E-flite 9.0-Gram Sub-Micro G90 Heading Lock Gyro User Manual
G90 sub-micro heading lock gyro instruction manual
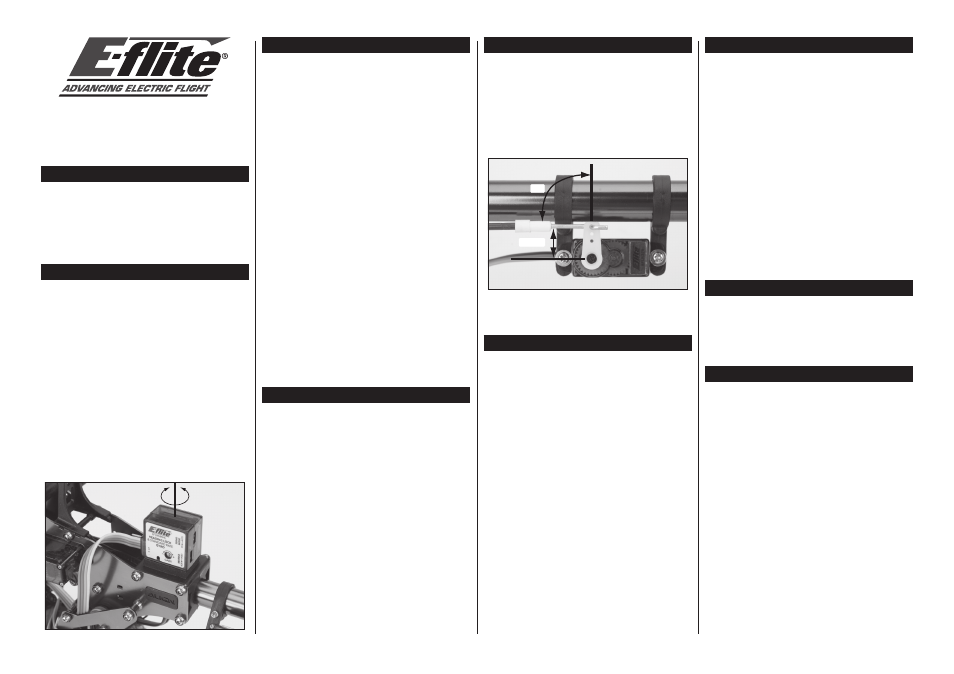
G90 Sub-Micro
Heading Lock Gyro
Instruction Manual
Introduction
The G90 Sub-Micro Heading Lock Gyro’s small size
(20 x 20 x 15mm) and low weight (9.0 grams, including leads
and connectors) make it an ideal choice for a wide variety of
micro and mini class electric helicopter models. With features
like analog and digital servo support, optional dual remote
gain adjustment and Heading Lock or Standard Rate Mode
selection capabilities, it offers locked-in tail performance
and adjustability perfect for the sport and 3D pilot alike.
Gyro Installation
When installing the G90, it is typically best to first refer
to your helicopter’s instruction manual for suggestions of
the location in which it should be mounted on the model.
If no suggestions are available, choose a solid location
free from vibration, in-line with the yaw axis of the model.
Also, be sure to keep the gyro away from heat generating
sources (like the motor and ESC) and other electronics.
When mounting the G90, be sure the side of the gyro with
the label is mounted vertically on the model (parallel to
the main shaft). The sides of the gyro without the leads
and switches are the top and bottom respectively. Also,
be sure to position the gyro so you can easily access the
gain setting adjustment pot (if not using the remote gain
adjustment option), reversing and servo mode switches.
Once you have found a suitable location, use a small amount
of isopropyl alcohol to clean the mounting area and gyro
where the foam mounting tape will be attached. Then,
use the included foam mounting tape to mount the gyro
securely on the model. It is important to use foam mounting
tape only as it helps to prevent vibration from adversely
affecting the performance and operating life of the gyro.
Gyro Connection(s) to Receiver
Single Mode Connection (Heading Lock Mode Only)
If you will
not
be utilizing the dual remote gain adjustment
and mode selection option to control gain values and mode
type from an auxiliary channel on the transmitter, it will only
be necessary to connect the Rudder Channel Lead of the gyro
(the connector with three wire leads) to the rudder channel
on the receiver. You will not need to connect the Auxiliary
Channel Lead of the gyro (the connector with one wire lead)
to the receiver, however, to be certain to secure it so it cannot
come into contact with any moving parts on the helicopter.
With just the rudder channel lead of the gyro connected
to the receiver, the gyro will operate in Heading Lock
Mode only. The gain value will then be adjusted using
the Gain Setting Adjustment Pot located on the gyro.
