Wiring guidelines, Input devices, Transducer source impedance – Rockwell Automation 1746-NI8 SLC 500 Analog Input Module Instructions User Manual
Page 15
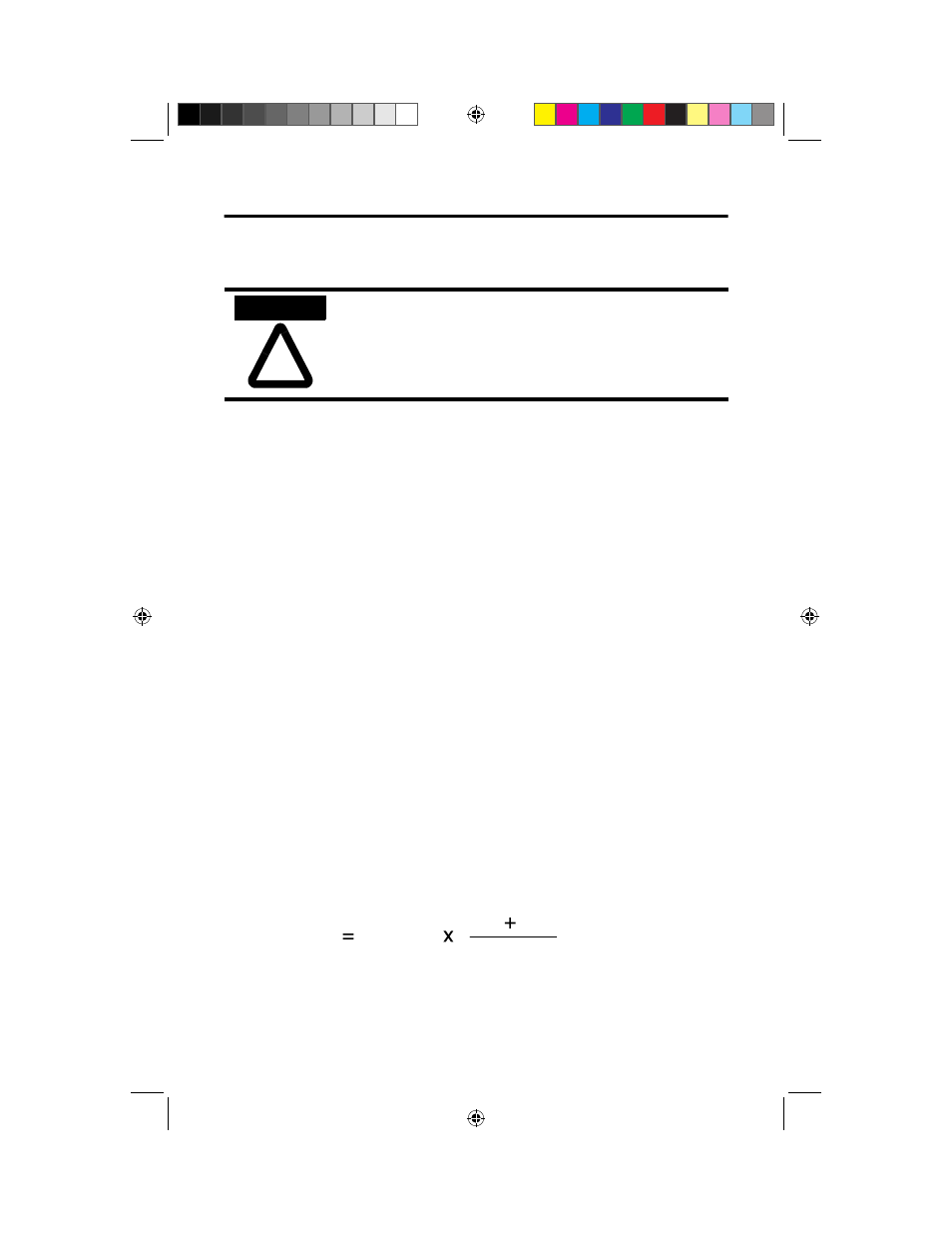
SLC 500™ Analog Input Module 15
Publication 1746-IN006A-US-P
Wiring Guidelines
Follow the guidelines below when planning your system wiring.
• To limit noise, keep signal wires as far away as possible from power and load lines.
• To ensure proper operation and high immunity to electrical noise, always use
Belden™ 8761 (shielded, twisted-pair) or equivalent wire.
• Connect the shield drain wire to the shield terminal on the 1746-NI8 module.
Up to four shield wires may be connected to each shield screw terminal that
provides a connection to chassis ground.
• Tighten terminal screws using a screwdriver. Each screw should be turned tight
enough to immobilize the wire’s end. Excessive tightening can strip the terminal
screw. The torque applied to each screw should not exceed 0.9 Nm (8 in-lb) for
each terminal.
• Follow system grounding and wiring guidelines found in your SLC 500 Modular
Hardware Style Installation and Operation Manual, publication 1747-6.2.
Input Devices
Transducer Source Impedance
If the source impedance of the input device and associated cabling is too high, it
affects the accuracy of the channel data word. Source impedance of 500 ohms
produces up to 0.05% of module error over and above the specified accuracy of the
module.
You can compensate for device impedance error by implementing the following
equation in your ladder program:
!
ATTENTION
To prevent shock hazard, care should be taken when wiring the
module to analog signal sources. Before wiring any analog
module, disconnect power from the SLC 500 system and from
any other source to the analog module.
V
S
V
measured
(R
s
R
in
)
R
in
where:
Vs = input device voltage
Rs = input device impedance
Rin = 1746-NI8 input impedance (See Specifications on page 17.)
@JO"VTQQE
@JO"VTQQE
".
".