Fan maintenance, Motor maintenance, Bearing maintenance – Twin City Inline Fume Exhaust Fans - IM-1080 User Manual
Page 5: Operation checklist
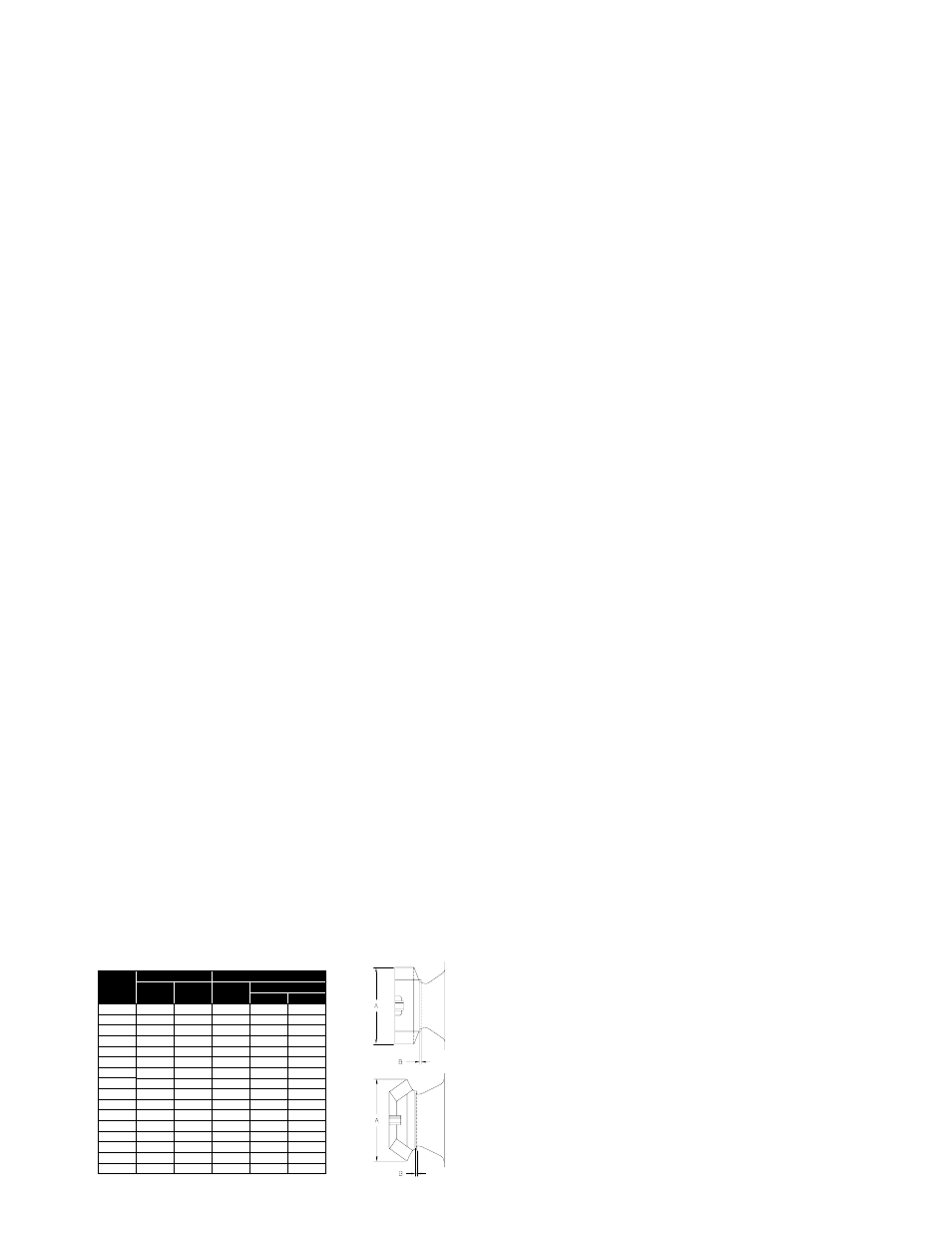
Twin City Fan IM-1080
5
FAN MAINTENANCE
Periodically inspect the shaft and wheel for dirt buildup,
corrosion, and signs of excess stress or fatigue. Clean
the components. If the wheel is removed for any reason,
make sure that it is securely attached to the shaft before
restarting the fan.
All structural components or devices used to support
or attach the fan to a structure should be checked at
regular intervals. Vibration isolators, bolts, foundations,
etc., are all subject to failure from corrosion, erosion,
and other causes. Improper mounting can lead to poor
operation characteristics or fan fatigue and failure. Check
metallic components for corrosion, cracks, or other signs
of stress. Concrete should be checked to insure the
structural integrity of the foundation. See curb installation
section for detail on proper mounting procedures.