Dual Mode Connections
(Heading Lock and Standard Rate Mode)
If you have chosen to utilize the dual remote gain adjustment
and mode selection option to control gain values and mode type
from an auxiliary channel on the transmitter, it will be necessary
to connect the Rudder Channel Lead of the gyro (the connector
with three wire leads) to the rudder channel on the receiver,
and the Auxiliary Channel Lead of the gyro (the connector with
one wire lead) to the channel on the receiver that will be used
for controlling the gyro from the transmitter. For most radio
systems, it will be best to connect the Auxiliary Channel Lead
of the gyro to Channel 5 (also known as the Gear Channel) on
the receiver, ensuring the yellow wire lead is oriented properly
so it is plugged into the “signal” side of the receiver’s pins.
With both the rudder channel and auxiliary channel leads of
the gyro connected to the receiver, the gyro can be operated
in either the Heading Lock or Standard Rate Mode. Mode
selection and gyro gain settings will then be adjusted using
an auxiliary channel on the transmitter, and the Gain Setting
Adjustment Pot located on the gyro will be disabled.
Tail Servo Selection
Selection of a suitable tail servo is critical for obtaining
maximum performance from the gyro. A servo with
quick transit times (.15 sec/60° or faster) is preferred,
and will allow the G90 to perform to its full potential.
We suggest using the following servos in
their recommended applications:
• E-flite
®
S60 Super Sub-Micro Servo (EFLRS60)
– For sub-micro and micro helicopters
• E-flite S75 Sub-Micro Servo (EFLRS75)
– For micro and mini helicopters
• JR 3400G Mini Digital Heli Gyro Servo (JRPS3400G)
– For mini helicopters
Servo Arm and Pushrod Setup
After installing your chosen servo on the model, it will be best
to center the servo electronically using an open channel before
installing the servo arm and connecting the servo to the G90.
Once you have centered the servo electronically, choose a
servo arm that allows the tail rotor pushrod linkage or linkage
ball to be positioned approximately 8–11mm (typical for T-REX
and similar models) from the center of the servo’s output
gear/shaft. Then, install the servo arm on the servo, ensuring
it is perpendicular to the tail rotor pushrod linkage when in the
centered/neutral position. Also, be sure to remove any unused
portions of the servo arm to prevent any binding or obstruction.
8-11mm
90º
After installing the tail rotor pushrod linkage on the tail servo
arm, and ensuring the tail servo is still centered electronically,
adjust the length of the pushrod so the tail pitch slider is centered
on the tail rotor shaft, between the tail case and tail hub.
Servo Connection to Gyro
Once the tail servo, servo arm and linkage have been installed
on the model, it will be necessary to connect the servo to
the G90. Connect the servo lead to the servo connection
on the gyro (the three pins exiting the gyro case), ensuring
proper orientation and polarity direction of the wire leads
by following the markings on the label of the gyro:
S
= Signal wire lead connection location
+
= Positive wire lead connection location
–
= Negative wire lead connection location
Servo Mode Setting
Standard (STD) Servo Mode
If you are using an analog servo (like the E-flite S60 or
S75), be sure the Servo Mode switch located on the side of
the gyro is set to the Standard (STD) position for the best
possible performance. If it is set to the Digital Servo (DS)
position, the analog servo may not operate correctly and/or
will be damaged due to the high frame rate output of the gyro
when it is in the Digital Servo Mode.
Do not use analog
servos with the gyro set for Digital Servo Mode.
Digital (DS) Servo Mode
If you are using a digital servo (like the JR 3400G), be sure the
Servo Mode switch located on the side of the gyro is set to the
Digital Servo (DS) position for the best possible performance.
In the Digital Servo Mode, the gyro sends inputs to the servo at
a much higher rate than when in the Standard Servo Mode for
added performance and holding power. However, you must be
sure to use a digital servo that is capable of handling an input
pulse rate of 275Hz or higher (like JR and similar digital servos),
or the servo will not operate correctly and/or will be damaged
due to the high frame rate output of the gyro when it is in the
Digital Servo Mode.
Do not use digital servos that cannot
handle an input pulse rate of at least 275Hz, or analog
servos, with the gyro set for Digital Servo Mode.
Initial Transmitter Settings
After completing installation and connection of the G90 and
tail servo on the model, please proceed with confirming
the following initial settings in your transmitter:
• Set the rudder channel trim and sub-
trim (if available) to neutral
• Disable and inhibit any forms of Revolution (Revo) Mixing
Initializing the Gyro
Once you have confirmed the initial settings in the
transmitter, it will be necessary to power up and
initialize the gyro before proceeding with some of
the following setup and adjustment steps:
• Power the transmitter on first.
• Then, power the receiver and gyro on.
• After powering on the receiver and gyro, make
sure you do not move or sway the model and
allow it to remain motionless until the blue LED
on the gyro illuminates solidly, indicating the gyro
has initialized properly and is ready for use.
Note: It is extremely important you do not move or
sway the model after powering on the gyro and before
it initializes. The gyro must be allowed adequate time
to record the neutral position in order to initialize
for proper operation. If you accidentally move the
model after powering the gyro on, and before it has
initialized, power the model off and repeat the process
to power the model on and initialize the gyro properly.