Caution, Warning – Reznor R6GN Option - Installation - LP Conv Kit User Manual
Page 4
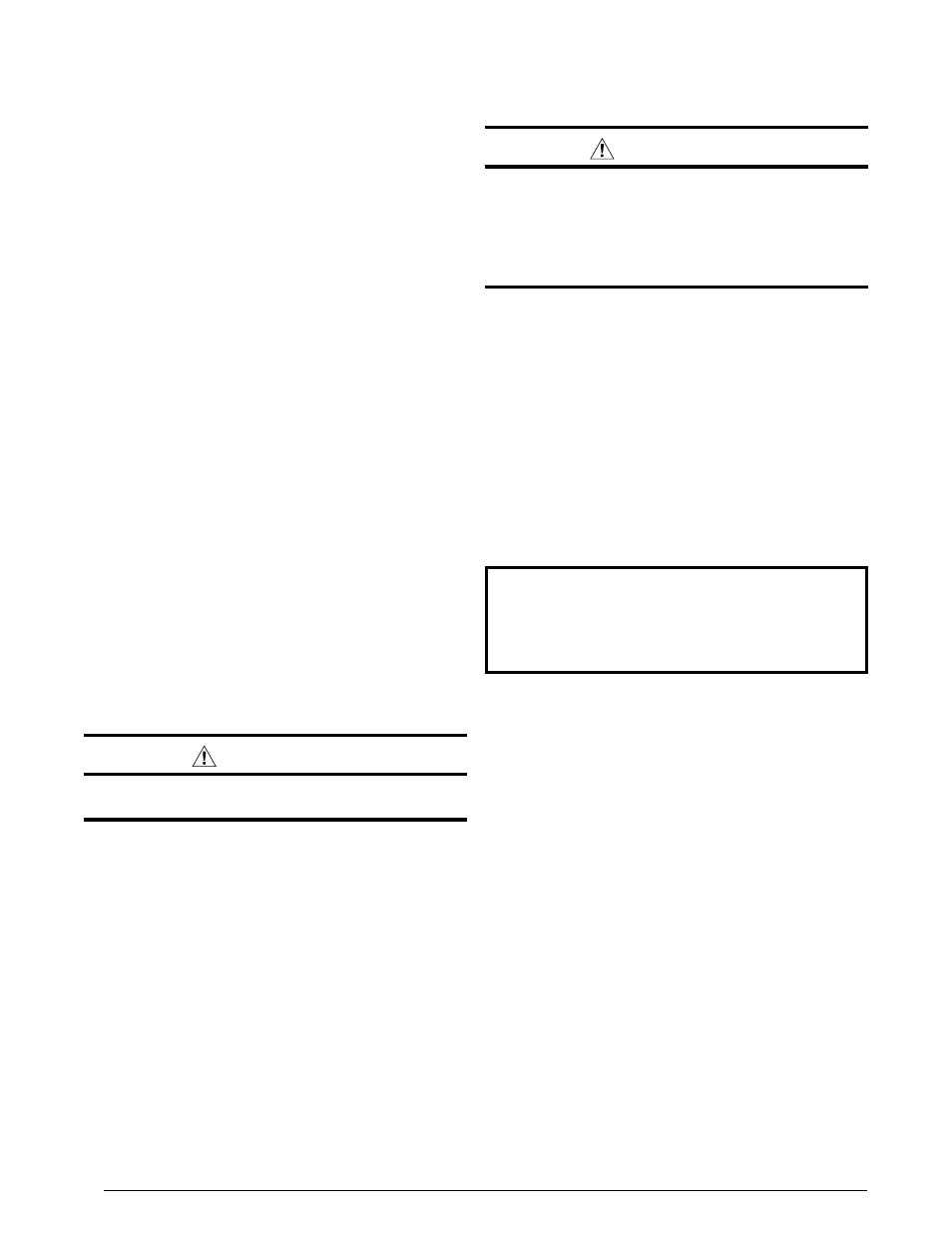
4
EXAMPLE 2:
• For a high fire flow rate of 68 cu. ft. gas per hour.
• Local heating value of LP gas (obtained from gas
supplier) = 2,500 Btu per cu. ft.
• Input rate = 2,500 x 68 = 170,000 Btuh.
LIGHTING & ADjUsTMENT OF
THE APPLIANCE
1. Turn ON the gas at the manual valve, outside of the unit.
2. Check all gas connections for leaks with a soap and water
solution. If the solution bubbles, there is a gas leak which
must be corrected.
DO NOT use an open flame to check
for gas leaks.
