Warning, High altitude deration, Pressure gauge installation – Reznor R6GN Option - Installation - LP Conv Kit User Manual
Page 3
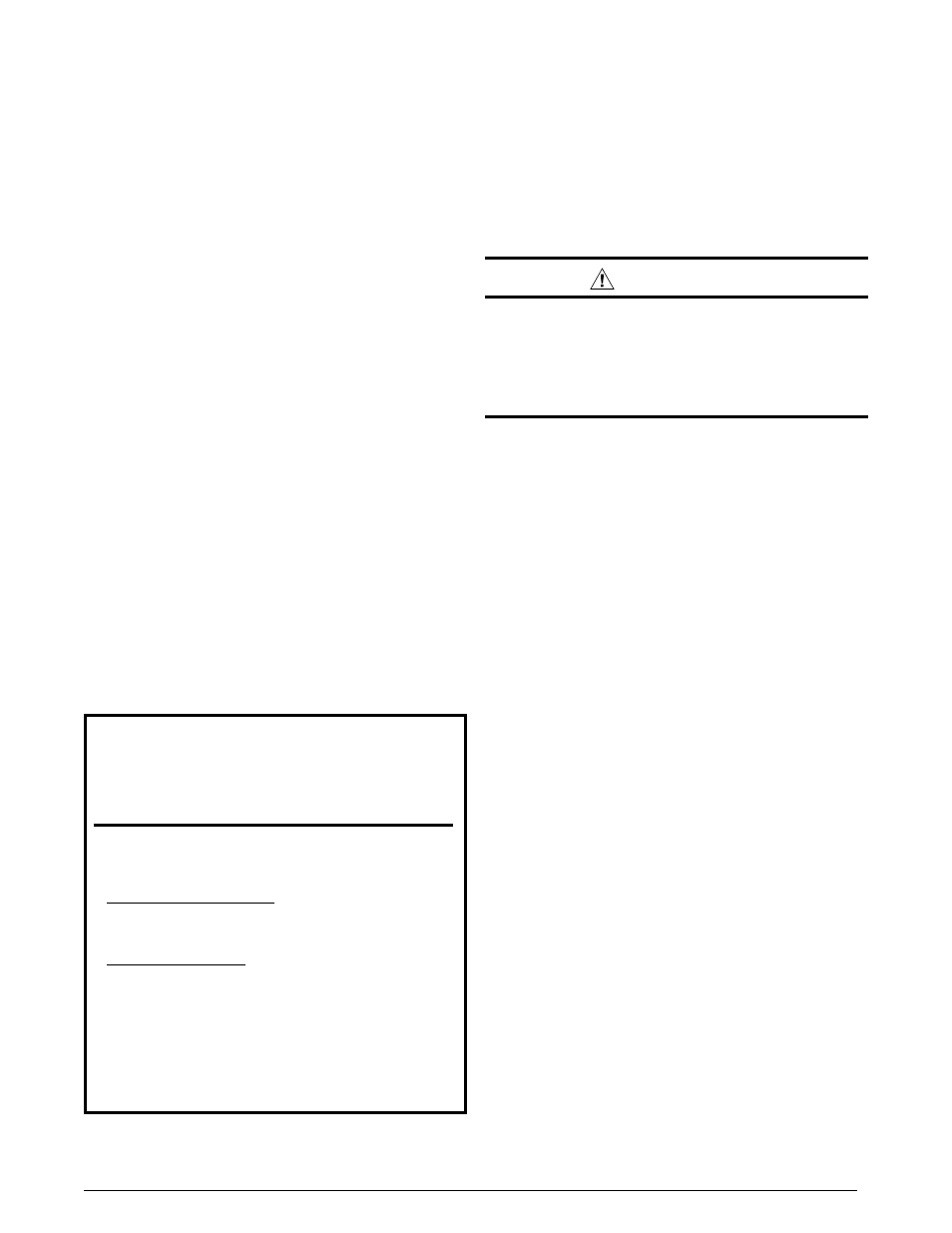
3
HIGH ALTITUDE DERATION
High altitude application with this unit depends on the installation
altitude and the heating value of the gas. At high altitudes, the
heating value of natural gas is always lower than the heating
value at sea level.
All installations of this equipment must be made in accordance
with the National Fuel Gas Code or with local jurisdiction codes.
For installations at altitudes 2,000 feet or below, the installer does
not need to derate the heat exchanger performance.
