Checkline TI-007 User Manual
Page 7
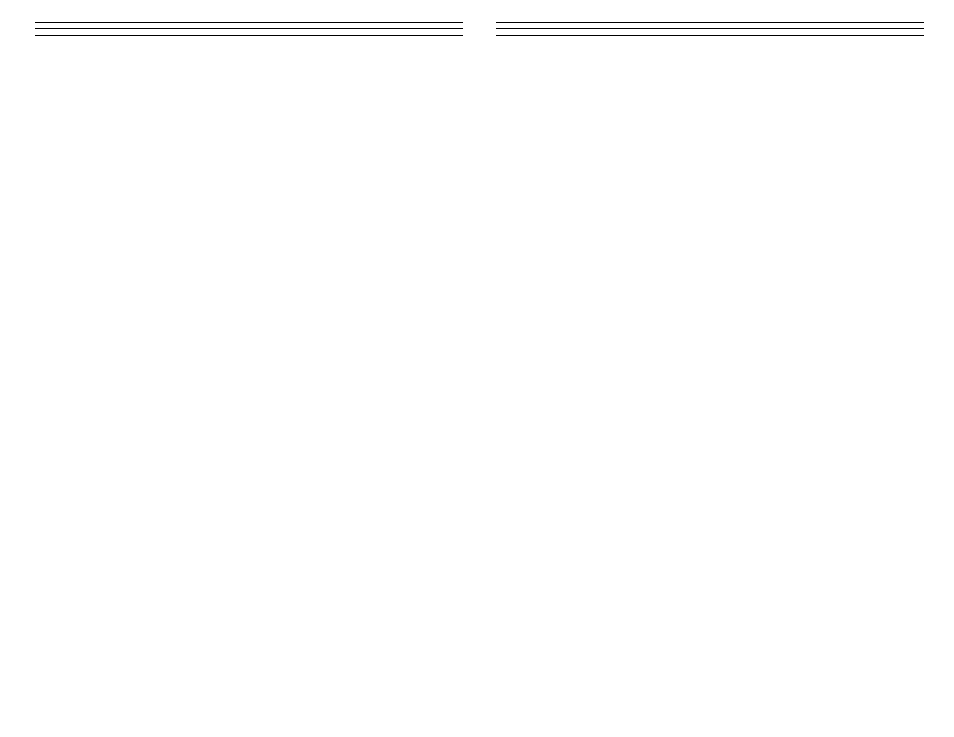
– 10 –
4 .0
T RAN SDU CER SELECT I ON
The TI-007 is inherently capable of performing measurements on a wide range of
materials, from various metals to glass and plastics. Different types of material, however,
will require the use of different transducers. Choosing the correct transducer for a job is
critical to being able to easily perform accurate and reliable measurements. The following
paragraphs highlight the important properties of transducers, which should be considered
when selecting a transducer for a specific job.
Generally speaking, the best transducer for a job is one that sends sufficient ultrasonic
energy into the material being measured such that a strong, stable echo is received by
the TI-007. Several factors affect the strength of ultrasound as it travels. These are
outlined below:
Initial Signal Strength
The stronger a signal is to begin with, the stronger its return echo will be. Initial signal
strength is largely a factor of the size of the ultrasound emitter in the transducer. A large
emitting area will send more energy into the material being measured than a small
emitting area. Thus, a so-called “1/4-inch” transducer will emit a stronger signal than
a “1/8-inch” transducer.
Absorption and Scattering
As ultrasound travels through any material, it is partly absorbed. If the material through
which the sound travels has any grain structure, the sound waves will experience scatter-
ing. Both of these effects reduce the strength of the waves, and thus, the TI-007’s ability
to detect the returning echo.
Higher frequency ultrasound is absorbed and scattered more than ultrasound of a lower
frequency. While it may seem that using a lower frequency transducer might be better in
every instance, low frequencies are less directional than high frequencies.
Geometry of the Transducer
The physical constraints of the measuring environment sometimes determine a transduc-
er’s suitability for a given job. Some transducers may simply be too large to be used in
tightly confined areas. Also, the surface area available for contacting with the transducer
may be limited, requiring the use of a transducer with a small cone tipped delay line.
Measuring on a curved surface, may require the use of a transducer with a matching
curved wearface.
Temperature of the Material
When it is necessary to measure on surfaces that are exceedingly hot, special delay lines
may be neccessary. Additionally, care must be taken when performing a “Calibration to
Known Thickness” with a high temperature application. See Appendix B for more
information on measuring materials with a high temperatures.
Selection of the proper transducer is often a matter of tradeoffs between various
characteristics. It may be necessary to experiment with a variety of transducers
in order to find one that works well for a given job. ELECTROMATIC can provide
assistance in choosing a transducer, and offers a broad selection of transducers
for evaluation in specialized applications.
– 7 –
large ranges. The TI-007 provides two simple methods for setting the sound-velocity,
described in the following pages.
Calibration to a known thickness
NOTE: This procedure requires a sample piece of the specific material to be measured, the
exact thickness of which is known, e.g. from having been measured by some other means.
1. Make sure the TI-007 is ON.
2. Apply couplant to the sample piece.
3. Press the transducer against the sample piece, making sure that the transducer sits flat
against the surface of the sample. The display should show some (probably incorrect)
thickness value, and the Stability Indicator should have nearly all its bars on.
4. Having achieved a stable reading, remove the transducer. If the displayed thickness
changes from the value shown while the transducer was coupled, repeat step 3.
5. Press the CAL key. The IN (or MM) symbol should begin flashing.
6. Use the UP and DOWN arrow keys to adjust the displayed thickness up or down,
until it matches the thickness of the sample piece.
7. Press the CAL key again. The IN/µs (or M/s) symbols should begin flashing.
The TI-007 is now displaying the sound velocity value it has calculated based
on the thickness value that was entered in step 6.
8. Press the CAL key once more to exit the calibration mode. The TI-007 is now ready
to perform measurements.
Calibration to a known velocity
NOTE: This procedure requires that the operator know the sound-velocity of the material to
be measured. A table of common materials and their sound-velocities can be found in
Appendix C.
1. Make sure the TI-007 is ON.
2. Press the CAL key to enter calibration mode. If the IN (or MM) symbol is flashing,
press the CAL key again, so that the IN/µs (or M/s) symbols are flashing.
3. Use the UP and DOWN arrow keys to adjust the displayed velocity up or down, until
it matches the sound-velocity of the material to be measured.
4. Press the CAL key once more to exit the calibration mode. The TI-007 is now ready
to perform measurements.
NOTE: At any time during the calibration procedure (IN, MM, IN/µs, or M/s flashing
in the display), pressing the SCAN key will restore the tool to the factory default
sound-velocity for steel (0.233 IN/µs).
To achieve the most accurate measurements possible, it is generally advisable to always
calibrate the TI-007 to a sample piece of known thickness. Material composition (and thus,
its sound-velocity) sometimes varies from lot to lot and from manufacturer to manufacturer.
Calibration to a sample of known thickness will ensure that the tool is set as closely as
possible to the sound velocity of the material to be measured.