Checkline TI-007 User Manual
Page 5
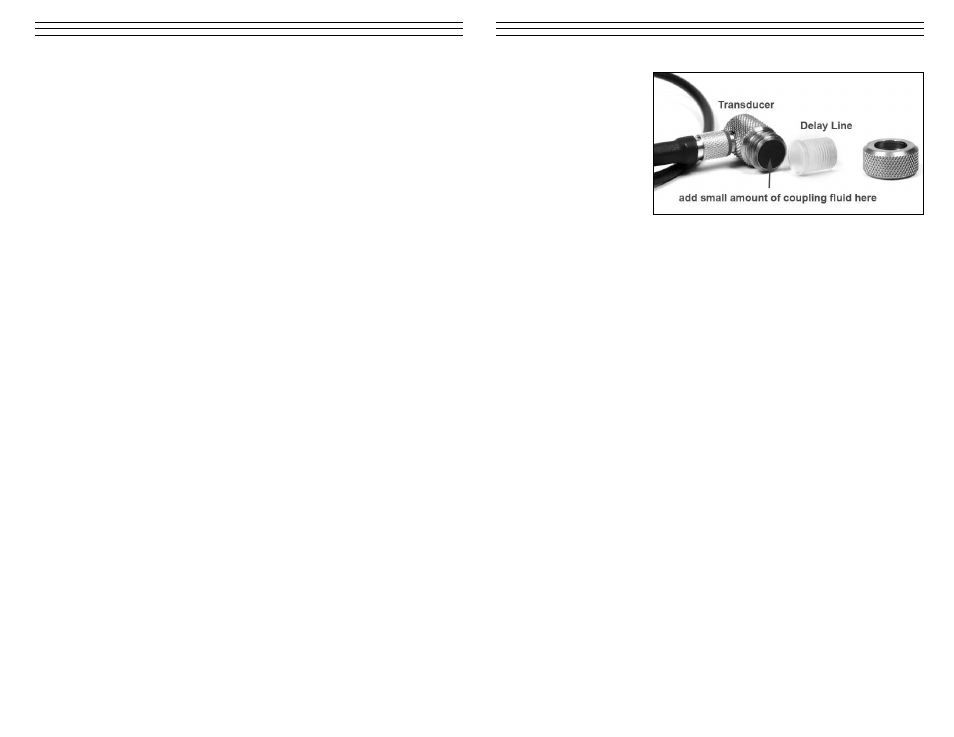
– 12 –
6 .0
APPEN DI X B — APPLI CAT I ON N OT ES
Measuring tubing
When measuring a piece of tubing for wall thickness, it may prove beneficial to have
multiple delay lines with different radiuses for different tubing diameters. The delay lines
can be easily radiused by placing a piece of emery cloth around the tubing and moving the
transducer back and forth until a radius has formed on the tip of the delay line.
Measuring hot surfaces
The velocity of sound through a substance is dependant upon its temperature. As materials
heat up, the velocity of sound through them decreases. In most applications with surface
temperatures less than about 200 °F (100 °C), no special procedures must be observed.
At temperatures above this point, the change in sound velocity of the material being
measured starts to have a noticeable effect upon ultrasonic measurement.
At such elevated temperatures, it is recommended that the user perform a calibration
procedure (refer to page 6) on a sample piece of known thickness, which is at or near
the temperature of the material to be measured. This will allow the TI-007 to correctly
calculate the velocity of sound through the hot material.
When performing measurements on hot surfaces, it may also be necessary to use a
specially constructed high-temperature delay line. It is recommended that the probe be
left in contact with the surface for as short a time as needed to acquire a stable measure-
ment. While the transducer is in contact with a hot surface, it will begin to heat up, and
through thermal expansion and other effects, may begin to adversely affect the accuracy
of measurements.
Measuring laminated materials
Laminated materials are unique in that their density (and therefore sound-velocity) may
vary considerably from one piece to another. Some laminated materials may even exhibit
noticeable changes in sound-velocity across a single surface. The only way to reliably
measure such materials is by performing a calibration procedure on a sample piece of
known thickness. Ideally, this sample material should be a part of the same piece being
measured, or at least from the same lamination batch. By calibrating to each test piece
individually, the effects of variation of sound-velocity will be minimized.
An additional important consideration when measuring laminates, is that any included air
gaps or pockets will cause an early reflection of the ultrasound beam. This effect will be
noticed as a sudden decrease in thickness in an otherwise regular surface. While this may
impede accurate measurement of total material thickness, it does provide the user with
positive indication of air gaps in the laminate.
– 5 –
The Transducer
The transducer is the
“business end” of the
TI-007. It transmits and
receives ultrasonic sound
waves that the TI-007 uses
to calculate the thickness
of thematerial being
measured. The transducer
connects to the TI-007 via
the attached cable, and one
coaxial connector.
The transducer must be used correctly in order for the TI-007 to produce accurate, reliable
measurements. Below is a short description of the transducer, followed by instructions for
its use.
The photo above shows a typical single element delay line transducer. This delay line is
fastened to the transducer with a retainer ring. A drop of couplant is applied between the
delay line and transducer body. The transducer body contains one crystal element that is
responsible for conducting ultrasonic sound into and back from the material being mea-
sured. When the transducer is placed against the material being measured, it is the area
directly beneath the delay line that is being measured.
When measuring, press against the top of the transducer with the thumb or index finger to
hold the transducer in place. Moderate pressure is sufficient, as it is only necessary to keep
the transducer stationary, and the delay line seated flat against the surface of the material
being measured.
Making Measurements
In order for the transducer to do its job, there must be no air gaps between the wear-face
and the surface of the material being measured. This is accomplished with the use of a
“coupling” fluid, commonly called “couplant”. This fluid serves to “couple”, or transfer,
the ultrasonic sound waves from the transducer, into the material, and back again. Before
attempting to make a measurement, a small amount of couplant should be applied to the
surface of the material being measured. Typically, a single droplet of couplant is sufficient.
After applying couplant, press the transducer (wearface down) firmly against the area to be
measured. The Stability Indicator should have six or seven bars darkened, and a number
should appear in the display. If the TI-007 has been set to the correct sound velocity
(see page 6), the number in the display will indicate the actual thickness of the material
directly beneath the transducer.
If the Stability Indicator has fewer than five bars darkened, or the numbers on the display
seem erratic, first check to make sure that there is an adequate film of couplant beneath the
transducer, and that the transducer is seated flat against the material. If the condition per-
sists, it may be necessary to select a different transducer (size or frequency) for the materi-
al being measured. See page 10 for information on Transducer selection.
While the transducer is in contact with the material that is being measured, the TI-007
will perform four measurements every second, updating its display as it does so. When the
transducer is removed from the surface, the display will hold the last measurement made.