Bendix, Ad-ip, Air dryer troubleshooting chart – Bendix Commercial Vehicle Systems AD-SP SYSTEM PURGE AIR DRYER 10/04 User Manual
Page 19
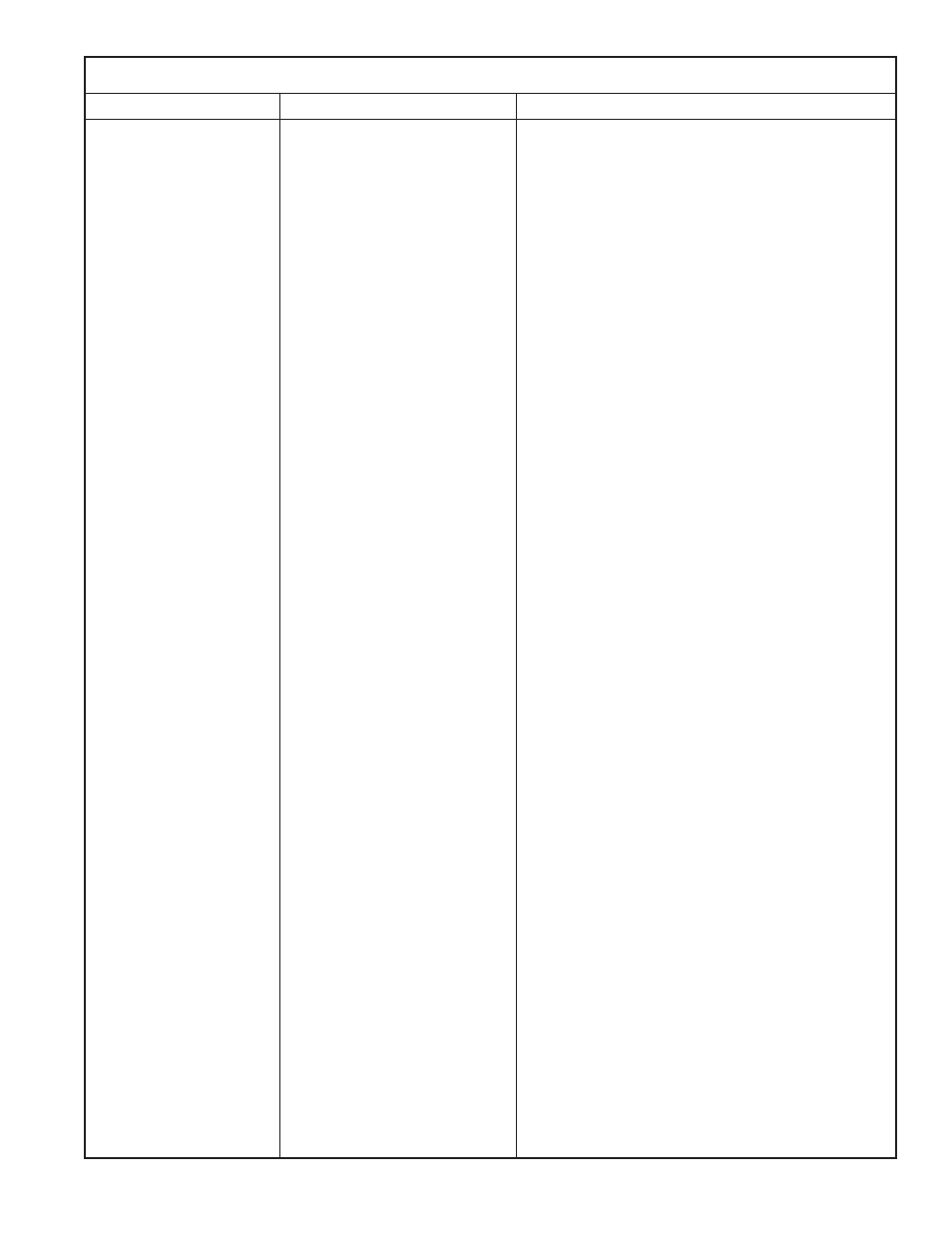
19
BENDIX
®
AD-IP
®
AIR DRYER TROUBLESHOOTING CHART
SYMPTOMS
CAUSE
REMEDY
1. Air dryer is constantly
“cycling” or purging.
Air dryer purges
frequently (every four
(4) minutes or less
while vehicle is idling)
(continued).
A. Excessive system leakage.
IMPORTANT: Note whether
air pressure loss is shown
on dash gauge(s). Pressure
loss
SHOWN on the gauges
is caused by service brake
system or component
leakage. Pressure loss
NOT SHOWN on gauges is
caused by supply system
or component leakage.
(continued)
1. Test fittings, hoses, lines and connections. Apply
soap solution to detect excessive leakage. Tighten or
replace as needed then repeat the air dryer charge-
purge cycle and observe the gauge installed in the
supply reservoir. If leakage is within limits, remove
the gauge from the reservoir and replace drain cock
or valve. If excessive leakage is detected, continue
testing.
2. Test the accessories connected to the supply
reservoir. Drain all air pressure from system,
disconnect all air lines leading to accessories (fan
clutch, wipers, air seats, etc.) and plug the reservoir
at the disconnection point. Build the air system
pressure until the air dryer purges and observe
the supply reservoir gauge. If leakage is no longer
excessive, repair or replace the leaking accessory.
If excessive leakage is detected, continue testing.
3. Test for governor leakage. Build the system pressure
to the governor cut-out, turn off the engine and apply
a soap solution to governor exhaust port and around
the cap. Leakage should not exceed a one (1) inch
bubble in five (5) seconds. Reduce the system
pressure to 80 psi, or less, and re-apply the soap
solution. Leakage should not exceed a one (1) inch
bubble in five (5) seconds. If excessive leakage is
detected in either test, repair or replace the governor.
4. Test the compressor unloader leakage. Drain all air
pressure from the system and remove the governor
from the compressor. Temporarily plug the governor
unloader port or air line that mated with, or connected
to, the compressor. Build the air system pressure until
the air dryer purges then IMMEDIATELY SHUT OFF
THE ENGINE. Observe the air gauge in the supply
reservoir. If the leakage is within limits, replace the
compressor unloaders. Re-connect the governor to
the compressor (after removing the plug installed in
the governor) and retest while observing the supply
reservoir gauge. If excessive leakage is detected,
continue testing.
5. Test the air dryer purge valve and outlet (delivery)
check valve. Drain all air pressure from the system.
Remove the control line connection at the air
dryer and plug the end of the air line leading to the
governor (not the air dryer control port). Build the
system pressure to governor cut-out and observe the
air gauge. If little or no pressure drop is observed,
replace the air dryer check valve. If a pressure drop
continues, apply a soap solution to the air dryer
purge exhaust and purge control port (where the
control line was removed). Leakage should not
exceed a one (1) inch bubble in five (5) seconds.
If leakage is excessive, repair or replace the purge
valve assembly.