Digilent 410-259P User Manual
Page 3
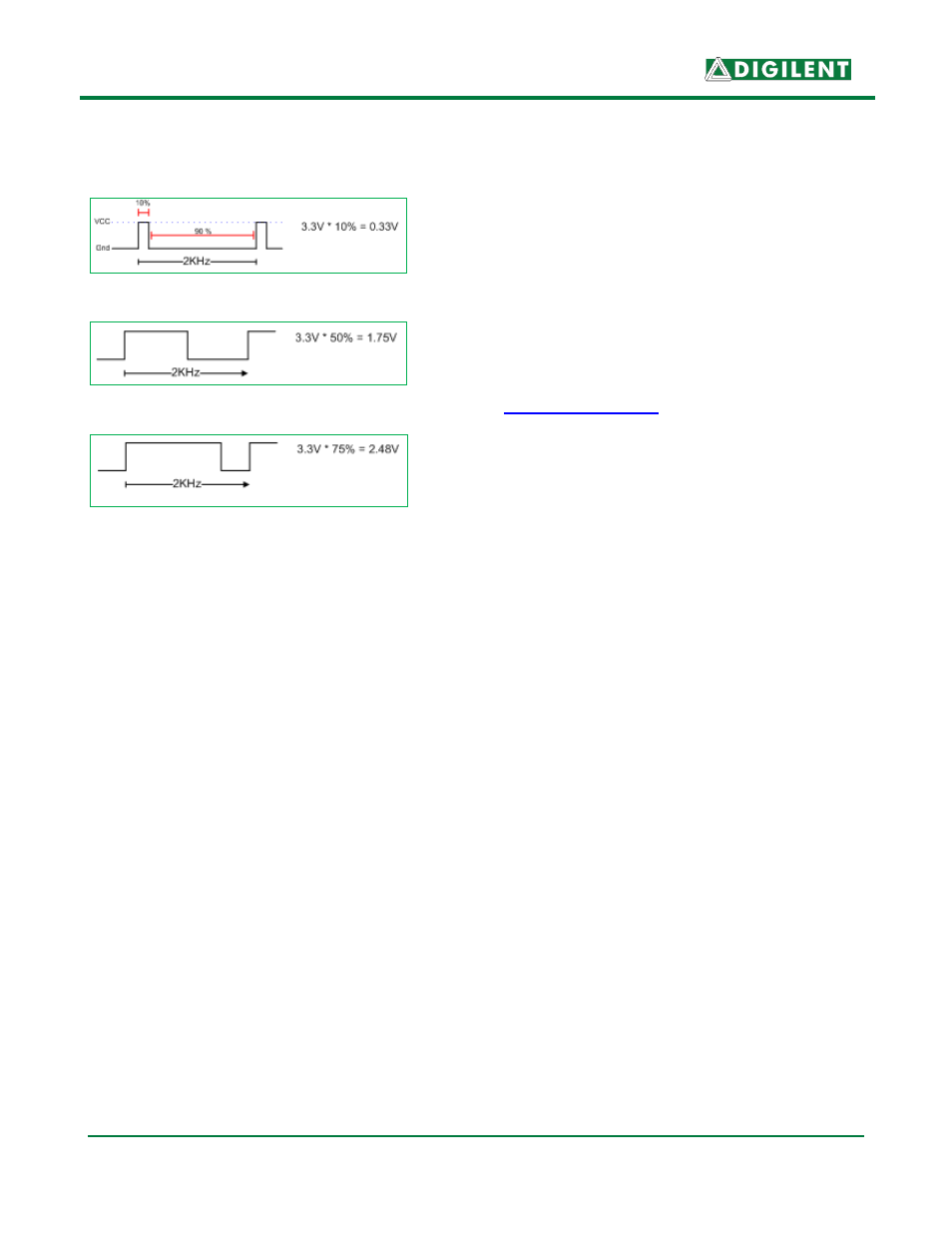
PmodDHB1™ Reference Manual
®
www.digilentinc.com
www.digilentinc.com
Copyright Digilent, Inc.
page 3 of 3
Figure 1.) Figures 2 and 3 represent duty
cycles of 50% and 75%.
Figure 1. 10% Duty Cycle
Figure 2. 50% Duty Cycle
Figure 3. 75% Duty Cycle
An H-bridge is a voltage amplification and
direction control circuit. Customers should use
the H-bridge to format the signal to the
appropriate motor voltage and polarity to spin
the motor.
The changing magnetic forces that occur as
you intermittently apply voltage drive the
motor. Even when the voltage stops,
momentum causes the motor to continue
spinning. At a high enough frequency, this
process of powering and coasting enables the
motor to achieve a smooth rotation that can
easily be controlled through digital logic.
PWM has two important effects on DC motors.
PWM overcomes inertial resistance more
easily at startup because short bursts of
maximum voltage achieve a greater degree of
torque than the equivalent DC voltage. PWM
also generates a higher level of heat inside the
motor. If customers use a pulsed motor for an
extended time, they will need heat dissipation
systems to prevent damage to the motor.
Because of these effects, it is best to use PWM
in high-torque infrequent-use applications such
as airplane flap servos and robotics.
PWM circuits can also create radio frequency
interference (RFI) that operators can minimize
by locating motors near the controller and by
using short wires. You may also need to filter
line noise created by continually powering up
the motor to prevent interference with the rest
of the circuits. You can place small ceramic
capacitors directly across the motor terminals
and between the motor terminals and the
motor case to filter the RFI emissions from the
motor.
Note: For more information on the Pmod
DHB1 see the product page at
www.digilentinc.com
.