Wilkerson R28 User Manual
Safety guide, Warning
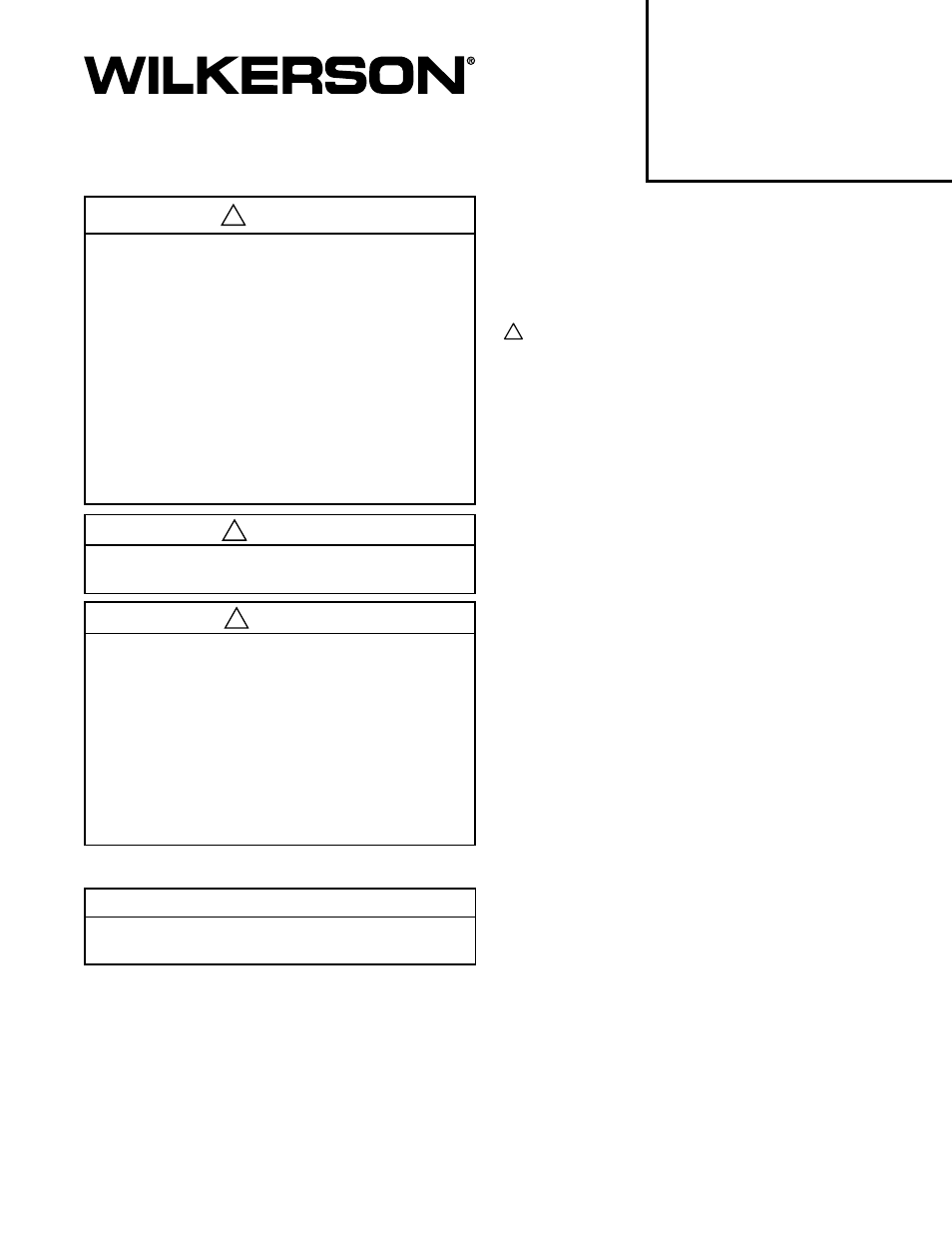
7. To increase regulated pressure, pull adjusting knob up and turn clockwise. To
reduce pressure, turn knob counterclockwise. To lock the knob, push the knob
down.
