Checkline TI-007 User Manual
Page 6
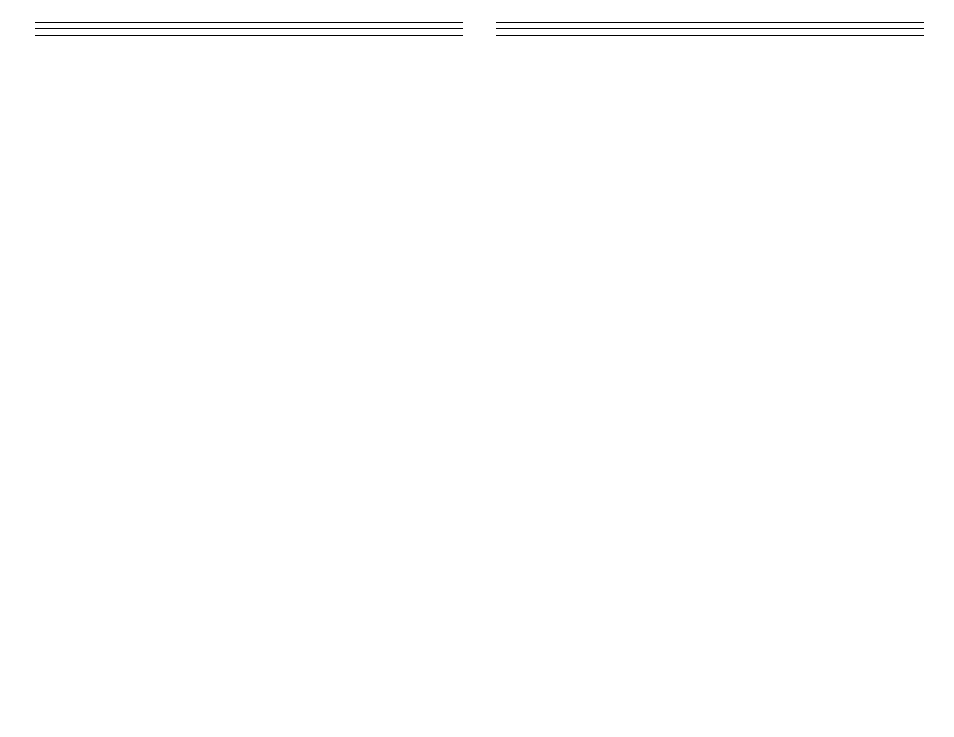
– 11 –
5 .0
APPEN DI X A — PRODU CT SPECI FI CAT I ON S
Weight:
10 ounces(with batteries).
Size:
2.5W x 4.5 H x 1.24 D inches
(63.5W x 114.3 H x 31.5 D mm).
Operating Temp.:
–20 to 120 °F (–30 to 50 °C)
Case:
Extruded aluminum body / nickel plated aluminum
end caps.
Keypad:
Sealed membrane, resistant to water and petroleum
products.
Power Source:
Two “AA” size, 1.5 volt alkaline or 1.2 volt NiCad cells.
150 hours typical operating time on alkaline,
100 hours on NiCad.
Display:
Liquid-Crystal-Display,
4.5 digits, 0.500 inch high numerals.
LED backlight.
Measuring Range:
0.0060 to 1.0000 inches (0.15 to 25.40mm) — Steel
Resolution:
0.0001 inch (0.001mm)
Accuracy:
±0.0001 inch (0.001mm), depends on material
and conditions
Sound Velocity Range:
0.0492 to 0.3937 in/ms (1250 to 10000m/s)
– 6 –
IMPORTANT
Occasionally, a small film of couplant will be drawn out between the transducer and the
surface as the transducer is removed. When this happens, the TI-007 may perform a mea-
surement through this couplant film, resulting in a measurement that is larger or smaller
than it should be. This phenomenon is obvious when one thickness value is observed while
the transducer is in place, and another is observed after the transducer is removed.
Condition and Preparation of Surfaces
In any ultrasonic measurement scenario, the shape and roughness of the test surface are of
paramount importance. Rough, uneven surfaces may limit the penetration of ultrasound
through the material, and result in unstable, and therefore unreliable, measurements. The
surface being measured should be clean, and free of any small particulate matter, rust, or
scale. The presence of such obstructions will prevent the transducer from seating properly
against the surface. Often, a wire brush or scraper will be helpful in cleaning surfaces. In
more extreme cases, rotary sanders or grinding wheels may be used, though care must be
taken to prevent surface gouging, which will inhibit proper transducer coupling.
Extremely rough surfaces, such as the pebble-like finish of some cast iron, will prove most
difficult to measure. These kinds of surfaces act on the sound beam like frosted glass on
light: the beam becomes diffused and scattered in all directions.
In addition to posing obstacles to measurement, rough surfaces contribute to excessive
transducer wear, particularly where the transducer is “scrubbed” along the surface.
Selecting Measurement Mode
The TI-007 is equipped with four measurement mode options (echo-echo, interface-echo,
plastic, auto). In echo-echo mode, the gauge can read thin metals down to .006 inches
(.15 millimeters). The echo-echo mode also allows the user to measure the thickness of
metals that have been previously coated or painted on the surface. This enables the user to
determine the thickness of the metal without having to remove the paint. In interface-echo
mode, the gauge can read plastics and thicker materials. The TI-007’s auto mode will auto-
matically switch between modes according to the different materials being measured. The
following section outlines how to switch between measurement modes:
Measurement Modes
1. Make sure the TI-007 is ON.
2. Press the UP arrow key to toggle between measurement modes. The gauge will display
PLAS followed by I-E (Interface Echo), E-E (Echo-Echo), PLAS (Plastic) or AutO
(Auto) depending on which TI-007 mode was last used.
3. Repeat step 2 until the desired mode has been displayed.
Calibration
In order for the TI-007 to make accurate measurements, it must be set to the correct
sound-velocity for the material being measured. Different types of material have different
inherent sound-velocities. For example, the velocity of sound through steel is about 0.233
inches-per-microsecond, versus that of aluminum, which is about 0.248 inches-per-
microsecond. If the tool is not set to the correct sound-velocity, all of the measurements
the tool makes will be erroneous by some fixed percentage. The one point calibration is
the simplest and most commonly used calibration procedure - optimizing linearity over