Fts-1 fork threading set – Park Tool FTS-1 User Manual
Page 2
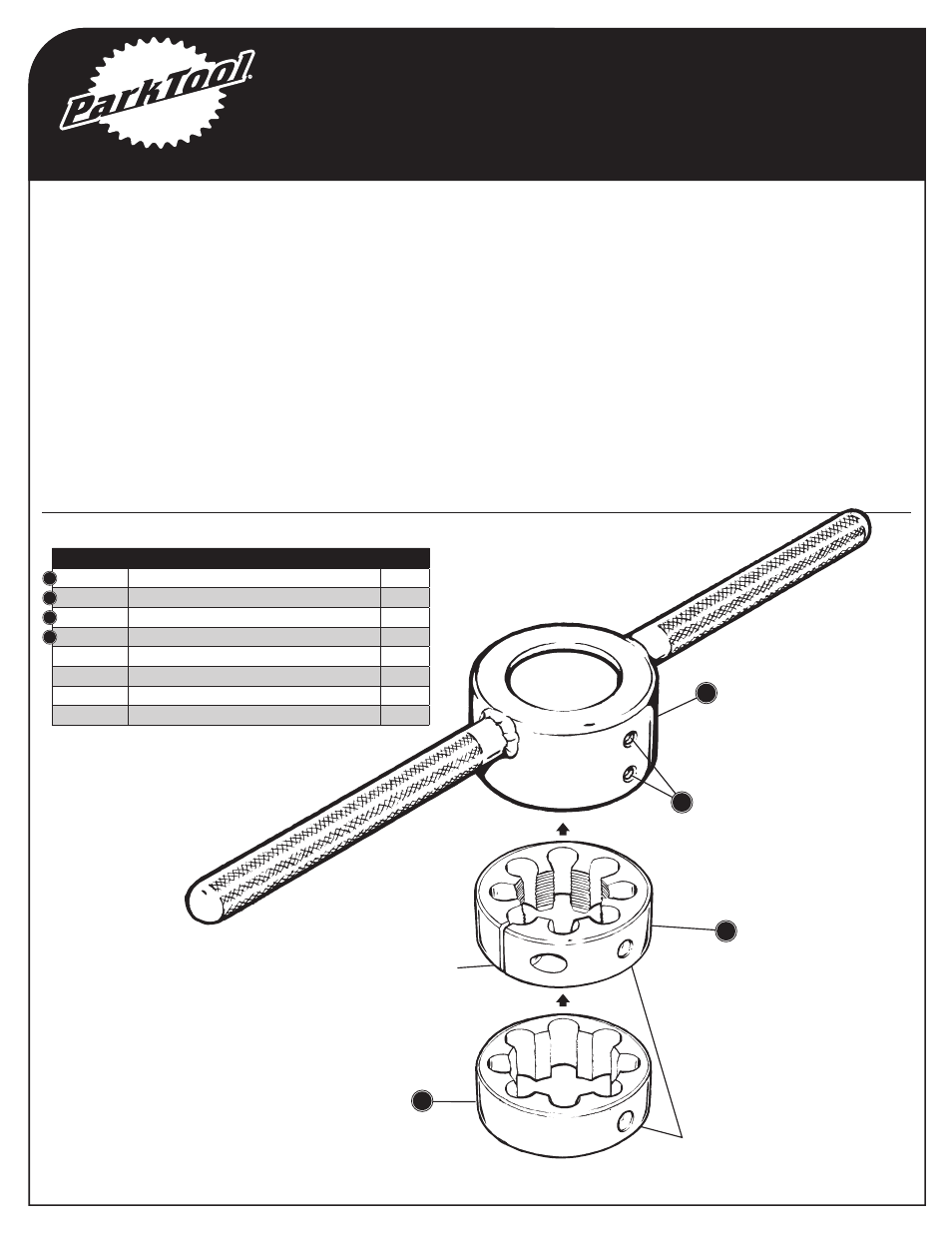
Park Tool Co.
