Installation – AERCO BMK 1.5 LN June 2010 User Manual
Page 15
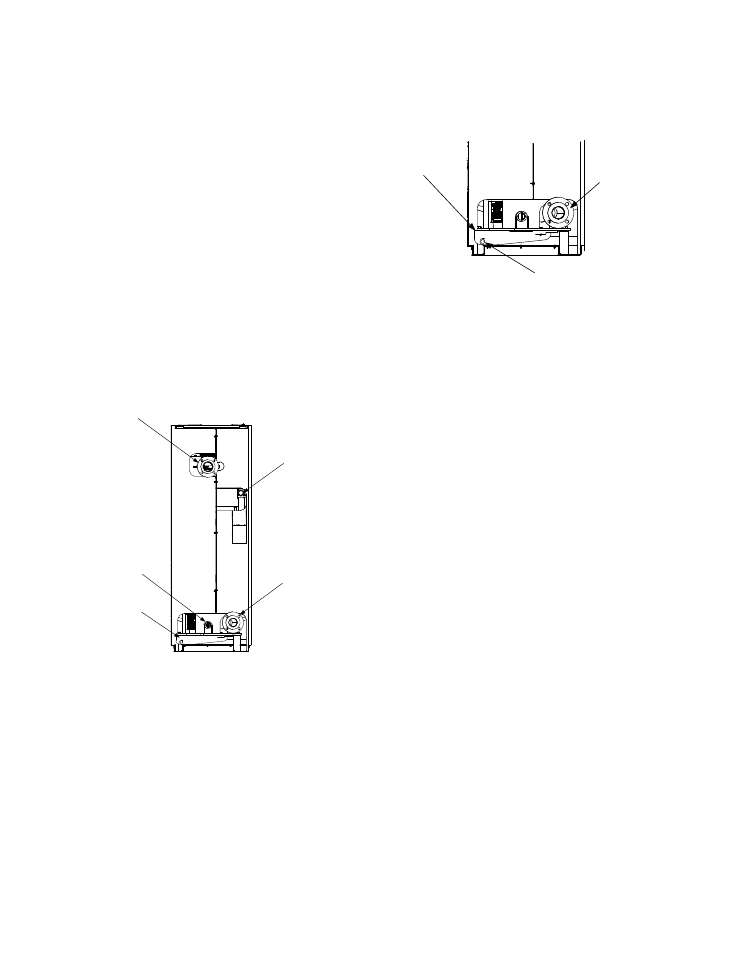
INSTALLATION
2-3
In multiple unit installations, it is important to
plan the position of each unit in advance.
Sufficient space for piping connections and
future service/maintenance requirements must
also be taken into consideration. All piping must
include ample provisions for expansion.
If installing a Combination Control Panel (CCP)
system, it is important to identify the
Combination Mode Boilers in advance and place
them in the proper physical location. Refer to
Chapter 5 for information on Combination Mode
Boilers.
2.5 SUPPLY AND RETURN PIPING
The Benchmark 1.5 Boiler utilizes 3” 150#
flanges for the water system supply and return
piping connections. The physical location of the
supply and return piping connections are on the
rear of the unit as shown in Figure 2-3. Refer to
Appendix F, Drawing AP-A-832 for additional
dimensional data.
BOILER SUPPLY
3" – 150# FLANGED
CONNECTION
BOILER RETURN
3" – 150# FLANGED
CONNECTION
1-1/2”
GAS INLET
CONNECTION
SHELL DRAIN
VALVE
EXHAUST
MANIFOLD
REAR VIEW
Figure 2-3
Supply and Return Locations
2.6 CONDENSATE DRAIN
The Benchmark 1.5 Boiler is designed to
condense water vapor from the flue products.
Therefore, the installation must have provisions
for suitable condensate drainage or collection.
The condensate drain pipe located on the
exhaust manifold (Figure 2-4) must be
connected to a condensate trap which is packed
separately within the unit’s shipping container.
The procedure to install and connect the
condensate drain is provided in paragraph 2.6.1.
EXHAUST
MANIFOLD
PARTIAL REAR VIEW
CONDENSATE DRAIN
CONNECTION
BOILER
RETURN
Figure 2-4
Condensate Drain Connection Location
2.6.1 Exhaust Manifold Condensate
Drain
The exhaust manifold drain pipe connection
shown in Figure 2-4, must be connected to a
condensate drain trap external to the unit. Refer
to Figure 2-5 and install the trap as follows:
1. Install 3/4” NPT nipples in the tapped inlet
and outlet of the condensate trap (part no.
24060).
2. Install a third 3/4” NPT nipple in the tapped
condensate outlet of the exhaust manifold.
3. Connect the exhaust manifold nipple to the
condensate trap inlet using a female union.
4. install a suitable support under the
condensate trap and ensure that the trap is
level.
5. Connect a length of 1” I.D. polypropylene
hose (part no. 91030) to the nipple on the
outlet side of the condensate trap and
secure it with a hose clamp.
6. Route the hose on the trap outlet to a
nearby floor drain.
If a floor drain is not available, a condensate
pump can be used to remove the condensate to
drain. The maximum condensate flow rate is 20
GPH. The condensate drain trap, associated
fittings and drain lines must be removable for
routine maintenance.