2 bus error – Rockwell Automation 57C400-1 115V AC/DC Input Module User Manual
Page 21
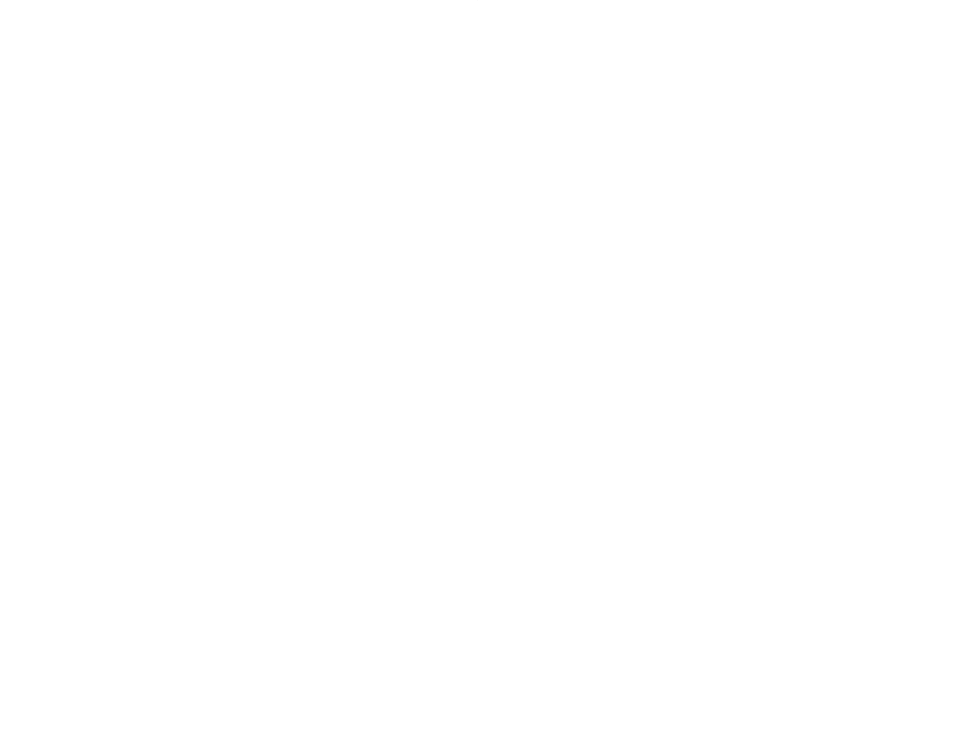
5Ć3
5.2
Bus Error
Problem: A 31" or 51" through 58" appears on the processor
module's LED. This error message indicates that there was a bus
error when the system attempted to access the module. The possible
causes of this error are a missing module, a module in the wrong
slot, or a malfunctioning module. It is also possible that the user is
attempting to write to registers on the module. Refer to the DCS5000
Processor Module Instruction Manual (JĆ3635) or AutoMax Processor
Module Instruction Manual (JĆ3650) for more information. Use the
following procedure to isolate a bus error:
Step 1.
Verify that the input module is in the correct slot and that
the I/O definitions are correct.
Refer to figure 3.2. Verify that the slot number being
referenced agrees with the slot number defined in the
configuration task. Verify that the register number and bit
number are correct.
For remote I/O installations, also verify that the master slot
and remote drop number are defined correctly.
Step 2.
Verify that the module can be accessed.
Connect the programming terminal to the system and run
the ReSource Software. Use the I/O MONITOR function to
display register 0. If the programmer is able to monitor the
inputs, the problem lies in the application software
(proceed to step 3). If the programmer cannot monitor the
inputs, the problem lies in the hardware (proceed to step
4).
Step 3.
Verify that the user application program is correct.
This module cannot be written to. If a BASIC task caused
the bus error, the error log will contain the statement
number in the task where the error occurred. If a ladder
logic or control block task caused the error, you will need
to search the task for any instances where you used an
input as a ladder logic coil or wrote to it in a control block
task.
Step 4.
Verify that the hardware is working correctly.
Verify the hardware functionality by systematically
swapping out the input module, processor module(s), and
backplane. After each swap, if the problem is not
corrected, replace the original item before swapping out
the next item.
For remote I/O installations, systematically swap out the
input module, the slave remote module, and the
backplane. After each swap, if the problem is not
corrected, replace the original item before swapping out
the next item.