Drive maintenance and installation, Motor change-out and jib crane, Troubleshooting guidelines – Twin City Inline Fume Exhaust Fans - IM-1080 User Manual
Page 6: Troubleshooting performance problems
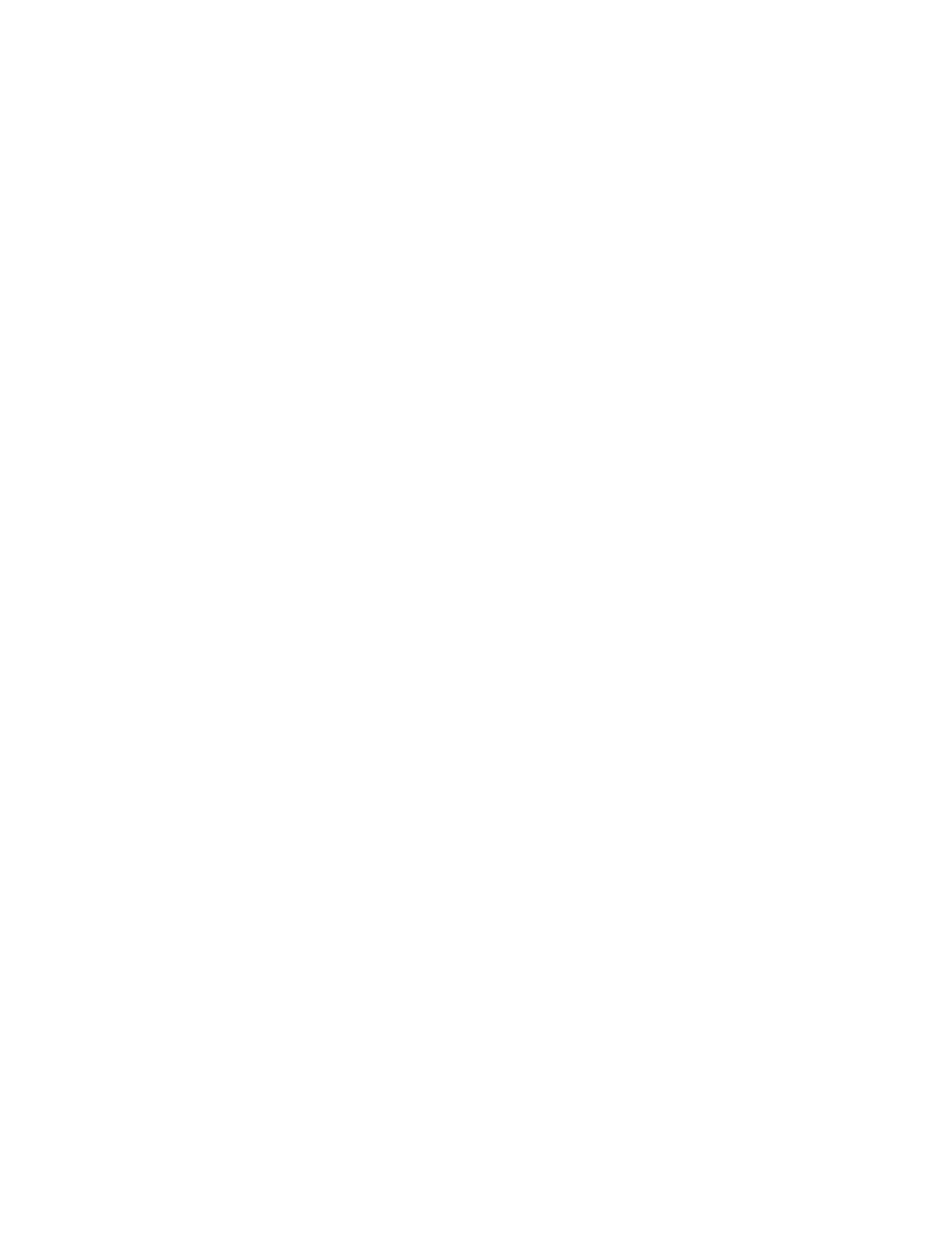
6
Twin City Fan IM-1080
DRIVE MAINTENANCE AND INSTALLATION
V-belt drives need periodic inspection, retensioning, and
occasional belt replacement. When inspecting drives, look
for dirt buildup, burrs or obstructions that can cause pre-
mature belt or drive replacement. If burrs are found, use
fine emery cloth or a stone to remove them. Be careful
that dust does not enter the bearings. Check sheaves for
wear. Excessive slippage of belts on sheaves can cause
wear and vibration. Replace worn sheaves with new
ones. Carefully align sheaves to avoid premature sheave
failure. Inspect the belts for wear. If fraying or other wear
is observed to be mostly on one side of the belts, the
drives may be misaligned. Reinstall the drives according
to the following instructions:
1. Slip (do not pound) proper sheave onto correspond-
ing shaft. CAUTION: Placing fan sheave on motor can
overspeed wheel and cause structural failure.
