2 isolation techniques – Rockwell Automation Safety Guidelines for the Application, Installation, and Maintenance of Solid-State Control User Manual
Page 11
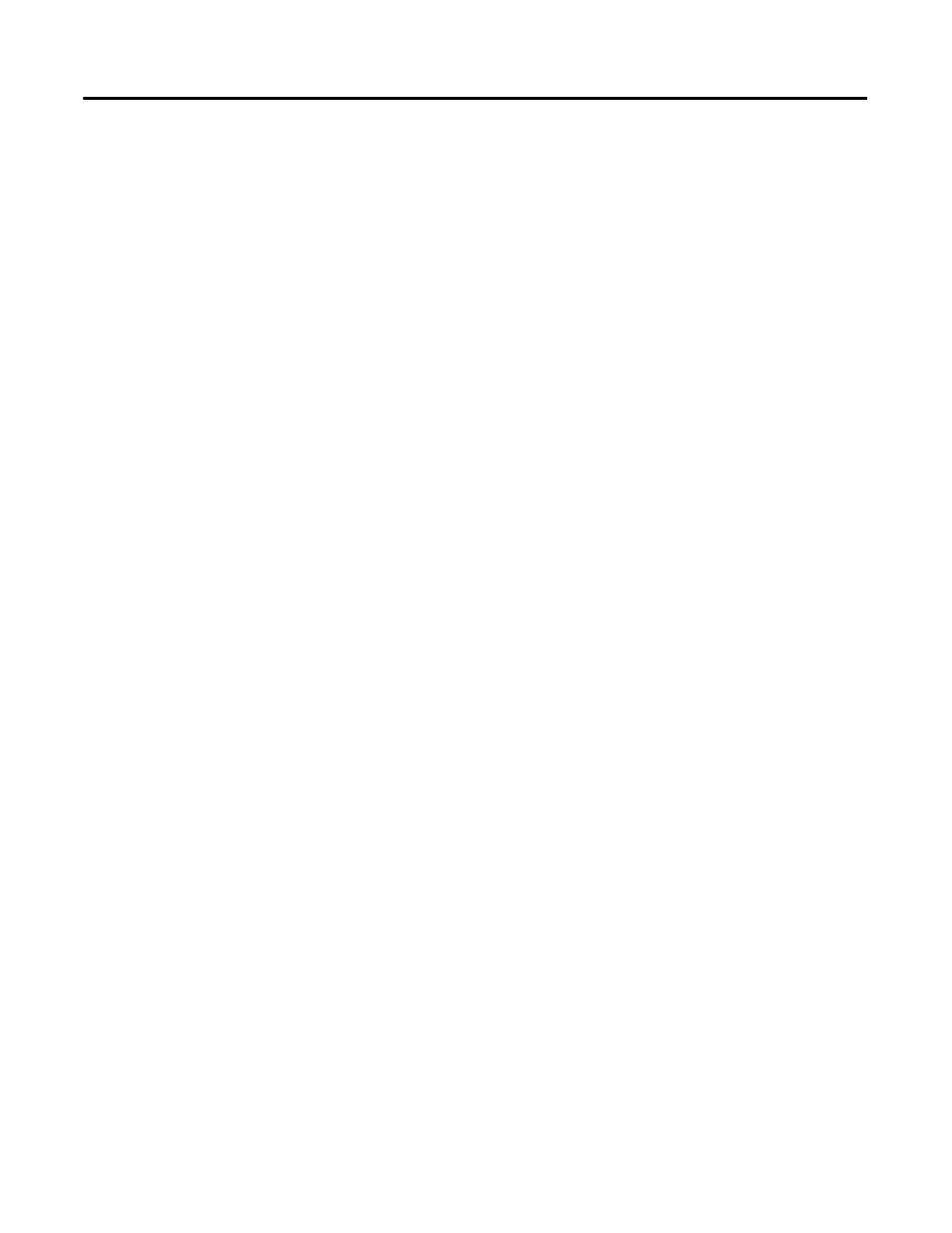
Publication SGI-1.1 - August 2009
Section 3: Application Guidelines
11
3.2.2 Isolation Techniques
The most important function of isolation components is to separate high level
circuits from low level circuits in order to protect against the transfer of a fault
from one level to the other.
Isolation transformers, pulse transformers, reed relays, or optical couplers are
typical means to transmit low level logic signals to power devices in the high
level circuit. Isolation impedance means also are used to transmit logic signals
to power devices.
Comments: 3.2.2 — Isolation Techniques
In addition to utilizing the various components discussed in the left column,
specific wiring techniques should be applied to assure separation of power
circuit wires from logic circuit wires. If at all possible, logic wires should be run
in a conduit that is segregated for that purpose only. Multiple conductors in a
shielded cable is an appropriate substitute for separate conduits. Another
common practice is to run the logic signals through twisted pairs of wire.
Regardless of the circumstances, wires carrying logic signals should never be
wrapped in the same bundle with wires that carry power signals.
3.3 Special Application
Considerations
3.3.1 Converting Ladder Diagrams
Converting a ladder diagram originally designed for electromechanical systems
to one using solid-state control must account for the differences between
electromechanical and solid-state devices. Simply replacing each contact in the
ladder diagram with a corresponding solid-state "contact" will not always
produce the desired logic functions or fault detection and response. For
example, in electromechanical systems, a relay having a mechanically linked
normally open (N.O.) and normally closed (N.C.) contact can be wired to
check itself. Solid-state components do not have a mutually exclusive
N.O.-N.C. arrangement. However, external circuitry can be employed to
sample the input and "contact" state and compare to determine if the system is
functioning properly.
Comments: 3.3.1 —Converting Ladder Diagrams
The example cited in this section of the NEMA Standard illustrates only
one of a number of reasons for special care in converting an
electromechanical (relay) ladder diagram to a programmable controller
(PC) program. Some other basic considerations are:
A PC program is an instruction to the PC’s central processing unit to allow
it to perform the logic functions and sequences for a particular
application. Typically, the PC’s logic level components are electrically
isolated from the actual input, sensor and actuator devices, as contrasted
with electromechanical controls which usually include contacts and coils
of the actual plant floor devices in the control schematic. Therefore a PC
program normally functions as open-loop control, unless feedback loops
from the plant floor devices to separate inputs of the PC are provided and
programmed to cause corrective action if inconsistencies are detected.