05 stick (smaw) welding troubleshooting, Stick (smaw) welding troubleshooting -21, Fabricator 141i – Tweco Fabricator 141i Operating Manual User Manual
Page 81
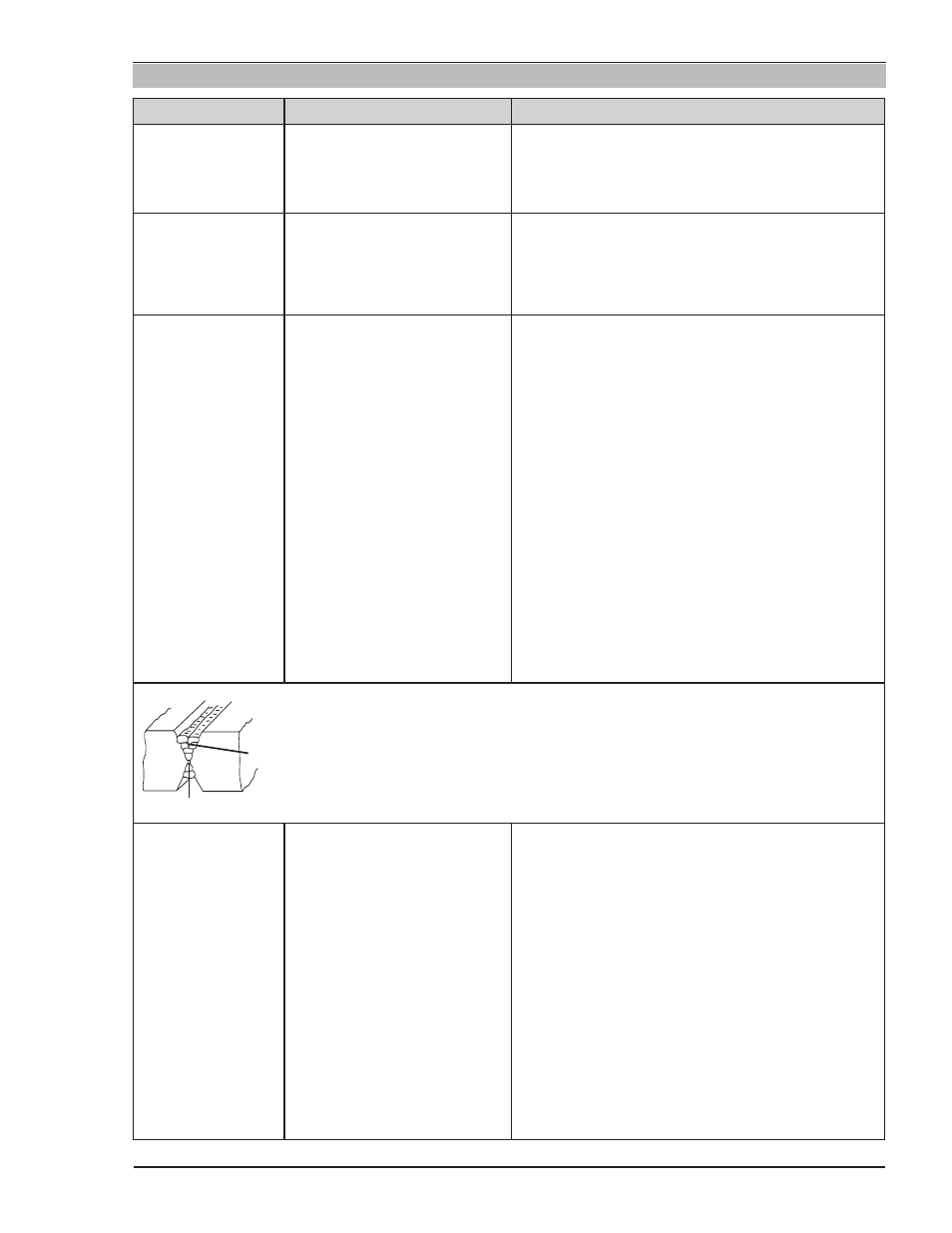
Fabricator 141i
Manual 0-5145
4-21
BASIC WELDING GUIDE
4.05 Stick (SMAW) Welding Troubleshooting
FAULT
CAUSE
REMEDY
1 Welding current
varying
ARC FORCE control knob is
set at a value that causes the
welding current to vary ex-
cessively with the arc length.
Reduce the ARC FORCE control knob until welding
current is reasonably constant while prohibiting the
electrode from sticking to the work piece when you
“dig” the electrode into the workpiece.
2 A gap is left by
failure of the weld
metal to fill the
root of the weld.
A Welding current too low
A Increase welding current.
B Electrode too large for joint. B Use smaller diameter electrode.
C Insufficient gap.
C Allow wider gap.
3 Non-metallic par-
ticles are trapped
in the weld metal.
A Non-metallic particles may
be trapped in undercut from
previous run.
A If a bad undercut is present clean slag bout and
cover with a run from a smaller gauge electrode.
B Joint preparation too re-
stricted.
B Allow for adequate penetration and room for clean-
ing out the slag.
C Irregular deposits allow slag
to be trapped.
C If very bad, chip or grind out irregularities.
D Lack of penetration with slag
trapped beneath weld bead.
D Use smaller electrode with sufficient current to give
adequate penetration. Use suitable tools to remove
all slag from comers.
E Rust or mill scale is prevent-
ing full fusion.
E Clean joint before welding.
F Wrong electrode for position
in which welding is done.
F Use electrodes designed for position in which
welding is done, otherwise proper control of slag is
difficult.
Figure 1- Example of insufficient gap or incorrect sequence
4 A groove has been
formed in the base
metal adjacent to
the toe of a weld
and has not been
filled by the weld
metal (undercut).
A Welding current is too high. A Reduce welding current.
B Welding arc is too long.
B Reduce the length of the welding arc.
C Angle of the electrode is
incorrect.
C Electrode should not be inclined less than 45° to
the vertical face.
D Joint preparation does not
allow correct electrode angle.
D Allow more room in joint for manipulation of the
electrode.
E Electrode too large for joint. E Use smaller gauge electrode.
F Insufficient deposit time at
edge of weave.
F Pause for a moment at edge of weave to allow weld
metal buildup.
G Power Source is set for MIG
(GMAW) welding.
G Set Power Source to STICK (SMAW) mode.
Insufficient Gap
Incorrect Sequence
Art # A-05866_AC