on back coupling
flange.
SWEAT CONNECTION (Use refrigerant grade
tubing.)
1.
Remove locking nut, rubber 0-ring and
Schrader core from valve.
2. Cut tubing to correct length.
3. Insert tube into Compatible Fitting. Wrap top
and bottom of service valves in wet cloth to
prevent damage by heat. Solder with low-
temperature (450 F) silver alloy solder.
4. Replace Schrader core.
5. Evacuate or purge system with field-supplied
refrigerant.
Leak Testing
No installation is complete until all field and
factory joints have been checked for leaks.
1. Remove the valve stem caps from both service
valves and check to be sure the valves are
frontseated (turned clockwise). Remove the
service port caps.
2. Attach a gage manifold to service ports of the
service valves and purge the hoses.
3. Pressurize the evaporator coil and the inter
connecting refrigerant tubing with vapor from
an external refrigerant cylinder of R-22 until
the system and cylinder pressures are equalized.
NOTE: NEVER USE A UNIT CHARGE FOR
LEAK TESTING.
4. Leak test with an electronic detector, a halide
torch, or a liquid soap solution.
5. Release the pressure and repair any leaks found.
6. If the system is to be purged or evacuated, leave
the service valves in the frontseated position.
7. If the system is free of leaks, you may then
prepare the unit for operation by:
a. Backseating (turn counterclockwise) both
service valves.
b. Removing the gage manifold.
c. Replacing the caps on the service port and
valve stem.
Purging
— To purge unit, do not use the unit
charge Proceed as follows:
1. Remove the valve stem caps from both service
valves and check the valve stems to be sure they
are frontseated (clockwise).
2. Remove the service port caps from both service
valves and connect a refrigerant cylinder of
R-22 to the service port of the liquid line
service valve.
3. Open the refrigerant cylinder valve and allow
approximately 1/2 to 1 pound of refrigerant to
flow thru the system and out the service port
on the suction line service valve.