8. To panel mount this unit the following applies:
— Model R18/R19: Panel clearance hole diameter = 1.94" (49,3 mm).
— Model R18/R19: Panel thickness 3/16" (4,8 mm).
— Model R28: Panel clearance hole diameter = 2.44" (61,9 mm).
— Model R28: Panel thickness 3/16" (4,8 mm).
MAINTENANCE
DEPRESSURIZE SYSTEM BEFORE ATTEMPTING SERVICE!
THIS UNIT MAY BE SERVICED WITHOUT REMOVING THE UNIT FROM THE
COMPRESSED AIR LINE.
NOTE: The R28 and R28A (Series A) have different internal parts and require the
use of different repair kits. The R28A is the most current design and production
began in December 1997. For identification purposes, the Bonnet of the R28 has
“28A” permanently marked in two places on the shoulder above the panel nut
threads. Also internally the body has raised characters “28A”. Once the diaphragm
is removed, this can be seen. Parts from R28 and R28A regulators are NOT
interchangeable. You can NOT use R28 regulator parts in R28A regulators; nor can
you use R28A parts in R28 regulators. When repairing the R28 and the R28A
regulators, make your identification by looking for the identifying “28A” mark on the
bonnet, and then select the repair part numbers accordingly from the parts listed in
this sheet. If you are unsure of which regulator you have, contact your local
Wilkerson distributor or call Wilkerson.
1. Servicing depends largely on the condition of the compressed air system and
the degree of contamination in the system. Service unit at minimum every six
months.
2. Before attempting to service this product on-line, depressurize both the
upstream and downstream sides of the regulator and turn the adjusting knob
counter-clockwise to remove all spring force.
3. Remove the bottom plug, valve spring and valve assembly. Inspect all seals
and components for damage and replace as required. Clean seals and
components with mild detergent and water (no solvents!). Use a clean, dry
cloth to wipe any contamination from valve seat inside the body. Lubricate the
valve stem and lower valve O-ring seal with a light coat of Parker O-Lube™
lubricant or equivalent. Reassemble unit. Torque Bottom Plug to value shown
in table.
4. To replace main spring or diaphragm, turn adjusting knob counter-clockwise to
remove all spring force, then remove bonnet by turning counter-clockwise
(viewed above). Remove the adjusting screw assembly, main spring, slip ring
and diaphragm assembly. Inspect the diaphragm and the relief seat on
relieving models, for damage and contamination. Replace diaphragm
assembly if necessary. Clean the relief seat with a soft, dry cloth. Reassemble
in the reverse order, making sure the slip ring is properly positioned on top of
the diaphragm. Bonnet torque specifications are listed in the table.
5. Before returning unit to service, insure that all seals have been properly
reinstalled or replaced, and components requiring torque have been properly
tightened.
ACCESSORIES
Joiner set ........................................................................................ GPA-96-601
T-Bracket ......................................................................................... GPA-96-602
T-Bracket with Joiner set ................................................................ GPA-96-603
L-Bracket (R18) .............................................................................. GPA-96-606
L-Bracket (R28) .............................................................................. GPA-96-607
Pressure Gauges:
0-30 PSI ..................................................................................... K4515N14030
0-60 PSI ..................................................................................... K4515N14060
0-160 PSI ................................................................................... K4515N14160
0-300 PSI ................................................................................... K4515N14300
0-2,0 bar ..................................................................................... K4515G14030
0-4,2 bar ..................................................................................... K4515G14060
0-11,2 bar ................................................................................... K4515G14160
0-21 bar ...................................................................................... K4515G14290
TROUBLE-SHOOTING LEAKS
1. If regulated pressure begins to creep, (an uncontrolled rise in regulated
pressure) it will most likely be caused by contamination on the valve seat.
