Troubleshooting – AERCO BMK 3.0 LN Nat. Gas June 2010 User Manual
Page 64
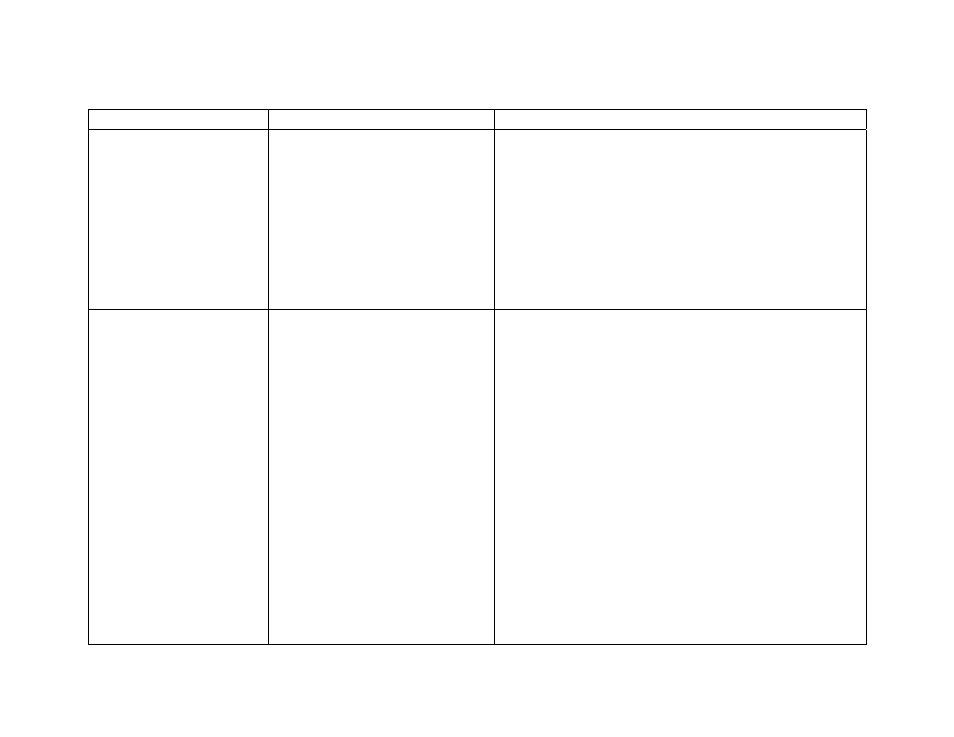
TROUBLESHOOTING
TABLE 8-1. BOILER TROUBLESHOOTING – Continued
FAULT INDICATION
PROBABLE CAUSES
CORRECTIVE ACTION
HIGH GAS
PRESSURE
1. Incorrect supply gas pressure.
2. Defective SSOV Actuator gas
pressure adjustment regulator.
3. Defective High Gas Pressure Switch
4. Gas pressure snubber not installed.
1. Check to ensure gas pressure at inlet of SSOV is 2 psig
maximum.
2. If gas supply pressure downstream of the SSOV cannot be
lowered, to 1.8” W.C. (see para. 4.3, step 10), the SSOV
Actuator gas pressure adjustment regulator may be defective.
3. Remove the leads from the high gas pressure switch and
measure continuity across the common and normally closed
terminals with the unit not firing. Replace the switch if it does not
show continuity.
4. See Figure 8-1. Ensure that the gas pressure snubber is installed
at the high gas pressure switch.
HIGH WATER TEMP
SWITCH OPEN
1. Faulty Water temperature switch.
2. Incorrect PID settings.
3. Faulty shell temperature sensor.
4. Unit in Manual mode
5. Unit setpoint is greater than Over
Temperature Switch setpoint.
6. Boiler Management System PID or
other settings not correctly setup.
7. No interlock to boiler or BMS to
disable boiler(s) in event that system
pumps have failed.
8. System flow rate changes are
occurring faster than boilers can
respond.
1. Test the temperature switch to insure it trips at its actual water
temperature setting.
2. Check PID settings against Menu Default settings in the
Appendix. If the settings have been changed, record the current
readings then reset them to the default values.
3. Using the resistance charts in the Appendix C, Measure the
resistance of Shell sensor and BTU sensor at a known water
temperature.
4. If unit is in Manual Mode switch to Auto Mode.
5. Check setpoint of unit and setpoint of Temperature Switch;
Ensure that the temperature switch is set higher than the unit’s
setpoint.
6. Check the BMS for changes to PID default values, correct as
necessary.
7. If system pump is controlled by Energy Management System
other than BMS or pumps are individually controlled by boiler,
check to see if there are flow switches interlocked to the BMS or
boiler.
8. If the system is a variable flow system, monitor system flow
changes to ensure that the rate of flow change is not faster than
what the boilers can respond to.
8
-
6