2. Align sheaves with straightedge extended along
sheaves, just making contact in two places on outside
perimeters of both sheaves.
3. Tighten sheave bolts (or setscrews if appropriate).
Table 1 can be used to determine the amount of
torque required.
4. Install a matched set of belts. Adjust the motor posi-
tion to obtain slack, install, and tighten belts. Using a
pry bar will damage belts.
5. Tighten belts to proper belt tension. Ideal tension is
just enough so that the belts do not slip under peak
load. When using drive tensioning data supplied by V-
belt drive manufacturers, new belts can be tensioned
to a value 50% greater than for normal operation. This
will reduce retensioning requirements after break-in.
Recheck sheave alignment after tensioning.
6. After initial installation of belts, recheck belt tension
again after a few days. (New belts require a break-in
period of operation.)
7. When replacing belts, replace the entire set. After ini-
tial replacement and tensioning, recheck belt tension
after a few days. (New belts require a break-in period
of operation.) Never use belt dressing on any belts.
8. Fans that have motors and drives mounted at the fac-
tory are trim balanced prior to shipment. This is not
possible on units that are shipped without motors and
drives. The addition of drive components in the field
can create unbalance forces. Twin City Fan & Blower
recommends final balancing of the unit after the drive
components are installed. Failure to do so may void
the warranty.
MOTOR CHANGE-OUT AND JIB CRANE
Motor Change-Out Procedure (Direct Drive Fans)
Twin City Fan Model TVIFE is available with a portable
jib crane option for use in removing the motor. The jib
crane mounts directly to a fabricated base that is built
into the mixing plenum box. When using a jib crane ver-
ify that it is not being used to lift loads that are greater
than its design capacity.
To remove the motor:
Attach the jib crane to the mounting bracket on the mix-
ing plenum box, verify that all attachments are properly
tightened and that there are no cracks and no damage
on the crane or mounting bracket.
Position the jib crane above the windband of the fan
and rig the crane cable to the lifting brackets on the
windband itself. Wind in cable until all lines are taught.
Remove all bolts securing the windband to the fan as-
sembly itself. Lift the windband off of the fan assembly
and lower it to the roof top.
Warning: be aware of your surroundings as fan compo-
nents can be heavy.
Position the jib crane above the fan housing and again
rig the crane cable to the lifting brackets on the fan
housing and tighten the cable. Remove all bolts holding
the fan housing to mounting bracket on the mixing box
or curb cap. Lift the fan housing and lower it to the
roof top. Loosen and remove wheel from motor shaft.
Loosen and remove bolts holding motor to fan housing
and remove motor.
Install new motor
Attach motor to fan housing, make sure all bolts are
sufficiently tightened. Attach wheel to motor shaft and
tighten. Using jib crane, lift wheel and housing assembly
by mounting brackets back onto mixing box/curb cap.
Carefully lower housing assembly onto box. Verify wheel
and funnel are overlapping correctly. Bolt housing as-
sembly to mixing plenum box/curb cap. Lift windband
by lifting lugs and align with bolt holes on top of fan
assembly. Bolt windband to fan assembly.
TROUBLESHOOTING GUIDELINES
Use current safety practices when investigating fan or
system performance problems. General safe practices and
performance troubleshooting guidelines can be found in
AMCA Publications 410 and 202, respectively. Fan appli-
cation and field measurement procedures can be found in
AMCA Publications 201 and 203.
TROUBLESHOOTING PERFORMANCE
PROBLEMS
The lists below indicate possible areas to check when
air or sound values do not match expectations. Most fan
problems can be pinpointed to one of these common
causes.
Air Capacity Problems:
1. Resistance of system not at design rating. If resistance
is lower than expected, both airflow and horsepower
may be up. If resistance is higher than anticipated, air
volume will be down.
2. Fan speed is not at design speed.
3. Air density not at design values. Also check air perfor-
mance measurement techniques/procedures.
4. Devices for air modulation are closed or plugged. Also
check filters.
5. Wheel mounted improperly or is rotating in reverse.
6. Parts of system or fan have been damaged or need
cleaning.
Noise Problems:
1. Air performance is incorrect and fan is not at design
point of operation. Fan forced to operate in an unstable
flow region.
2. Bearing failure. Check bearings (lubrication).
3. Supply voltage high or inconsistent supply frequency.
Adjustable frequency controllers can generate motor
noise.
4. Objects which are installed in a high velocity airstream
can generate noise. This includes flow sensors, turning
vanes, etc.
5. Poor fan inlet conditions.
6. Acoustics or sound measurement procedure incorrect.