MOTOR MAINTENANCE
The three basic rules of motor maintenance are:
1. Keep the motor clean.
2. Keep the motor dry.
3. Keep the motor properly lubricated.
Blow dust off periodically (with low pressure air) to pre-
vent motor from overheating. Some smaller motors are
lubricated for life. Lubrication requirements are normally
attached to the motor. Use the motor manufacturer’s
recommendations for relubrication. If this information is
not available, the following schedule may be used. Mo-
tors less than 10 HP running about eight hours a day in
a clean environment should be lubricated once every five
years; motors 15 to 40 HP, every three years. For motors
in dusty or dirty environments or running 24 hours a day:
divide the service interval by 4. Do not over lubricate.
BEARING MAINTENANCE
Proper lubrication of the fan drive bearings helps assure
maximum bearing life. All fans are equipped with decals
indicating relubrication intervals for normal operating con-
ditions. However, every installation is different and the
frequency of relubrication should be adjusted accord-
ingly. On high moisture applications, the lubrication fre-
quency may need to be doubled or tripled to adequately
protect the bearings. Double the relubrication frequency
on fans with vertical shafts. Observation of the conditions
of the grease expelled from the bearings at the time of
relubrication is the best guide as to whether regreasing
intervals and amount of grease added should be altered.
Greases are made with different bases. There are syn-
thetic base greases, lithium base, sodium base, etc.
Avoid mixing greases with different bases. They could be
incompatible and result in rapid deterioration or break-
down of the grease. The lubrication sticker identifies a
list of acceptable lubricants. All bearings are filled with
a lithium-based grease before leaving the factory. When
the fans are started, the bearings may discharge excess
grease through the seals for a short period of time. Do
not replace the initial discharge because leakage will
cease when the excess grease has worked out. Some-
times the bearings have a tendency to run hotter during
this period. There is no reason for alarm unless it lasts
over 48 hours or gets very hot (over 200°F). When re-
lubricating, use a sufficient amount of grease to purge
the seals. Rotate bearings by hand during relubrication.
OPERATION CHECKLIST
Verify that proper safety precautions have been followed:
□
Electrical power must be locked off
Check fan mechanism components:
□
System connections are properly made and tightened.
□
Bearings are properly lubricated.
□
Wheel, drives and fan surfaces are clean and free of
debris.
□
Rotate the impeller by hand to verify it has not
shifted in transit.
□
Check fan/wheel overlap. (See Figure 7.)
□
Drives on correct shafts (not reversed).
□
Check position of guards to prevent rubbing.
Check fan electrical components:
□
Motor is wired for proper supply voltage.
□
Motor was properly sized for power and rotational
inertia of rotating assembly.
□
Motor is properly grounded.
□
All leads are properly insulated.
Trial “bump”:
□
Turn on power just long enough to start assembly
rotating.
□
Check rotation for agreement with rotation arrow.
□
Does the assembly make any unusual noise?
□
Check drive alignment and tension. Does this meet
with drive manufacturer’s recommendations?
□
Correct any problems which may have been found.
(Follow safety guidelines - shut power off.) Perform
checklist again until unit is operating properly.
□
Run unit up to speed.
Verify fastener tightness. These may have loosened
during shipment or installation.
□
Setscrews attaching wheel hub to shaft.
□
Setscrews in drive sheaves or coupling.
□
Nuts on inlet funnel.
□
Nuts and bolts holding motor.
□
Nuts holding housing frame to base and base to
ground.
□
Nuts on accessories including shaft seal, access
doors and pie-splits.
□
Bolts in taper-lock bushings.
□
Grease line connections.
After one week of operation, check all nuts, bolts and
setscrews and tighten if necessary.
Figure 7.
FAN
SIZE
TFE
QFE, QIFE, TVIFE
A
B
A
B
MIN.
MAX.
90
–
–
12.25
0.25
0.38
122
12.25
0.31
15.00
0.31
0.44
135
–
–
16.50
0.38
0.50
150
15.00
0.38
18.25
0.44
0.56
182
18.25
0.56
20.00
0.50
0.63
200
20.00
0.63
22.25
0.56
0.69
222
22.25
0.69
24.50
0.63
0.75
245
24.50
0.75
27.00
0.69
0.88
270
27.00
0.88
30.00
0.75
0.97
300
30.00
0.97
33.00
0.88
1.06
330
33.00
1.06
36.50
0.75
0.94
365
36.50
0.94
40.25
0.81
1.03
402
40.25
1.03
44.50
0.88
1.13
445
44.50
1.13
49.00
1.00
1.25
490
49.00
1.25
54.25
1.13
1.38
542
54.25
1.38
60.00
1.25
1.56