Theory of operation, Schematic – Elecraft K2 PLL User Manual
Page 4
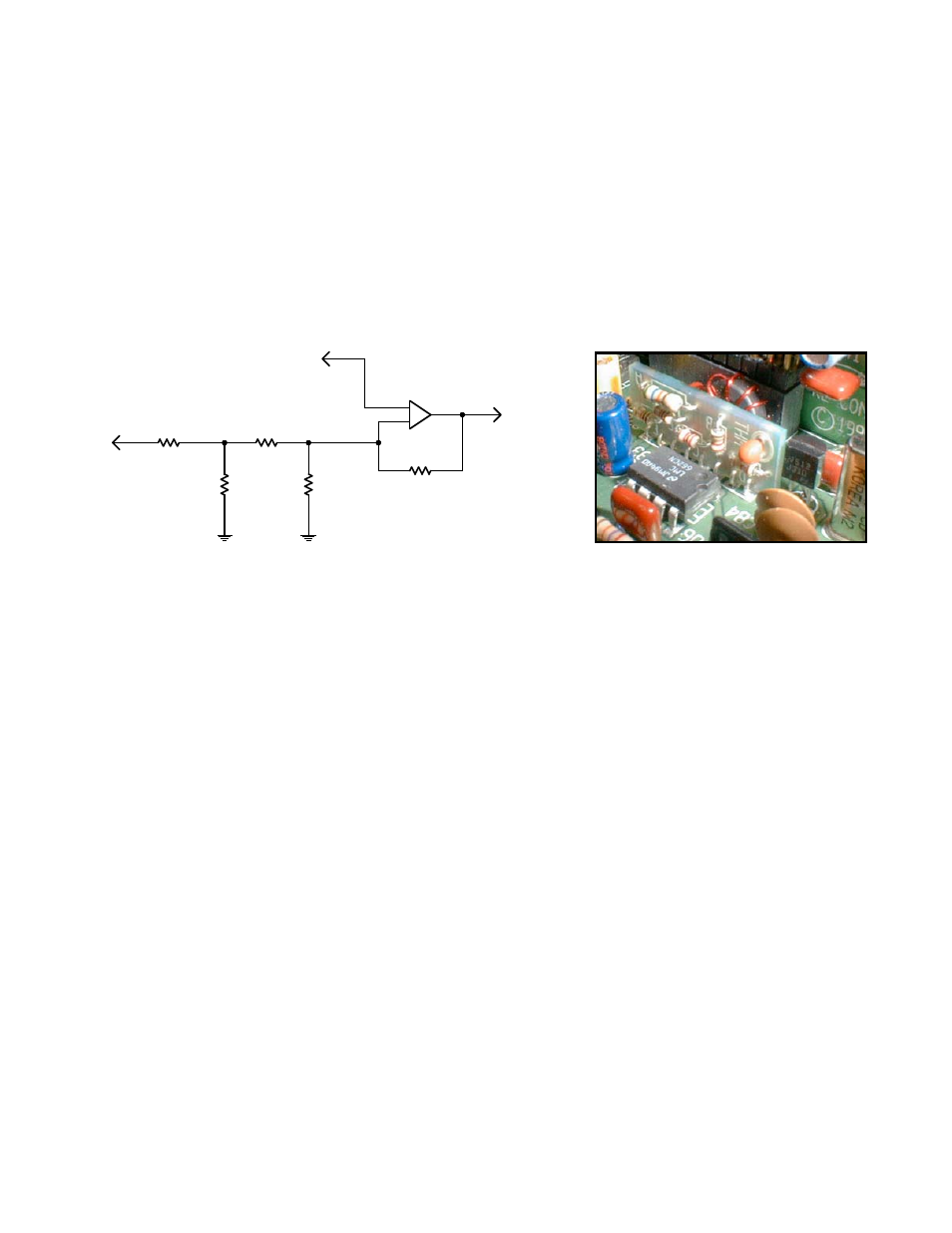
Page 4 of 4
Theory of Operation
The thermistor circuit works by applying a variable offset voltage to varactor diodes D16 and D17 to compensate for drift in the
PLL reference oscillator. As temperature increases, the uncompensated oscillator will drift down in frequency. The thermistor
causes a slight increase in the bias voltage to these diodes as the temperature increases.
The resistor values have been chosen to minimize the drift of the PLL Reference Oscillator over its entire tuning range (typically
10 to 13 kHz). There will still be some residual drift due to component variations and the BFO. The residual drift will usually be
less than 100 Hz over a temperature range of 50F to 110F. This is an order of magnitude better than the uncompensated circuit.
Schematic
The schematic and a photo of the modifications are shown below. All resistors in combination establish the nominal gain of DC
amplifier U6A. The relative values of RA-RD and the thermistor, Rt, set the rate of gain change with temperature. RE and RF (not
shown) replace resistors that were contained in RP3 and have no functional effect on the compensation circuit. In the oscillator
itself (also not shown), L31 has been changed to 12 H, and X1 is a new crystal with improved temperature stability.
To RP2
From U5, Pin 7
+
-
U6A
LMC662
RD
1.8K
RB
12K
RC
2.2K
8B
Rt, 10K@25C
RA
33K
Stability Measurement and Compensation Adjustment (Expert Builders Only)
The procedure below can be used to test and optionally fine-tune the K2's frequency stability as a function of temperature. This
information is provided for builders who have accurate frequency measurement capability and wish to experiment with the
thermistor compensation circuit. Otherwise resistor RA should be left at its original value of 33 k, which will provide very
good results.
To measure the drift of the K2:
1. Allow the K2 to warm up for 30 minutes or longer at room temperature (top, bottom, and side covers should be installed).
2. Switch to the band to be tested (we use 20 meters for comparisons). Set the POWER control for about 1 watt, and connect
the K2 to a dummy load.
3. Enter TUNE mode and measure the K2's transmit frequency using a frequency counter, synthesized receiver, or other stable
instrument. (An alternative is to carefully check the frequency of a reference signal on the K2, such as WWV.)
4. Transmit at 10 to 20 watts into a dummy load for 15 to 30 minutes using TUNE mode. (Use an internally-installed KPA100
at 20 watts if available). This should increase the internal temperature of the K2 by 15 to 30 degrees F, depending on
whether a KPA100 was used or the K2 was "barefoot."
5. Re-measure the K2's transmit frequency at the 1-watt level soon after you stop transmitting (because of the thermal mass,
you have several minutes in which to make this measurement). Again, a receive frequency test can be used as an alternative.
6. The difference in the two frequencies indicates the amount of drift.
On 20 meters, with both the BFO and PLL reference modifications in place, typical drift using this test is 5 to 20 Hz per 15
degrees (F) of temperature change. Before modification, a K2 might drift 100 Hz or more over the same temperature range.
After both the BFO and PLL modifications have been made, the value of resistor RA on the thermistor may optionally be varied
to reduce the drift further. Increasing the value of RA decreases the compensation and will shift the drift toward negative values.
The value of RA should not be made smaller than 15K or larger than 56 k. Note: CAL PLL must be re-run and drift re-measured
after making any change to RA.