5115 Hadley Ave. N., St. Paul, MN 55128 (USA) www.parktool.com
Part No. Description
Qty.
605
Handle Assembly
1
606
1”x 24 tpi Cutting Die
1
609
Set Screw
4
610
1” Thread Guide
1
607
1-1/8”x 26 tpi Cutting Die (optional)
–
608
1-1/4”x 26 tpi Cutting Die (optional)
–
611
1-1/8” Thread Guide (optional)
–
612
1-1/4” Thread Guide (optional)
–
FTS-1 part numbers
1
2
3
4
FTS-1 Fork Threading Set
4
2
1
Cutting Die
Schneideisen
Filière
Dado de Corte
Set Screw Positioning Points
Fixierpunkte
Points de fixation des vis
Ranuras para tornillos de sujeción
Handle Assembly
Werkzeugschaft
Porte filière
Maneral
Set Screws
Fixierschrauben
Vis de fixation
Tornillos de Sujeción del maneral
Adjustment Screw
Justierschraube
Vis de réglage
Tornillo de Ajuste
Thread Guide
Gewindeführung
Guide de filière
Guia de Corte
3
The Park Tool FTS-1 Fork Threading Set is a precision tool designed for cutting new
threads and for chasing existing threads on metal fork columns that are not chromed.
The unique thread guide system used with the FTS-1 is specially designed to allow the
chips and shavings that result during use to fall completely through the guide, prevent-
ing damage to the fork threads and the tool.
The FTS-1 includes die handles, 1” x 24 tpi cutting die and 1” thread guide. 1-1/8” x 26 tpi
die, 1-1/4” x 26 tpi die, 1-1/8” guide and 1-1/4” guide are available as accessories.
Instructions
Always wear safety glasses when using the FTS-1 or any cutting tool.
1. Loosen the set screws (#609) on the FTS-1’s handle assembly (#605) and remove the
cutting die (#606) and thread guide (#610).
2. Locate the adjustment screw in the cutting die. This adjustment screw allows the
die diameter to be expanded or contracted. Turning the adjustment screw clockwise
expands the die diameter, while turning the adjustment screw counter-clockwise
contracts the die diameter. Using the adjustment screw, expand the die completely
and thread the die clockwise onto the fork threads (the tapered side of the die should
contact the threads of the fork first) until fully engaged. Then use the adjustment
screw to contract the die so that the die is snug, but not tight, on the fork threads.
3. Remove the die from the fork threads and position the die and the guide into the
handle assembly. Tighten the four set screws in the handle assembly, making sure
the set screws are in line with the positioning points in the die and guide.
4. Liberally apply cutting oil or cutting fluid to the threads of the fork and to the die.
Park Tool CF-2 Cutting Fluid is recommended.
5. Lower the FTS-1 onto the fork column, allowing the guide to correctly position the die
onto the fork threads. Using no downward pressure, lightly turn the handle assembly
clockwise until the die engages the threads of the fork. Continue to turn the die down
the threads until resistance is felt. From this point on, the die should be advanced no
more than one quarter turn into the resistance and then backed up one half turn to
break the chips that are formed during the cutting process (the chips that are formed
will fall through the specially designed cutouts in the guide, preventing binding and
damage to the die and the fork threads). Work slowly and keep the die flooded with
cutting oil at all times during the cutting or chasing process to avoid heat build-up.
6. Remove the FTS-1 by turning counterclockwise. Clean oil and chips with a rag, fol-
lowed by a brush and solvent.
7. Thread a headset adjusting race onto the fork threads. If the race is too difficult to
thread on to the fork, readjust the die as detailed in steps 1-3 and take another pass
to increase the depth of the fork threads. Cutting new threads may require more
than one pass with the FTS-1.
Notes: All components should be used and stored with extreme care. Components should
be cleaned and then wiped with an oily cloth or rust inhibitor after use and the cutting die
should be periodically sharpened by a qualified technician. Park Tool Co. offers a sharpen-
ing service that can return cutting tools to factory specifications. Information can be found
at: www.parktool.com.