3. Turn ON the electrical power to the appliance.
4. Move the gas valve lever/switch/knob to the ON position. See
Figure 2 (page 5). NOTE: The lever/knob must be moved to
the end of its range of motion to insure the valve is completely
open. Use only your hand to push in or turn the gas control
valve. Never use tools.
5. Set the room thermostat to a point above room temperature
to begin the heating cycle of the unit.
6. Check that the unit ignites and operates properly. Refer to the
installation instructions provided with your unit for the normal
operating sequence.
7. After the flame ignites, visually inspect the burner assembly
to ensure that the flame is drawn directly into the center of the
heat exchanger tube. The end of the flame will be out of sight
around the bend of the heat exchanger tube. In a properly
adjusted burner assembly, the flame color should be blue
with some light yellow streaks near the outer portions of the
flame.
NOTE: Until all of the air is bled out of the gas line, the spark
ignitor may not ignite the gas. If the ignition control locks out, turn
the thermostat to its lowest setting and wait one minute then turn
the thermostat to a point above room temperature. The ignitor
will try again to ignite the main burners. This process may have
to be repeated several times before the burners will ignite. After
the burners are lit, check all gas connections for leaks again with
the soap and water solution. If the solution bubbles, there is a
gas leak which must be corrected. Do not use an open flame
to check for gas leaks.
VERIFYING & ADjUsTING FIRING RATE
The input firing rate must be verified for each installation to
prevent over-firing of the unit.
CAUTION:
Do not re-drill the burner orifices. If the orifice size
must be changed, use only new orifices.
ImPORTANT NOTe: The firing rate must not exceed the rate
shown on the unit data label. At altitudes above 2,000 ft., it
must not exceed that on the data label less 4% for each 1,000
ft. Follow the steps below to determine the unit firing rate:
• For installations at 2,000 feet and less, the firing rate
is the same as shown on the unit rating label.
• For installations above 2,000 feet, calculate the correct
firing rate as shown in Example 1.
• Table 2 (page 6) lists the correct orifice size to use at
different altitudes. See Example 1 to determine the unit
rating and orifice size.
• After changing the orifices, it is required that you
measure the gas input rate by clocking the gas meter
and using the local gas heating value. See Step 6 and
Example 2 below.
• Observe the action of the burners. Make sure there is
no yellowing, lifting or flashback of the flame.
WARNING:
The reduction of input rating necessary for high
altitude installation may only be accomplished with
factory supplied orifices. DO NOT attempt to drill out
orifices in the field. Improperly drilled orifices may
cause fire, explosion, carbon monoxide poisoning,
personal injury or death.
1. Obtain the gas heating value from the gas supplier (HHV).
2. Verify that the gas supply line is at the correct supply pressure
and that the supply pressure is within the allowable unit limits
listed on the unit rating plate.
3. Shut off all other gas fired appliances.
4. Start the unit in heating mode and allow it to run for at least
three minutes.
5. Using an in-line flow meter, measure the gas flow rate through
the supply line to the unit. Convert the reading into cubic feet
per hour. Refer to the meter manufacturer’s instructions, or
the gas supplier for more information.
6. Multiply the gas flow rate in cubic feet per hour by the heating
value of the gas in Btu per cubic foot to obtain the firing rate in
Btu per hour. See Example 2 below.
The manifold pressure
must be set to the appropriate value for your installation.
Adjustments to the firing rate can be made by adjusting
the gas manifold pressure.
CHECKING THE MANIFOLD PREssURE
The manifold pressure can be measured by installing a pressure
gauge or U-tube manometer to the OUTLET end of the gas
valve as follows:
1. Turn off all electrical power to the appliance.
2. Shut OFF the gas supply at the manual shutoff valve located
outside of the appliance.
3. Using a 3/16” Allen wrench, remove the manifold pressure tap
plug located on the outlet side of the gas valve. See Figure
2 (page 5).
4. Install an 1/8” NPT pipe thread fitting, that is compatible with
a Manometer or similar pressure gauge.
5. Connect the Manometer or pressure gauge to the manifold
pressure tap. Turn gas supply on at manual shutoff.
6. Set the room thermostat above room temperature to start the
furnace.
7. Allow the unit to operate for 3 minutes and then check the
manifold pressure. For LP gas installations, the manifold
pressure should be set to approximately 9.5” WC. If the manifold
pressure is not set to the appropriate pressure, then it must
be adjusted.
ADjUsTING THE MANIFOLD PREssURE
NOTE 1: The new valve LP regulator springs must be adjusted
to the proper input firing rates or manifold settings. Both HIGH
and LOW fire inputs should be checked. Always inspect the unit
rating label to determine the correct (0-2,000 ft) factory setting.
See Table 4 (page 6).