Refer to maintenance step #3 to remedy the condition.
2. If the unit leaks from the vent holes in the bonnet, it may be caused by
contamination, deterioration or damage to the diaphragm relief seat or
diaphragm itself. Refer to maintenance steps #3 and #4 to remedy the
condition. Replace any damaged or worn components.
Installation & Service Instructions
84-011-000
Regulator Models R18, R28,
R28A and R19
ISSUED: September, 2006
Supersedes: April, 2006
Doc.# 84011000, ECN# 060870, Rev. 5
Richland, MI 49083
Tel: (269) 629-5000
WARNING
To avoid unpredictable system behavior that can cause personal injury
and property damage:
•
Disconnect electrical supply (when necessary) before installation,
servicing, or conversion.
•
Disconnect air supply and depressurize all air lines connected to
this product before installation, servicing, or conversion.
•
Operate within the manufacturer’s specified pressure, temperature,
and other conditions listed in these instructions.
•
Medium must be moisture-free if ambient temperature is below
freezing.
•
Service according to procedures listed in these instructions.
•
Installation, service, and conversion of these products must be
performed by knowledgeable personnel who understand how
pneumatic products are to be applied.
•
After installation, servicing, or conversion, air and electrical supplies
(when necessary) should be connected and the product tested for
proper function and leakage. If audible leakage is present, or the
product does not operate properly, do not put into use.
•
Warnings and specifications on the product should not be covered
by paint, etc. If masking is not possible, contact your local
representative for replacement labels.
!
!
INSTALLATION
1. Refer to WARNING prior to installation.
2. Install as close to the point of use as possible. It is advisable to install a
particulate filter on the inlet side of this product to extend the unit’s service life
and to minimize the frequency between necessary maintenance periods.
3. Units must be installed with the flow in the direction of the flow arrow. The
adjusting knob may be orientated in any position relative to the pipe.
4. This product is supplied with two auxiliary ports located on the front and rear
faces of the body. These ports may be used as additional regulated ports or for
pressure gauges. A pipe plug is supplied to block the unused port. Make sure
pipe plug is sealed before installation.
5. Avoid using reducing bushings, couplings, etc., whenever possible to install
this product. These devices restrict air flow and can affect performance.
6. Maximum pressure rating is 300 psig (21 bar). Temperature range is 32°F to
150°F (0°C to 65,5°C).
Safety Guide
For more complete information on recommended application guidelines, see the
Safety Guide section of Pneumatic Division catalogs or you can download the
Pneumatic Division Safety Guide at: www.wilkersoncorp.com
!
WARNING
Product rupture can cause serious injury.
Do not connect regulator to bottled gas.
Do not exceed maximum primary pressure rating.
WARNING
FAILURE OR IMPROPER SELECTION OR IMPROPER USE OF THE
PRODUCTS AND/OR SYSTEMS DESCRIBED HEREIN OR RELATED
ITEMS CAN CAUSE DEATH, PERSONAL INJURY AND PROPERTY
DAMAGE.
This document and other information from The Company, its subsidiaries and
authorized distributors provide product and/or system options for further
investigation by users having technical expertise. It is important that you
analyze all aspects of your application, including consequences of any failure
and review the information concerning the product or systems in the current
product catalog. Due to the variety of operating conditions and applications
for these products or systems, the user, through its own analysis and testing,
is solely responsible for making the final selection of the products and systems
and assuring that all performance, safety and warning requirements of the
application are met.
The products described herein, including without limitation, product features,
specifications, designs, availability and pricing, are subject to change by The
Company and its subsidiaries at any time without notice.
EXTRA COPIES OF THESE INSTRUCTIONS ARE AVAILABLE FOR INCLUSION
IN EQUIPMENT / MAINTENANCE MANUALS THAT UTILIZE THESE PRODUCTS.
CONTACT YOUR LOCAL REPRESENTATIVE.
!