Drive mounting, Flexible couplings, Motor maintenance – Twin City Heavy Duty Centrifugal Fans - ES-995 User Manual
Page 4: Drive maintenance and installation
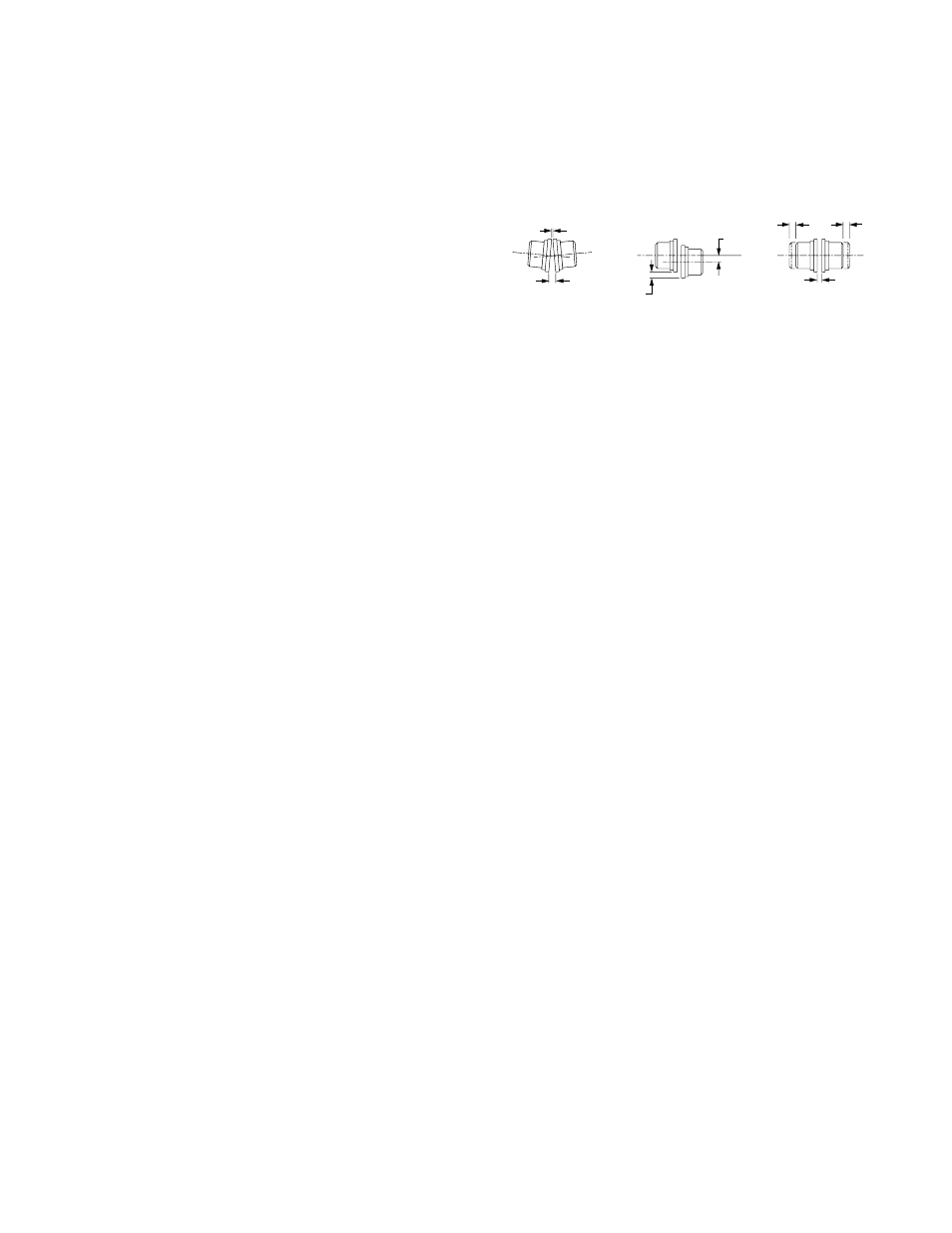
4
Twin City Engineering Supplement ES-995
are generally not interchangeable with parts from another
bearing.
2. The lower bearing housing should be bolted loosely to the
pedestal and seals; bearing and adapter sleeve housing
should be placed loosely on the shaft.
3. The rotor assembly with the seals and bearings should
next be positioned over the housings and carefully placed
into the lower housings.
4. The thrust locking ring should be installed in the bearing
closest to the drive sheave or coupling unless otherwise
noted in the drawing. The bearing race should be cen-
tered in the expansion bearing. The exception may be on
Arrangement 3 or 7 fans with a high operating tempera-
ture. Refer to the fan drawing for location.
5. When installing adapter sleeves, tighten for reduction in
clearance per manufacturer’s instructions.
6. Bend down a tab on the lockwasher after finishing adjust-
ment. If there is no lockwasher, tighten the setscrews
found on the locknut.
7. Grease or oil according to manufacturer’s instructions.
8. Install the bearing housing cap bolts and bearing mount-
ing bolts. Tighten bearing housing cap bolts and bearing
mounting bolts. Torque to bearing manufacturer's instruc-
tions.