WARNING:
The reduction of input rating necessary for high
altitude installation may only be accomplished with
factory supplied orifices. Do not attempt to drill out
orifices in the field. Improperly drilled orifices may
cause fire, explosion, carbon monoxide poisoning,
personal injury or death.
IMPORTANT NOTEs:
• For any installation that exceeds 2,000 feet, the input
rate must be reduced 4% per 1,000 feet of altitude
(example: 12% at 3,000 feet, 16% at 4,000 feet, etc).
Always round up to the next highest value of 1,000. So
an installation at 3,120 feet is derated by 16% due to
rounding up to 4,000.
• Deration is necessary to compensate for low atmospheric
pressure at high altitudes. Generally this will require
obtaining the gas heating value from the local gas utility
and replacing the burner orifices.
• Low fire rates for 2-stage operation must also be verified.
• Table 2 lists the correct orifice size to use at different
altitudes. See Installation Example 1 to determine the
unit rating and orifice size.
• After changing the orifices, it is required that you measure
the gas input rate by clocking the gas meter and using
the local gas heating value. See Verifying & Adjusting
the Firing Rate (page 4).
IMPORTANT NOTE: Observe the action of the
burners to make sure there is no yellowing, lifting
or flashback of the flame.
EXAMPLE 1:
Elevation: ....................................................3,890 feet
Type of Gas:
.......................................... Propane Gas
Unit Model: ................................... R6GN-150C180C
At 4,000 feet, the unit needs to be derated by 4% for each
1,000 feet of elevation. This equates to 16% or less than the
sea level rating of 153,000 Btu/h.
1. Determine unit input rating:
[153k x (100-16)%] = 129,000 Btuh. The required
heating rate for 3,890 feet is 129,000 Btu/h.
2. Determine orifice size:
From Table 2 (page 6), find the Unit Model Number.
Follow across the row and stop at the 2,001 - 4,000
elevation column. For this example, the orifice size
displayed is #50. For units equipped with a White-
Rodgers gas valve, install one #50 orifice in every
burner and check the firing rate. In this example, the
firing rate must not exceed 129,000 Btu/h.
IMPORTANT NOTEs:
• Before installing an orifice, check the face or side of
the orifice for the drill number to ensure that it is the
appropriate size.
• To prevent cross threading, hand tighten the orifices
into the gas manifold assembly until snug, then tighten
with a wrench 1/2 to 1 turn.
• For units converted for operation above 2,000 ft., follow
the High altitude deration instructions.
4. Replace factory burners with the new L.P. burners supplied in
this kit. Check burner and carryover alignment (on the burner
carryover bar), then fasten securely using all screws removed
in Step 9.
5. Reinstall burner box assembly to heat exchanger panel using
the four fasteners removed in Step 9.
6. Install manifold pipe with new LP orifices onto the burner box
assembly using four fasteners removed in Step 7. Make sure
all orifices are aligned into the burners.
NOTE:To complete the conversion from natural gas to LP
gas, the main gas valve must be replaced. Main gas valve
(#624695), White Rodgers Model # 36H6A must be used.
7. Using two wrenches, carefully reinstall the factory gas piping
and new LP Gas Valve to the manifold elbow. DO NOT ALLOW
The BuRNeR ASSemBLY TO ROTATe
. Make sure a leak
tight seal using joint compound approved for LP gas or other
equivalent approved methods. Secure the gas valve and piping
assembly using existing unit clamp.
8. Upon completion of the installation, inspect the alignment of
the burners with the heat exchanger tubes. The center of the
burners should be aligned with the center of the tubes.
9. Reconnect the main gas piping to the gas valve.
10. Reconnect wiring to the gas valve terminals. White wire to
Low (M), Brown wire to HI, and the Black wire to Common
(C).
11. Reconnect the spark ignitor wire to the spark ignitor.
12. Reconnect the red flame sensor wire to the flame sensor
and two blue wires to the flame roll-out switch.
PREssURE GAUGE INsTALLATION
For LP Gas installations: Refer to the unit rating plate to determine
the incoming gas maximum and minimum inlet pressures. The
incoming gas line pressure at the gas valve inlet must be between
11.0” WC and 14.0” WC.
ImPORTANT NOTe: If pressure testing the gas supply lines
at pressures greater than 1/2 psig (14” WC), the unit must be
disconnected from the gas supply piping system to prevent
damage to the gas valve.