Solid Pillow Block
1. Slide shaft in bearing bore to proper location.
NOTE: Shaft
should slide easily if self-aligning feature of the shaft is
within its limits. Sling the rotor assembly into place and
loosely bolt the bearings in place.
2. When bearings are in place, torque the base bolts using
values from Table 2 and tighten the collar setscrews to
manufacturer’s specification.
3. Grease or oil according to manufacturer’s instructions.
Drive Mounting
Mount drives as follows:
1. Slip (do not pound) proper sheave onto corresponding
shaft. To minimize bearing loading, mount sheaves as
close to bearings as possible.
CAUTION: Placing fan
sheave on motor can overspeed wheel and cause structural
failure.
2. Align sheaves with straightedge extended along sheaves,
just making contact in two places on outside perimeters
of both sheaves. This “four-point” alignment may also be
checked with a string tied to the shaft behind one of the
sheaves. The string is then pulled taut over the faces of
the sheaves to check the alignment at the four points at
the outside perimeters. Each sheave should be rotated
about one-half revolution during this check to look for
excessive runout or a bent shaft.
3. Install and tighten the belts. Run the drive for a few min-
utes to seat the belts. When tightening the belts, slide the
motor in to slip the belts on. Do not use a pry bar, as
this may damage the belt cords. Tighten the belts to the
proper tension. Ideal tension is just enough tension so that
the belts do not slip under peak load. Many drives are
provided with tensioning data which identifies the load to
apply at the center of the span and the allowable deflec-
tion from this force. This may be checked visually (look
for a slight bow on slack side), or listen for a squeal on
start up, indicating that the belts are too loose. Recheck
sheave alignment.
4. After initial installation of belts, recheck belt tension again
after a few days to adjust belt tension. (New belts require
a break-in period of operation.)
Flexible Couplings
These instructions are general for the installation of several
types of flexible couplings and should not be used as a sub-
stitute for more specific manufacturer’s instructions. The cou-
pling manufacturer’s installation data is available and will give
specific dimensions for alignment limits, lubricants, etc. Refer
to Item 7 in "Factory Assembled Units" section for coupling
alignment requirements.
Before preparing to mount the coupling, make sure that all
bearings, inlet vanes, shaft seals, or other components have
been installed on the shaft.
When mounting and keying the coupling halves to the
shaft, follow supplied instructions for heating and shrink fitting.
Set the coupling halves for the normal gap specified by the
manufacturer. Coupling gap is illustrated below.
The two types of misalignment are illustrated above. Typically
angular alignment is checked with feeler gauges between the hub
faces. When angular alignment has been adjusted to manufac-
turer’s specification by shimming, if necessary, parallel alignment
can be checked with a straightedge and feeler gauges on the
hub halves’ O.D. When shimming has brought parallel alignment
within specification, angular alignment and gap should again be
checked, and adjustments made if necessary. A dial indicator or
laser alignment may be used to more accurately take the mea-
surements described above.
Special adjustments may need to be made for couplings used
with some equipment. As an example, when used with motors
of over 300 HP, couplings may require provisions for limiting
end float. Larger drivers may grow in operation (due to heat
expansion) requiring the driver side to be set slightly low when
not operating. Refer to specific instruction manuals or assembly
drawings.
Thoroughly clean the coupling halves after completion of align-
ment. Reassemble the coupling and tighten bolts, washers and
locknuts. Lubricate per manufacturer’s recommendations.
Motor Maintenance
The three basic rules of motor maintenance are:
1. Keep the motor clean.
2. Keep the motor dry.
3. Keep the motor properly lubricated.
Blow dust off periodically (with low pressure air) to prevent
motor from overheating.
Some smaller motors are lubricated for life. Lubrication
requirements are normally attached to the motor. Use the motor
manufacturer’s recommendations for relubrication. Often motor
lubricants are not the same as the fan bearings. If this information
is not available, the following schedule may be used. Motors less
than 10 HP running about eight hours a day in a clean environ-
ment should be lubricated once every five years; motors 15 to 40
HP, every three years. For motors in dusty or dirty environments
or running 24 hours a day: divide the service interval by 4. Do
not over lubricate.
Drive Maintenance and Installation
V-belt drives need periodic inspection, retensioning, and occa-
sional belt replacement. When inspecting drives, look for dirt
buildup, burrs or obstructions that can cause premature belt or
drive replacement. If burrs are found, use fine emery cloth or a
stone to remove them. Be careful that dust does not enter the
bearings.
Check sheaves for wear. Excessive slippage of belts on
sheaves can cause wear and vibration. Replace worn sheaves
with new ones. Carefully align sheaves to avoid premature sheave
failure. If fraying or other wear is observed to be mostly on one
side of the belts, the drives may be misaligned. Realign and
Y
X
P
P
F
F
GAP
ANGULAR
PARALLEL
GAP AND
MISALIGNMENT
MISALIGNMENT
END FLOAT
X-Y = ANGULAR MISALIGNMENT
P = PARALLEL OFFSET (MISALIGNMENT)
F = END FLOAT